钛及钛合金检测的重要性与核心检测项目
钛及钛合金因其优异的强度重量比、耐腐蚀性和生物相容性,被广泛应用于航空航天、医疗植入、化工设备及海洋工程等领域。然而,材料的性能高度依赖于其成分纯度、加工工艺及微观结构特性。若原材料存在杂质超标、加工缺陷或热处理不当等问题,可能导致材料脆化、耐蚀性下降或疲劳寿命缩短,进而引发严重的安全隐患。因此,针对钛及钛合金的检测是确保其性能达标、延长使用寿命的关键环节。以下将详细解析钛及钛合金检测的核心项目及其技术要点。
一、化学成分分析
钛合金的化学成分直接影响其力学性能与耐蚀性。检测时需通过光谱分析法(如ICP-OES、XRF)对主元素(钛含量)、合金元素(如铝、钒、钼等)及杂质(氧、氮、氢、碳)进行定量分析。例如,氧含量过高会显著降低材料的塑性和韧性,而氢含量超标可能导致氢脆现象。
二、力学性能测试
通过拉伸试验、硬度测试(布氏/维氏/洛氏)、冲击试验及断裂韧性测试,评估材料的抗拉强度、屈服强度、延伸率及抗冲击能力。例如,航空级TC4钛合金(Ti-6Al-4V)的典型抗拉强度需达到≥895 MPa,延伸率≥10%。
三、微观组织观察
利用金相显微镜、扫描电镜(SEM)等设备分析材料的晶粒度、相组成及缺陷分布。α相与β相的占比及形态直接影响钛合金的强度与塑性,而热处理工艺的异常可能导致晶界析出不均匀的化合物。
四、无损检测(NDT)
采用超声检测(UT)、射线检测(RT)和渗透检测(PT)等非破坏性方法,识别材料内部的气孔、裂纹、夹杂等缺陷。例如,航空航天部件要求超声检测灵敏度达到Φ0.4mm平底孔当量。
五、耐腐蚀性评价
通过盐雾试验、电化学极化曲线测试及酸碱浸泡实验,模拟材料在海洋环境或化工介质中的耐蚀表现。医用钛合金还需进行细胞毒性测试,确保其生物相容性符合ISO 10993标准。
六、尺寸与表面质量检测
使用三坐标测量仪、轮廓仪等设备验证加工件的尺寸公差与形位精度,同时对表面粗糙度(Ra值)、氧化层厚度及微裂纹进行量化分析,避免应力集中引发的早期失效。
七、热处理工艺验证
对退火、固溶时效等热处理后的材料进行残余应力检测(X射线衍射法)和相变温度测定(DSC分析),确保工艺参数符合设计要求。
通过上述系统性检测,可全面评估钛及钛合金的理化性能与加工质量,为材料选型、工艺优化及故障分析提供科学依据。随着增材制造(3D打印钛合金)等新技术的推广,检测项目还需结合孔隙率分析、层间结合强度测试等新兴需求,持续完善技术标准体系。
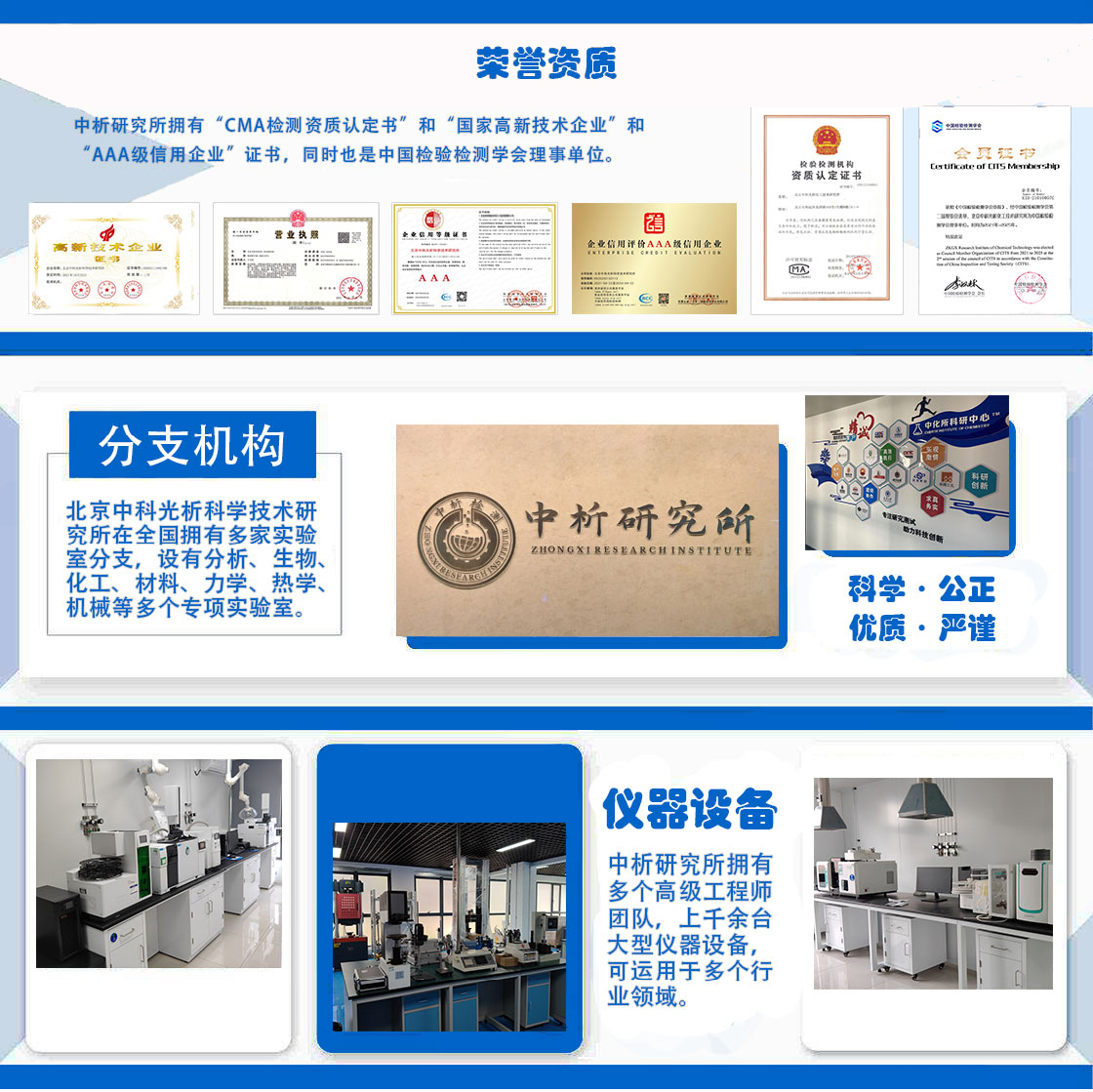
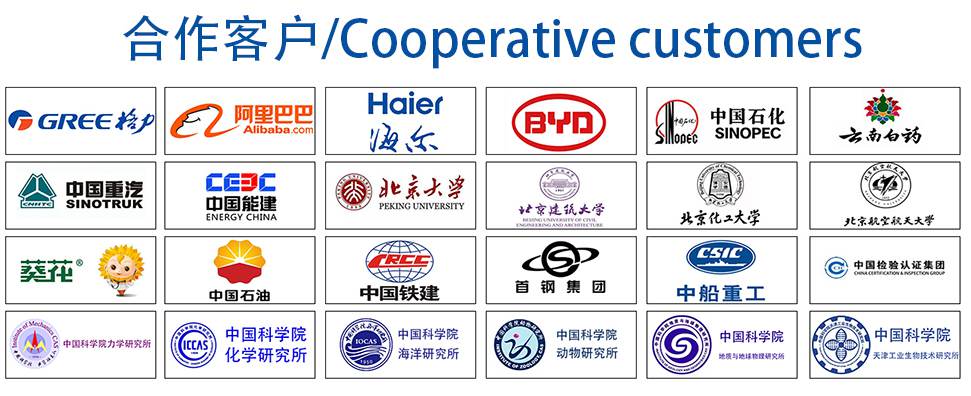