焊接结构检测的重要性与关键内容
焊接结构作为现代工业中广泛应用的关键承力部件,其质量直接关系到设备安全性、使用寿命和整体性能。从桥梁、建筑到压力容器、船舶制造,焊接工艺的可靠性需要通过科学系统的检测手段来保障。焊接结构检测的目的是发现焊缝及热影响区的潜在缺陷(如裂纹、气孔、夹渣等),评估焊接接头的力学性能是否符合设计要求,并为后续修复或验收提供数据支撑。随着行业标准的严格化和自动化焊接技术的普及,检测方法也在不断迭代,结合传统手段与新型技术形成全面的质量控制体系。
焊接结构检测的核心项目与方法
1. 外观质量检测
作为检测的首要环节,外观检查通过目视或放大镜观察焊缝表面状态。重点关注焊道成型是否规整、是否存在咬边、焊瘤、飞溅等表观缺陷,同时记录焊缝余高、宽度是否符合工艺文件要求。根据GB/T 3375-2018《焊接术语》标准,需对焊缝表面进行100%覆盖检查。
2. 无损检测(NDT)技术
无损检测是发现内部缺陷的核心手段,主要包括以下方法:
- 超声波检测(UT):利用高频声波反射原理检测焊缝内部裂纹、未熔合等缺陷,适用于厚板结构
- 射线检测(RT):通过X射线或γ射线成像技术显示焊缝内部气孔、夹渣等体积型缺陷
- 磁粉检测(MT):针对铁磁性材料表面及近表面裂纹检测,灵敏度可达微米级
- 渗透检测(PT):适用于非多孔材料表面开口缺陷的显像检测
3. 力学性能测试
通过破坏性试验验证焊接接头的承载能力,包括:
- 拉伸试验:测定接头抗拉强度和断口位置
- 弯曲试验:评估焊缝塑性变形能力
- 冲击试验:测试低温环境下的韧性指标
- 硬度测试:分析热影响区组织变化
4. 金相分析与化学成分检测
采用显微组织观察手段检查焊缝金属的晶粒度、相组成及夹杂物分布,结合光谱分析验证焊材成分是否符合标准。对于不锈钢、铝合金等特殊材料,还需进行晶间腐蚀敏感性试验。
5. 尺寸精度与变形量测量
使用三维坐标仪、激光扫描仪等设备检测焊接结构的几何精度,重点控制角变形、波浪变形等引起的尺寸偏差。依据ASME BPVC或EN 1090标准设定允许公差范围。
检测流程的标准化管理
完整的焊接结构检测应遵循PDCA循环:从焊接工艺评定(WPS/PQR)→过程参数监控→成品检测→数据归档的全流程质量控制。检测报告需包含缺陷类型、位置坐标、评级结果及返修建议,同时建立数字化检测档案以满足可追溯性要求。
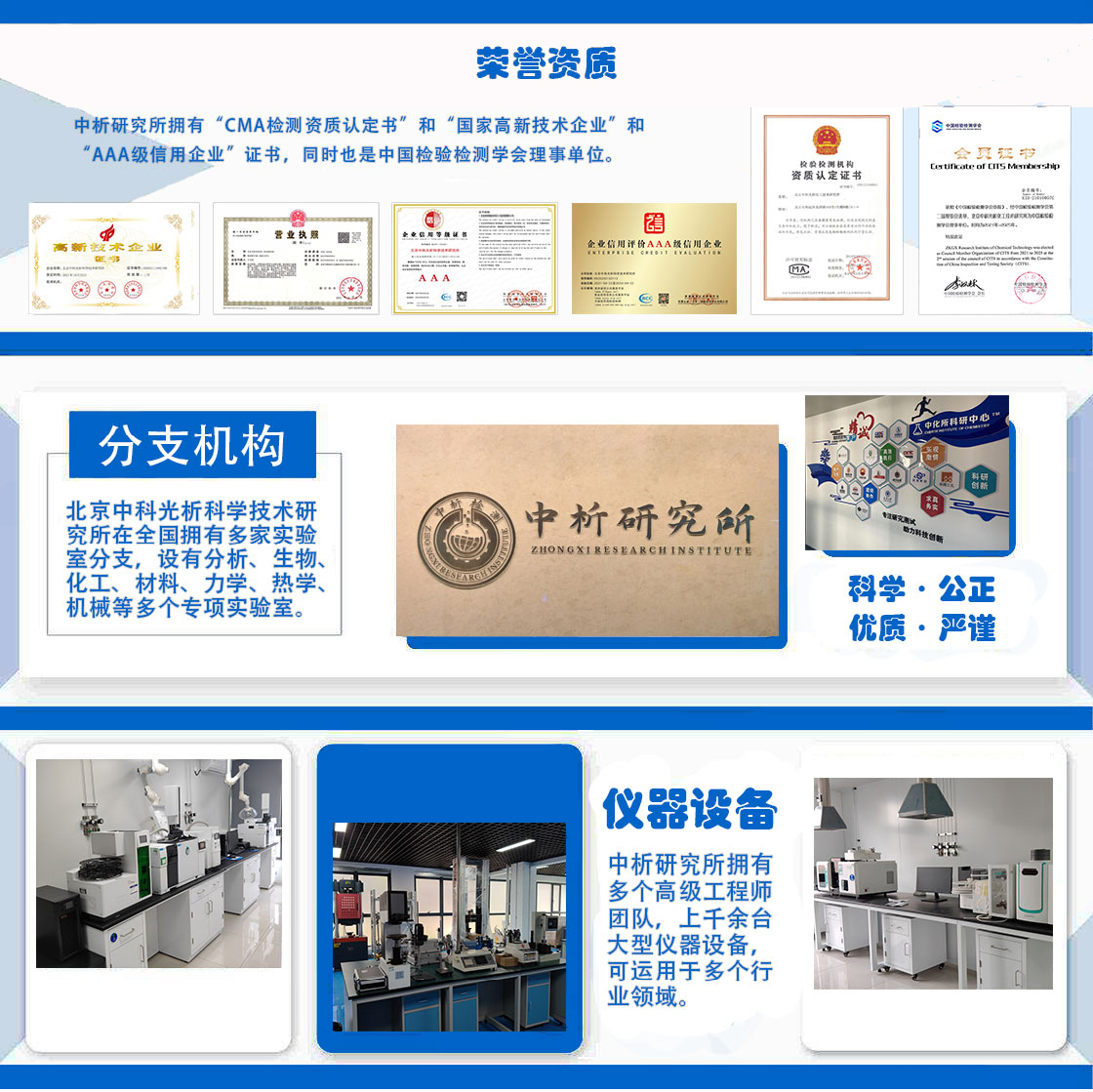
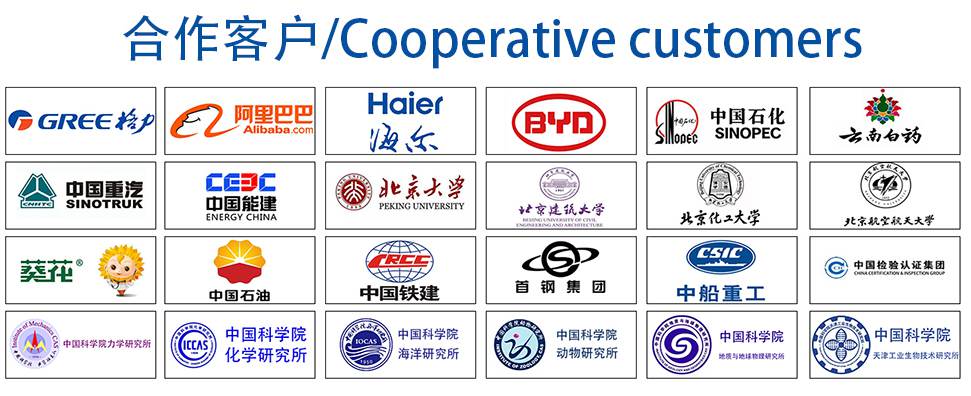