油气田用封隔器检测的重要性与核心内容
在油气田开发中,封隔器作为井下关键工具,承担着隔离不同地层、控制流体流动、保障井筒完整性的核心作用。其性能直接关系到油气井的生产效率、作业安全及环境保护。由于封隔器长期处于高温、高压、腐蚀性介质的复杂工况中,若出现密封失效或机械损伤,可能导致井喷、地层污染等重大事故。因此,通过科学、系统的检测手段评估封隔器的可靠性,已成为油气田设备管理流程中不可或缺的环节。
核心检测项目及技术要求
1. 机械性能检测
包括抗压强度、抗拉强度、抗扭强度测试,需模拟井下实际载荷条件。通过万能材料试验机和扭矩测试仪,验证封隔器主体结构及卡瓦系统的承载能力,确保其在极端压力下不发生塑性变形或断裂。
2. 密封性能检测
采用气密性试验和液压试验相结合的方式,测试封隔器胶筒在设定压差下的密封效果。需满足API 11D1标准要求,包括:
- 静态密封测试(72小时无泄漏)
- 动态交变压力测试(100次循环后性能保持率≥95%)
- 高温老化后密封性能评估
3. 耐腐蚀性能检测
通过电化学测试、盐雾试验及酸性介质浸泡实验,评价封隔器金属部件在H2S/CO2环境中的抗腐蚀能力。重点检测应力腐蚀开裂敏感性,要求材料腐蚀速率≤0.1mm/年。
齐全检测技术的应用
现代检测体系融合了多项前沿技术:
- 超声相控阵技术:实现胶筒内部缺陷的3D成像检测
- 数字图像相关技术(DIC):实时监测加载过程中的应变分布
- 有限元仿真分析:预测复杂工况下的应力集中区域
- 智能传感器系统:实现井下工作状态的实时监测
质量控制与标准化流程
检测过程严格遵循API、ISO及SY/T行业标准,建立从原材料入厂到成品出厂的全生命周期质量档案。关键控制节点包括:
- 原材料化学成分及力学性能复验
- 关键工序的在线无损检测
- 整机组装后的功能验证测试
- 第三方权威机构认证
通过完善的检测体系,可确保封隔器在苛刻工况下的使用寿命达到设计要求的8-10年,将现场故障率降低至0.5%以下。
上一篇:水与涉水产品(理化)检测下一篇:消毒产品(毒理)检测
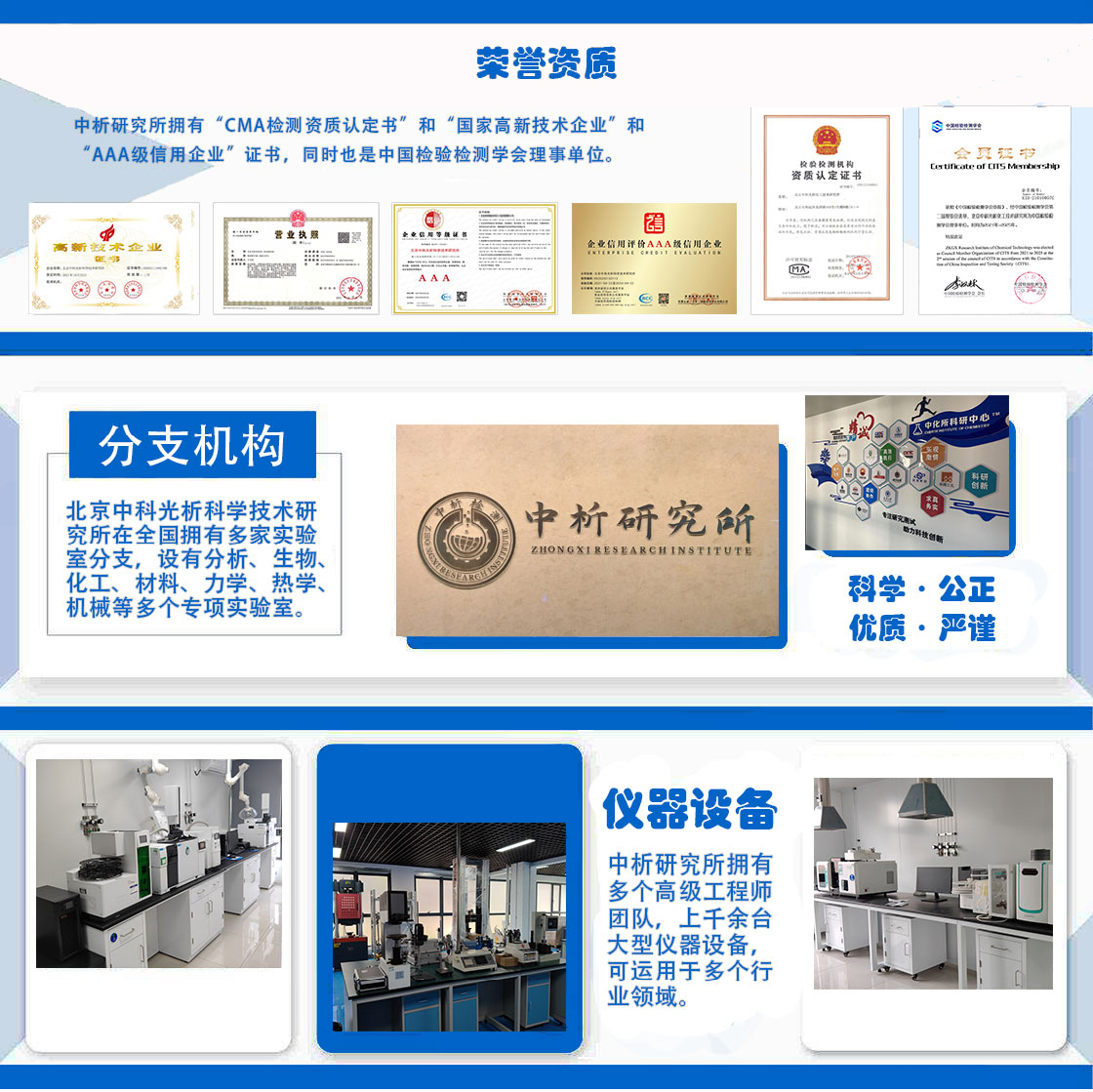
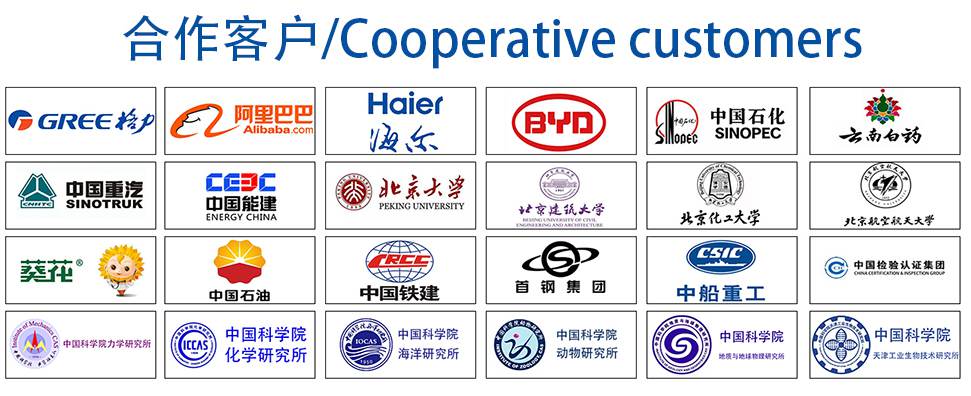
材料实验室
热门检测
14
16
16
20
22
18
20
17
14
17
17
21
18
15
20
22
18
19
25
18
推荐检测
联系电话
400-635-0567