钢制连续抽油杆检测的重要性
钢制连续抽油杆作为油田开采中举升系统的核心部件,承担着传递动力、输送原油的重要功能。其长期在高温、高压、腐蚀性介质及交变载荷环境下工作,容易出现疲劳裂纹、磨损、腐蚀等缺陷。若未及时检测发现,可能导致杆体断裂、油井停产甚至安全事故。因此,通过科学的检测手段对抽油杆的几何尺寸、力学性能、表面质量等进行全面评估,是保障油田生产安全和效率的关键环节。
核心检测项目及方法
1. 尺寸精度检测
使用游标卡尺、激光测径仪等工具对抽油杆的直径、椭圆度、直线度进行测量,确保符合API 11B标准要求的公差范围。重点检查杆体过渡段的尺寸变化,避免应力集中现象。
2. 力学性能测试
通过拉伸试验机测定抗拉强度、屈服强度及延伸率,依据ASTM E8标准进行测试;采用冲击试验机评估材料韧性,检测低温环境下的冲击吸收功是否达标。
3. 表面质量检验
借助磁粉探伤(MT)或渗透探伤(PT)检测表面裂纹、折叠等缺陷,使用表面粗糙度仪评估涂层均匀性。对螺纹连接部位进行三维形貌扫描,确认齿形精度和啮合状态。
4. 无损检测(NDT)
采用超声波检测(UT)探明内部夹杂、分层等缺陷,使用电磁涡流检测评估近表面损伤。对服役中的抽油杆实施在线磁记忆检测,预警早期应力集中区域。
5. 腐蚀防护检测
通过盐雾试验评估镀层耐蚀性,采用电化学工作站测试极化曲线,分析涂层防护性能。对已服役杆体进行金相分析,观察腐蚀产物类型及扩展形态。
6. 疲劳寿命评估
通过旋转弯曲疲劳试验模拟实际工况,结合断口形貌分析确定失效模式。运用有限元分析软件建立力学模型,预测剩余使用寿命。
7. 连接可靠性验证
对抽油杆接箍进行扭矩-拉力复合试验,检测螺纹副的承载能力和密封性。使用数字图像相关技术(DIC)观测连接部位的应变分布特征。
检测标准与规范
检测过程需严格遵循API SPEC 11B《抽油杆规范》、SY/T 5029《抽油杆及接箍》等行业标准,同时参考ISO 10407《石油天然气工业-钻杆检验》的相关要求。针对特殊工况需制定个性化检测方案,如高含硫油气井需增加氢致开裂(HIC)试验。
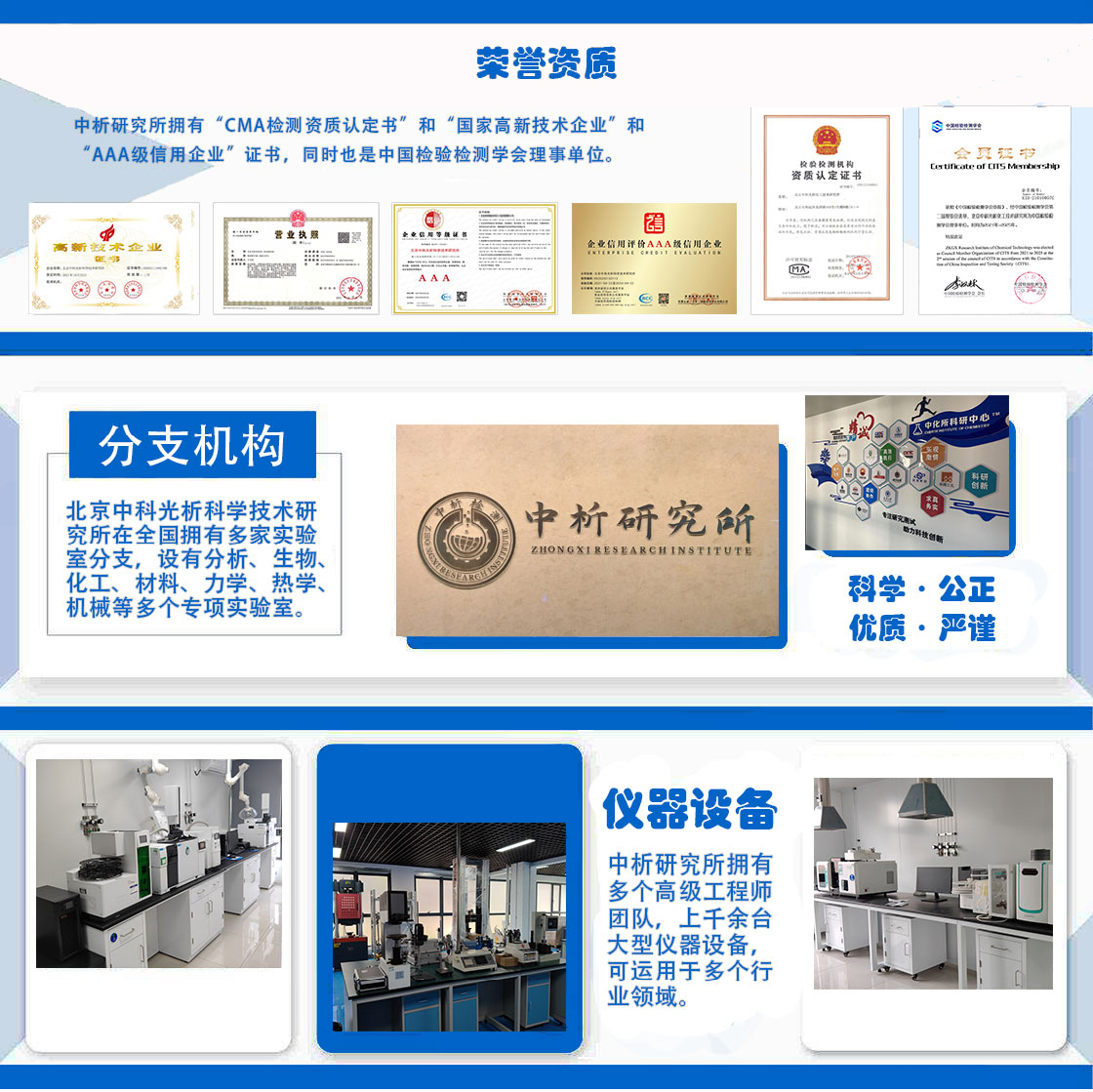
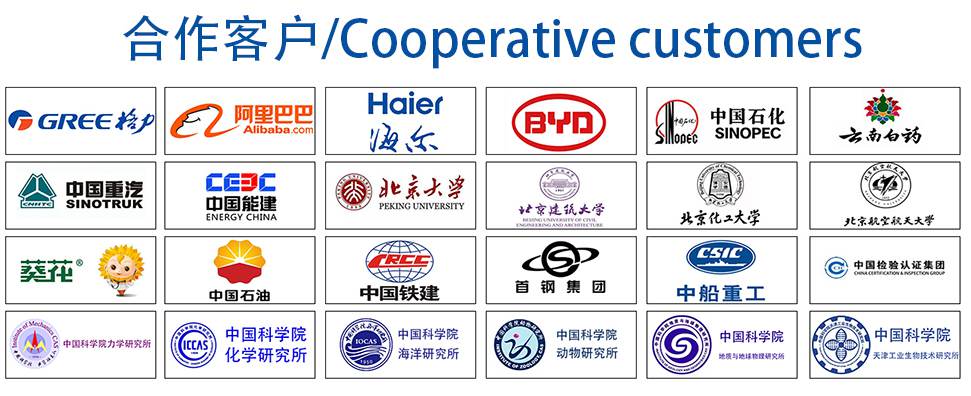