锻压机械(参数)检测的重要性及核心内容
锻压机械作为金属成形加工的核心设备,广泛应用于汽车制造、航空航天、模具生产等领域。其性能参数直接影响产品质量、生产效率和设备安全性。通过系统化的参数检测,能够确保设备符合国家技术标准(如GB 17120《锻压机械安全技术条件》及GB/T 23281《锻压机械噪声限值》),同时延长设备使用寿命,降低故障风险。本文将从关键检测项目出发,详细解析锻压机械参数检测的技术要点与执行规范。
一、精度与成型能力检测
1. 滑块行程精度:使用激光干涉仪测量滑块上下止点位置偏差,确保重复定位精度≤±0.05mm;
2. 合模平行度检测:通过千分表在模具四角测量闭合状态下的平行度误差,目标值≤0.02mm/m;
3. 公称力验证:采用动态力传感器测试最大锻压力输出,误差需控制在标称值的±5%以内。
二、动力系统性能检测
1. 液压系统检测:包含油压稳定性(波动≤1MPa)、油温控制(55±5℃)、泄漏量(每分钟≤3滴);
2. 气压传动测试:验证气缸响应时间(≤0.3秒)及保压性能(10分钟内压降≤5%);
3. 电机功率匹配度:通过电能质量分析仪检测电机负载率(65-90%为最佳区间)。
三、结构强度与稳定性检测
1. 机身刚度测试:施加1.25倍公称力进行静态变形检测,立柱挠度应<0.15mm/m;
2. 振动频率分析:采用加速度传感器采集设备运行时的振动频谱,避免共振风险;
3. 关键部件探伤:对曲轴、连杆等承力部件实施磁粉/超声波探伤,排查微观裂纹缺陷。
四、安全装置有效性验证
1. 急停响应测试:触发急停按钮后设备全停时间≤0.5秒;
2. 光电保护装置检测:模拟异物侵入时防护响应时间≤20ms;
3. 过载保护校验:设置110%公称力时保护系统应准确切断动力输出。
五、辅助系统参数检测
1. 润滑系统检测:油路压力(0.2-0.5MPa)、润滑油温升(≤15℃/h);
2. 冷却系统效率:单位时间换热能力需满足连续工作温控要求;
3. 噪声与粉尘监测:按GB/T 23281标准,距设备1m处噪声值≤85dB(A)。
检测周期与数据管理要求
建议每6个月进行常规检测,大修后需做全面参数校验。检测数据应建立电子档案,运用MES系统实现趋势分析,对关键参数(如滑块精度、液压效率)设置预警阈值,实现预测性维护管理。通过数字化检测手段,企业可降低30%以上的非计划停机损失,同时提升产品合格率2-3个百分点。
锻压机械的精准检测不仅是合规要求,更是企业提质增效的核心保障。随着智能传感技术和工业物联网的发展,参数检测正朝着在线监测、实时反馈的方向演进,为锻造行业智能化升级奠定技术基础。
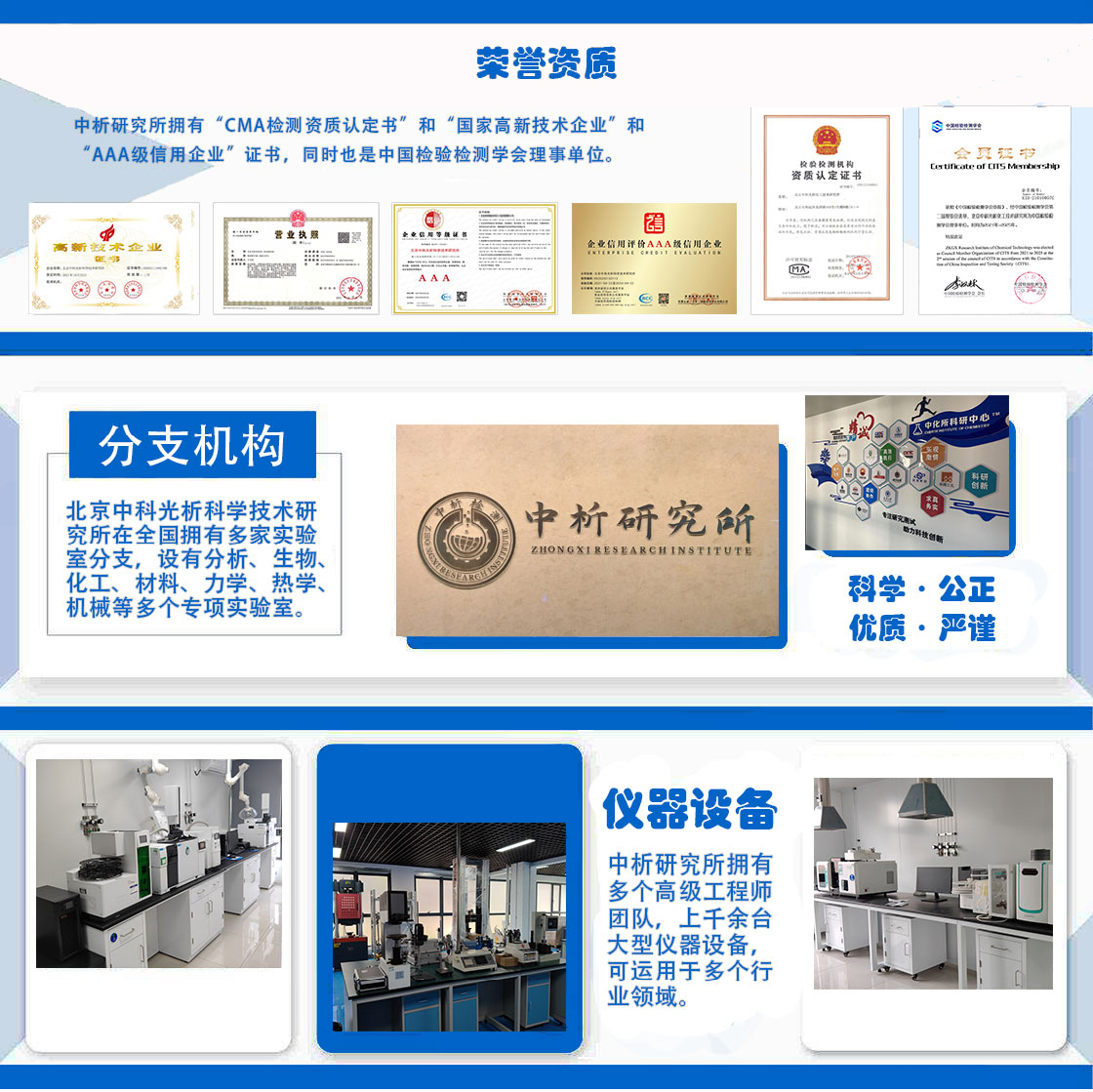
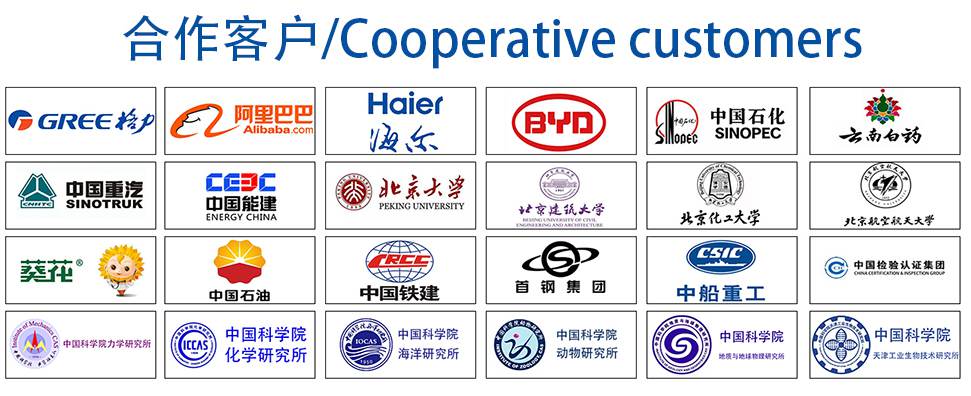