轴承座检测:全面把控机械基础件质量的核心环节
在机械传动系统中,轴承座作为承载和固定轴承的关键部件,其质量直接影响到设备的运行精度、使用寿命及安全性。随着现代工业对设备可靠性要求的不断提升,轴承座检测已成为机械制造和维保过程中的重要质量控制环节。专业化的检测体系不仅能够及时发现生产缺陷,更能通过数据化分析为产品优化提供科学依据,确保轴承座在复杂工况下保持稳定的支撑性能和精准的配合特性。
核心检测项目体系
1. 尺寸精度检测
使用三坐标测量仪、投影仪等精密仪器,对安装孔径、同轴度、平行度、垂直度等关键尺寸进行三维检测。重点验证轴承座内孔直径公差是否满足H7级精度要求,定位止口与安装面的垂直度误差控制在0.02mm/m以内。
2. 表面质量检测
通过目视检查配合磁粉探伤,检测铸造或机加工表面是否存在裂纹、气孔、砂眼等缺陷。使用表面粗糙度仪测量关键配合面的Ra值,确保轴承安装面粗糙度≤1.6μm,油封接触面≤3.2μm。
3. 材料性能测试
采用光谱分析仪进行材料成分验证,确保符合HT250/GG25等牌号要求。通过布氏硬度计检测本体硬度(180-240HB),冲击试验机验证材料韧性,金相分析评估铸件石墨形态及基体组织。
4. 配合特性检测
使用液压拉伸装置模拟轴承压装过程,检测过盈配合的轴向压装力曲线。采用激光对中仪测量轴承座与轴系的同轴度,确保径向跳动量≤0.05mm,端面跳动≤0.03mm。
5. 密封性能测试
对带密封结构的轴承座进行IP防护等级测试,使用气压检漏仪检测防尘防水性能。润滑系统接口需经受1.5倍工作压力的保压试验,30分钟内压力降不超过5%。
6. 动态性能验证
在专用试验台上进行模拟工况测试,监测高速运转时的振动值(≤4.5mm/s)、温升变化(ΔT≤35℃)及噪音水平。通过200小时耐久试验评估疲劳强度,检测微动磨损和变形情况。
智能化检测发展趋势
当前行业正加速推进数字化检测技术应用,基于机器视觉的自动尺寸检测系统可实现100%在线全检,检测效率提升3倍以上。结合大数据分析的预测性质量控制系统,能够实时监控生产波动,自动优化加工参数。采用相控阵超声检测技术,可精确识别铸件内部3mm以上缺陷,检测精度较传统方法提高40%。
科学的检测体系应建立全过程质量追溯机制,从原材料入厂到成品出厂形成完整的检测数据链。建议企业参照ISO/TS 16949标准建立检测规范,结合工况特点制定分级检测方案,在保证质量可靠性的同时实现成本最优配置。
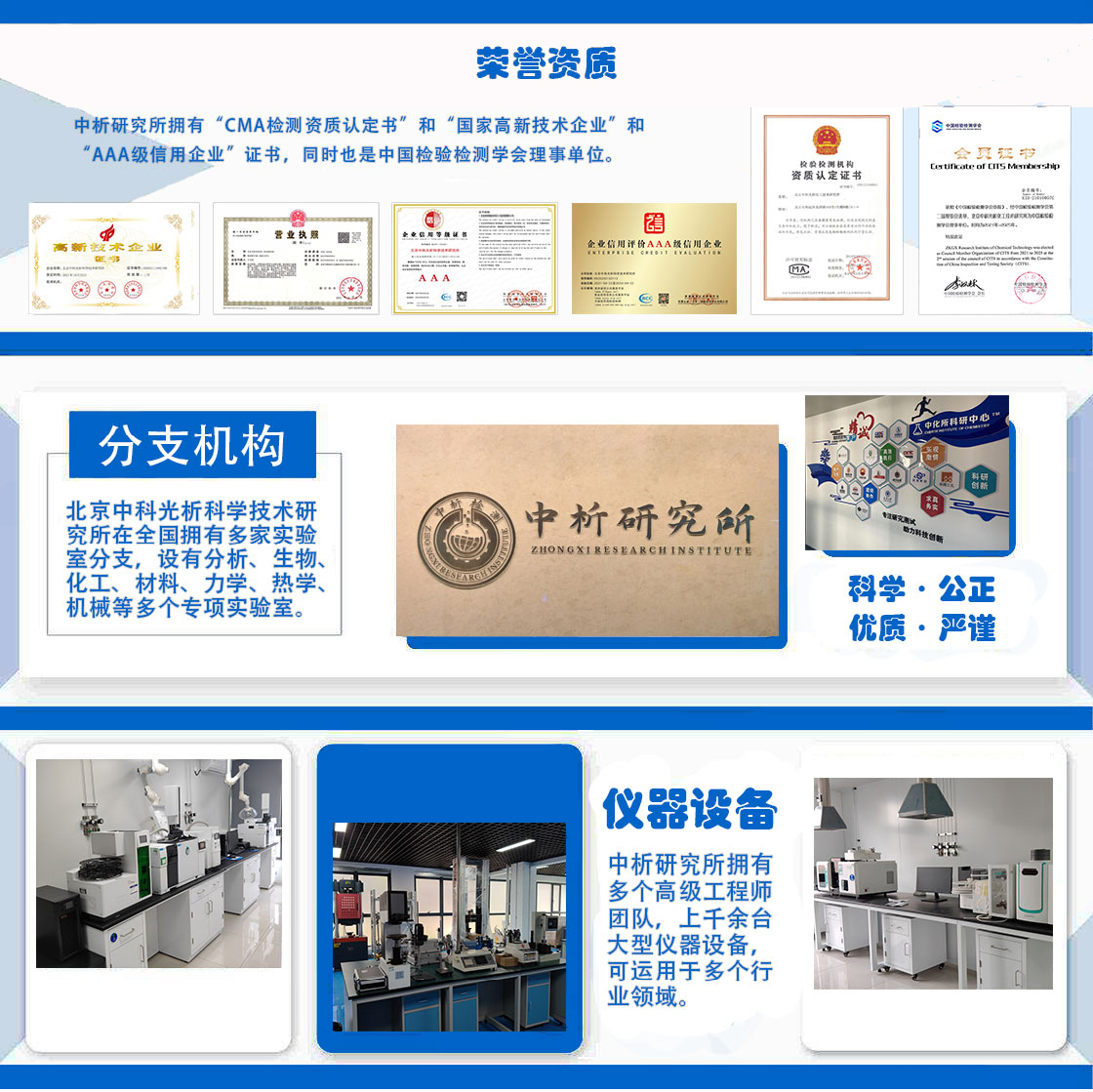
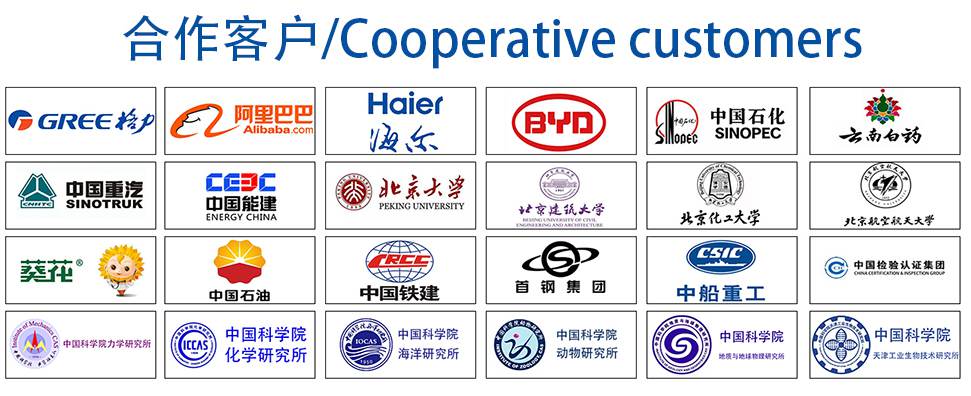