滚动轴承渗碳钢检测的关键项目与技术要点
滚动轴承作为机械设备的核心部件,其材料性能直接决定着轴承的承载能力、耐磨性和使用寿命。渗碳钢凭借其优异的表面硬度与心部韧性的结合特性,成为制造高精度滚动轴承的首选材料。然而,生产过程中材料成分偏差、热处理工艺不当或表面缺陷等问题可能导致轴承早期失效。因此,对渗碳钢进行系统性检测是确保轴承质量的重要环节,检测项目需覆盖材料成分、物理性能及微观结构等多个维度。
一、材料基础性能检测
化学成分分析是检测的首要环节,需验证碳(C)、锰(Mn)、铬(Cr)等主元素含量是否符合GB/T 3203-2016标准。采用光谱分析法可快速测定元素占比,确保材料基础特性达标。同步进行原始晶粒度检测,观察奥氏体晶粒尺寸是否控制在5-8级范围内,避免晶粒粗化影响材料韧性。
二、渗碳层特性测试
渗碳层深度测定是核心项目,需通过显微硬度梯度法或金相法测量有效硬化层(CHD)。按照ISO 2639标准,从表面至550HV1硬度的垂直距离应达到0.8-1.5mm。同时需检测渗碳层碳浓度分布曲线,确保表面碳含量0.8%-1.05%,梯度过渡平缓无突变。
三、微观组织分析
金相显微镜下需观测以下关键指标:渗碳层马氏体形态应为细针状,残余奥氏体含量≤20%(依据ASTM E975标准);心部组织需呈现低碳马氏体与贝氏体的混合结构。特别关注碳化物形态,避免出现网状或粗大颗粒,防止应力集中引发开裂。
四、力学性能验证
表面硬度需达到58-62HRC(洛氏硬度),心部硬度控制在30-45HRC区间。通过旋转弯曲疲劳试验验证材料耐久性,参照GB/T 4337标准,试样需经受10^7次循环载荷无断裂。冲击韧性测试使用夏比V型缺口试样,吸收能量应>40J(ISO 148-1)。
五、缺陷检测控制
采用磁粉探伤或涡流检测排查表面裂纹,灵敏度需满足ASTM E1444要求。超声波检测用于发现内部夹杂物,非金属夹杂物级别应≤2级(GB/T 10561)。对磨削烧伤的检测需结合酸蚀法和显微硬度法,确保无回火马氏体异常组织。
通过上述多维度检测体系的实施,可有效控制渗碳钢轴承的质量稳定性。检测数据需建立完整的可追溯记录,并结合实际工况进行失效模式分析,持续优化生产工艺参数,最终实现轴承产品的高可靠性目标。
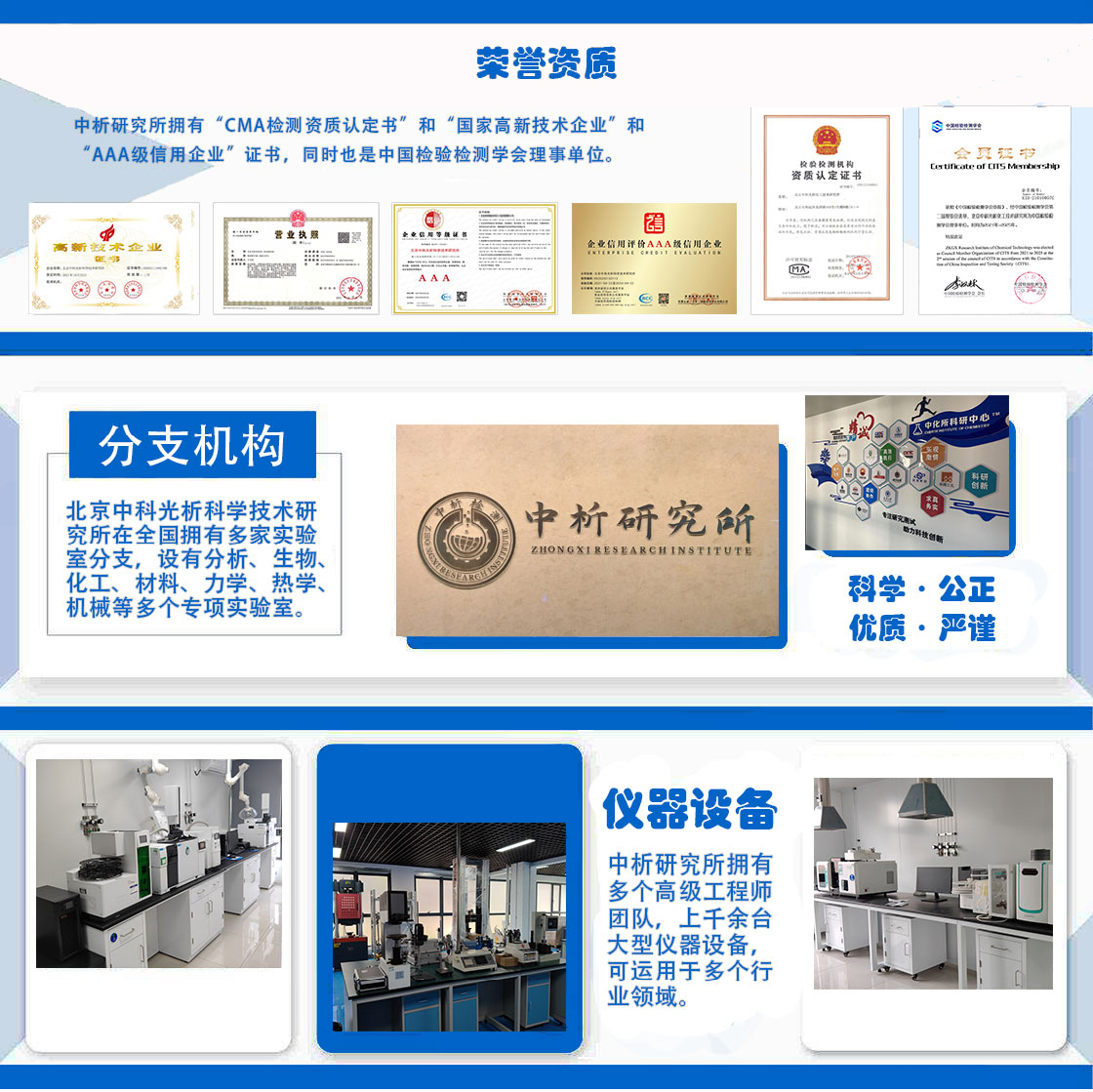
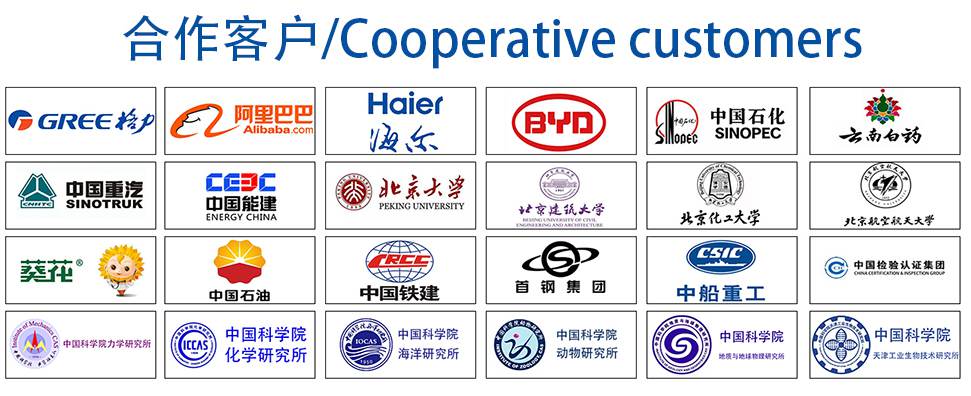