鼓风机轴承检测的重要性
鼓风机作为工业设备中的核心动力部件,其轴承的稳定运行直接关系到整机的效率与寿命。轴承在高速旋转、持续负载及复杂工况下易出现磨损、润滑失效、振动异常等问题,可能导致设备停机、能耗增加甚至安全事故。通过系统化的轴承检测,可提前识别隐患,优化维护计划,减少非计划性停机损失。常规检测需涵盖振动、温度、润滑状态、外观磨损等多维度指标,并结合动态与静态分析,形成全面的健康评估体系。
振动检测与分析
振动是轴承故障最直接的体现。使用专业振动传感器采集轴向、径向和水平方向的振动数据,通过频谱分析识别异常频率成分。重点关注轴承固有频率(如滚动体通过频率、保持架频率)的幅值变化,结合时域波形判断是否存在剥落、裂纹或安装偏移等问题。振动值超过ISO 10816标准阈值时需立即停机排查。
温度监测与热成像
轴承温升异常通常与润滑不良或过载相关。采用红外测温仪或内置温度传感器实时监控运行温度,对比设备历史数据与环境温度变化趋势。当温升超过额定值10℃或局部热点温度差异>15%时,需检查润滑系统并排查摩擦源。热成像技术可可视化温度分布,精准定位异常发热区域。
润滑状态评估
润滑油脂的黏度、污染度及氧化程度直接影响轴承寿命。通过油液分析仪检测油脂颗粒物含量(铁谱分析)、水分比例及添加剂损耗情况。对于脂润滑轴承,注脂周期应根据运行时长和油脂老化测试结果动态调整。建议每季度采样检测,确保油脂清洁度达到NAS 1638标准7级以内。
外观磨损与几何精度检测
停机检修时需拆解轴承进行目视检查,重点关注滚道剥落、保持架变形、密封件老化等缺陷。使用千分尺测量内圈、外圈直径偏差,游隙值应符合GB/T 307.1标准。对疑似疲劳损伤区域进行磁粉探伤或超声波检测,判断裂纹扩展深度。安装前需检查轴与轴承座配合公差,避免过盈量异常导致应力集中。
噪声频谱诊断
通过声级计采集运行噪声并生成频谱图,对比正常工况下的特征频率。轴承早期故障常表现为高频啸叫或周期性冲击声,结合包络分析技术可区分结构性噪声与故障信号。建议在背景噪声<60dB的工况下进行检测,避免环境干扰。
动态平衡校正
转子不平衡会加剧轴承负载,需定期使用动平衡机进行校准。当振动值随转速升高呈平方关系增长时,应进行现场动平衡调试。矫正后残余不平衡量应满足ISO 1940 G6.3平衡等级要求,确保转子质量分布均匀性。
轴向间隙与预紧力检测
采用推拉法或塞尺测量轴承轴向游隙,对比制造商规定的允许范围。对于角接触球轴承等需预紧的结构,使用扭矩扳手控制安装预紧力,避免过紧导致温升异常或过松引发轴向窜动。建议每次大修后重新校准间隙参数。
材质分析与硬度测试
对频繁失效的轴承进行材料成分光谱分析,核查是否与设计规范一致。使用洛氏硬度计检测滚道表面硬度(通常要求HRC58-62),显微硬度梯度变化异常可能预示热处理缺陷。对比断口形貌可区分疲劳失效与过载断裂模式。
通过上述多维度检测体系的实施,可建立轴承全生命周期健康档案,结合状态监测数据实现预测性维护。建议企业制定标准化检测流程,配备专业仪器并加强技术人员培训,将轴承故障率降低50%以上,显著提升鼓风机运行经济性与可靠性。
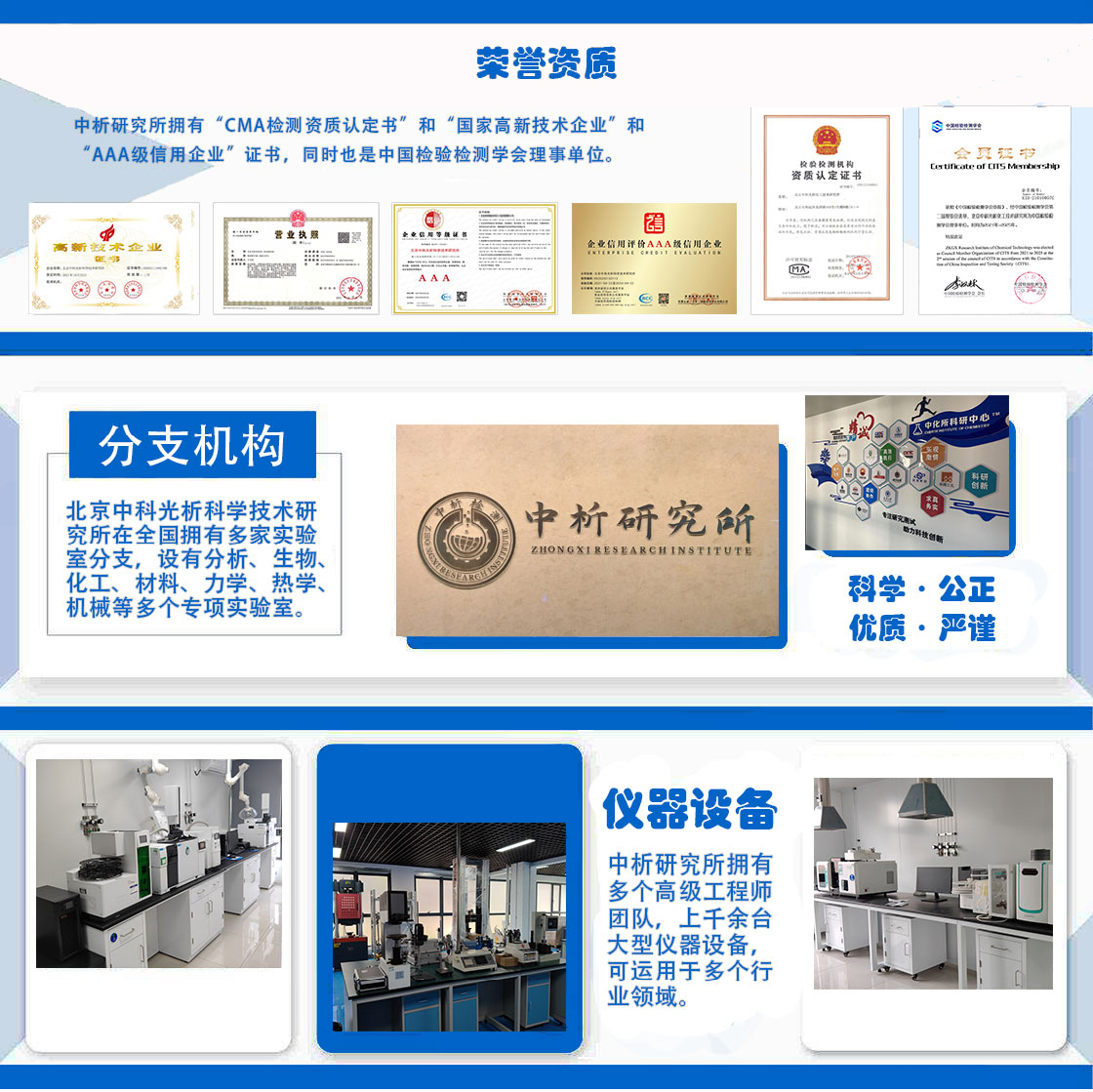
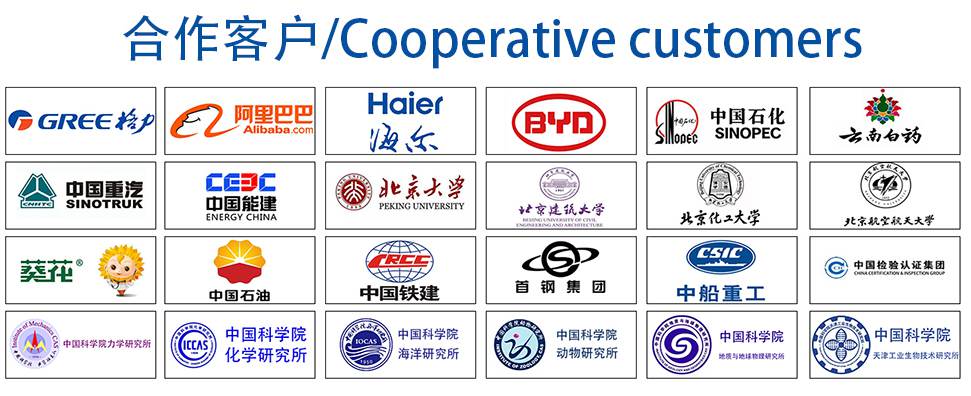