组合机床镗削头检测的重要性
组合机床镗削头作为精密加工的核心部件,其性能直接决定了加工工件的尺寸精度、表面质量和生产效率。随着制造业对高精度、高效率需求的不断提升,镗削头的检测已成为设备维护与质量管理中不可或缺的环节。通过系统性检测,可及时发现主轴跳动、传动系统磨损、润滑失效等问题,避免因设备异常导致批量性质量事故,同时延长关键零部件的使用寿命,保障生产线的稳定运行。
核心检测项目清单
针对组合机床镗削头的检测需覆盖机械、电气、热力学等多维度参数,主要包含以下关键项目:
1. 几何精度检测
使用激光干涉仪或电子水平仪检测主轴轴线与工作台面的垂直度、主轴径向跳动及端面跳动值,精度需达到GB/T 17421.2标准要求。同时检查镗杆的同轴度偏差,确保其≤0.005mm。
2. 主轴系统性能检测
通过转速计测量主轴各级转速的实际偏差值,要求误差≤±2%。使用扭矩测试仪验证最大输出扭矩是否达标,并持续监控主轴温升,在额定转速下运行1小时后温升不得超过35℃。
3. 振动与噪音分析
采用振动传感器采集主轴箱各向振动频谱,重点分析500-3000Hz频段的异常峰值。噪音检测需在标准工况下进行,距离设备1米处的声压级应≤75dB(A)。
4. 润滑系统检测
检查强制润滑系统的油路通畅性,使用流量计验证各润滑点供油量,确保达到设备制造商规定的0.8-1.2L/min标准。同时检测润滑油压力稳定性,波动范围需控制在±0.05MPa内。
5. 传动系统检测
对齿轮传动部件进行齿侧间隙测量,要求新设备间隙≤0.08mm,磨损极限为0.15mm。皮带传动系统需检测张紧力是否在180-220N范围内,并使用频闪仪检查同步带啮合状态。
6. 定位精度验证
通过球杆仪进行圆度测试,评估各轴联动精度。重复定位精度检测要求在300mm行程内,X/Y/Z轴的重复性误差分别≤0.006mm、0.008mm、0.005mm。
综合性能测试
完成专项检测后,需进行模拟加工试验。使用标准试件检测孔径尺寸公差(IT6级)、表面粗糙度(Ra≤1.6μm)及孔系位置精度(±0.015mm),全面验证镗削头的综合加工能力。
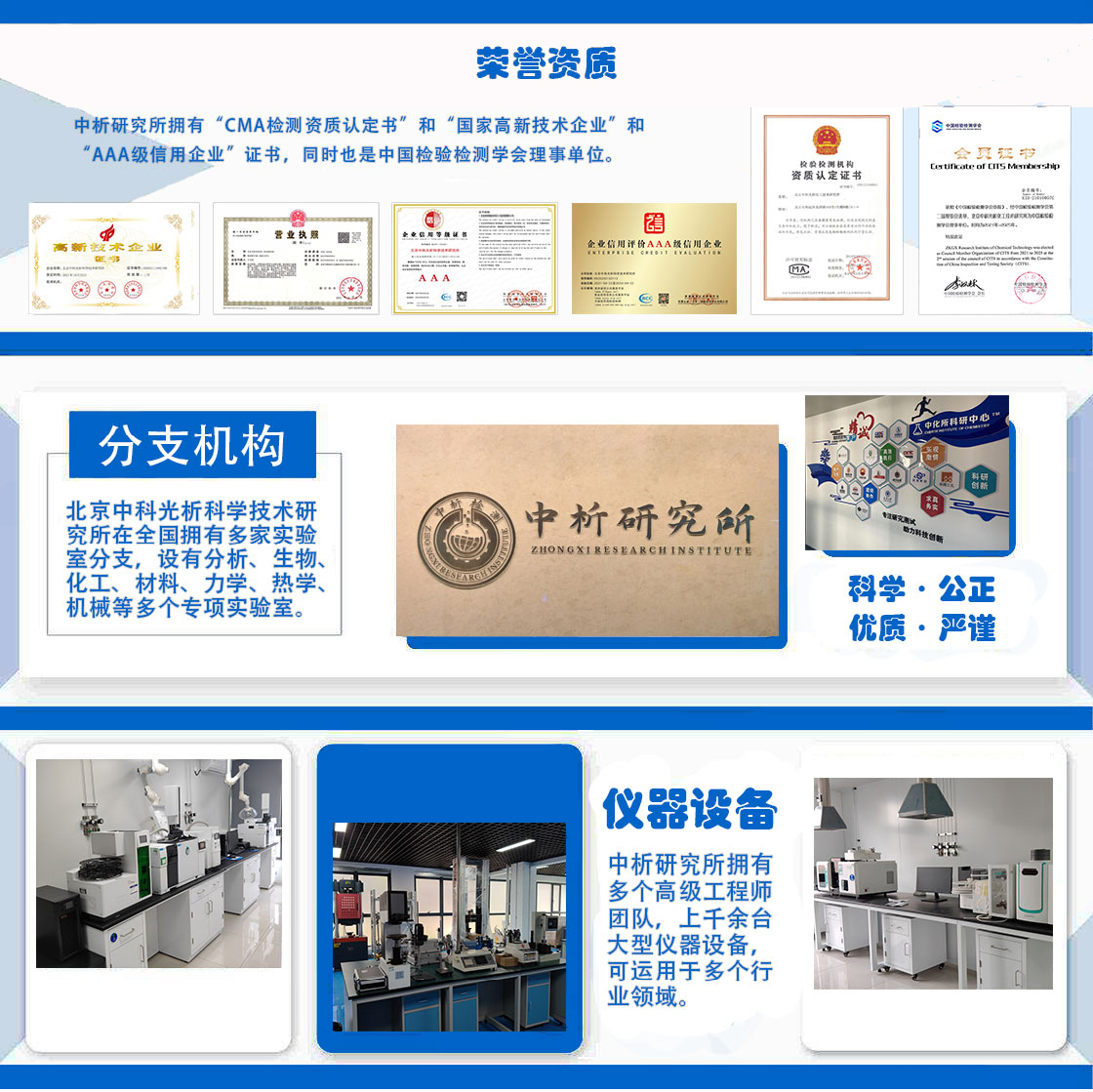
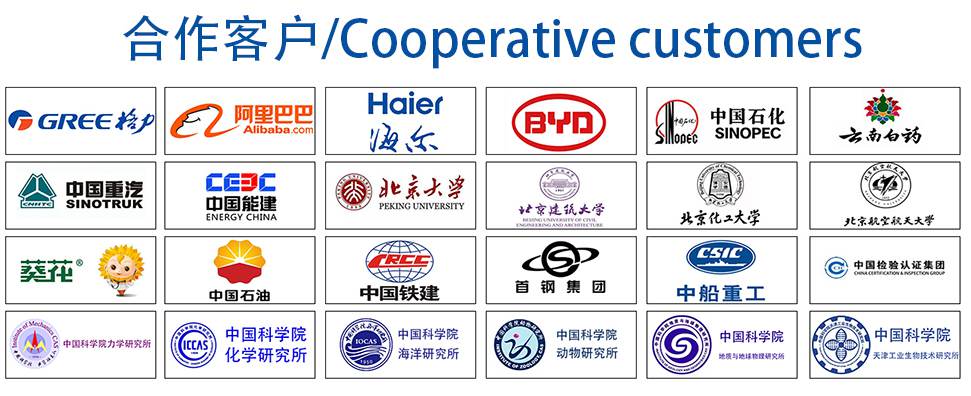