立式精镗床镗头检测的重要性
立式精镗床作为精密机械加工的核心设备,其镗头的性能直接关系到工件的加工精度和设备运行稳定性。镗头作为传递动力、控制切削参数的关键部件,长期处于高速、高负荷工况下,容易因磨损、变形或装配误差导致精度劣化。定期开展系统性检测不仅能预防突发故障,还可通过数据对比延长关键部件寿命,确保加工尺寸公差控制在±0.005mm以内。根据GB/T 5289.3-2018《卧式铣镗床检验条件》延伸标准,镗头检测需涵盖几何精度、动态特性、热稳定性等维度。
核心检测项目及方法
1. 主轴径向跳动检测
使用0.001mm分辨率的千分表检测主轴锥孔径向跳动,将检测棒安装于主轴锥孔内,分别在距主轴端面150mm、300mm处测量。标准规定300mm测量长度内跳动量不得超过0.015mm,重复测量3次取波动值最大值。
2. 轴向窜动检测
通过磁性表座固定千分表于工作台,测头垂直接触主轴端面检测面。主轴以500r/min空转时,轴向窜动应≤0.008mm。此参数直接影响深孔加工时的直线度精度,需特别注意推力轴承的预紧状态。
3. 主轴温升测试
采用红外测温仪连续监测主轴单元运行温度,在额定转速下持续运转2小时后,温升不应超过25℃。异常温升往往预示轴承润滑不良或预紧力过大,需结合振动频谱分析判断故障源。
4. 镗杆定位精度验证
使用激光干涉仪测量镗头轴向运动定位精度,在300mm行程内进行双向重复定位测试。根据ISO 230-2标准,精密级镗床重复定位误差应≤0.006mm,系统误差需通过数控系统补偿消除。
5. 静刚度检测
在镗杆伸出最大行程状态,通过液压加载装置施加1500N径向力,用位移传感器测量变形量。优质镗头系统刚度应保证单位载荷下变形量<1μm/100N,刚度不足会导致切削振纹等加工缺陷。
辅助系统检测要点
润滑系统检测
检查自动润滑装置油路通畅性,测量主轴轴承供油压力(通常0.2-0.4MPa)。对循环油液进行颗粒度分析,NAS 9级以下油品需立即更换,避免精密轴承异常磨损。
刀具夹持力测试
使用液压拉力计检测刀柄拉紧力,BT50刀柄标准夹持力为18-22kN。夹持力衰减会导致加工过程中刀具微位移,影响孔系位置精度。
检测周期建议
常规生产环境下推荐每500小时进行预防性检测,重切削工况需缩短至300小时。检测数据应建立趋势分析档案,当镗头定位精度偏差超过初始值30%时,必须进行维修或部件更换。通过科学的检测维护,可使精镗床镗头精度保持周期延长40%以上,显著降低非计划停机损失。
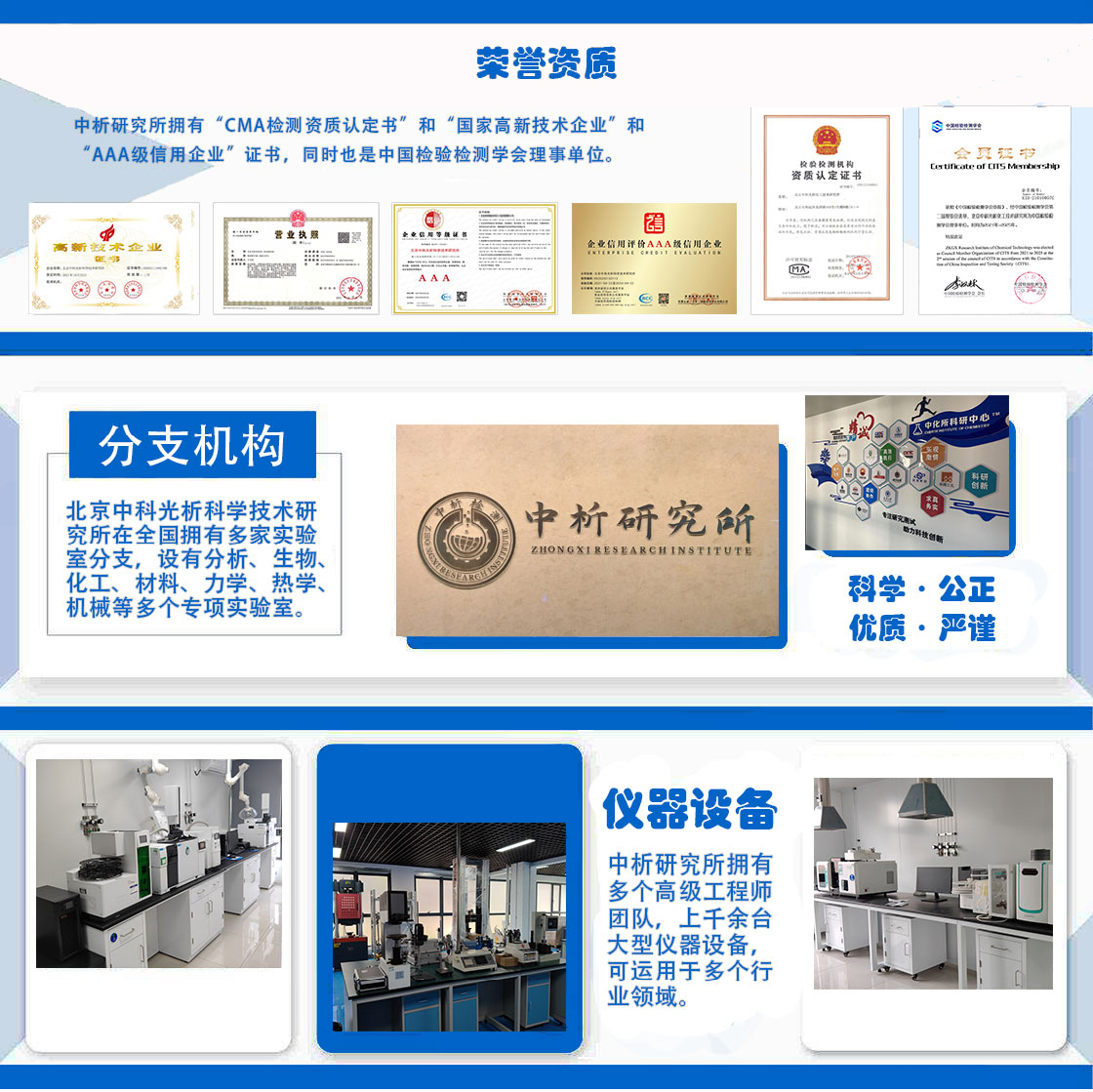
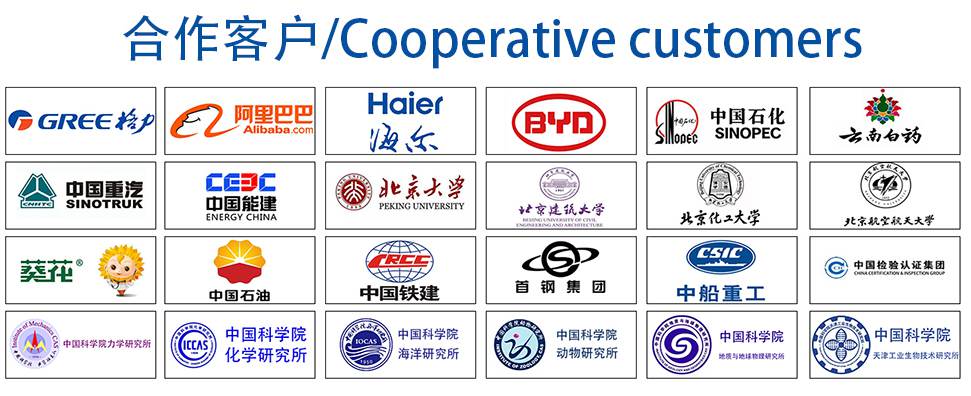