成套性检测:确保系统完整性与协同性的关键环节
在工业制造、设备集成及工程建设项目中,成套性检测作为质量控制的核心环节,直接关系到产品的功能实现和系统稳定性。这项检测旨在验证由多个独立部件、子系统组成的完整设备或生产线是否满足技术协议规定的配套完整性、参数匹配性及功能协调性。特别是在电力设备、自动化生产线、精密仪器等高端制造领域,缺乏严格的成套性检测可能导致设备间兼容性问题,轻则影响生产效率,重则引发重大安全事故。
成套性检测的核心项目
技术参数一致性验证
通过比对设备清单与技术协议,核实各组件型号、规格参数的完全匹配。例如在变电站设备成套检测中,需确保断路器额定电流、变压器容量等关键参数与设计要求完全一致,同时验证配套辅件(如连接件、密封件)的材质标准和尺寸精度。
功能匹配性测试
模拟实际运行场景,验证各子系统间的协同工作能力。以自动化生产线为例,需检测机械臂、传送带、控制系统间的动作时序配合精度,确保生产节拍误差不超过±0.5秒,同时验证紧急停止功能的跨系统联动响应速度。
接口兼容性验证
重点检测机械接口、电气接口、通讯协议的标准化程度。使用三维扫描仪测量机械配合面的尺寸公差(通常要求≤0.02mm),利用协议分析仪测试不同品牌PLC控制器与执行机构间的MODBUS/TCP通信稳定性,确保数据丢包率<0.1%。
安全性能联动检测
在核电设备成套检测中,需严格验证应急冷却系统、辐射监测装置、阀门控制单元的安全联锁功能。通过注入故障信号,测试从异常发生到保护装置动作的全流程响应时间,要求符合IEC61508标准的SIL3安全等级要求。
包装与标识完整性审查
核查运输包装的防震等级是否符合ISTA 3A标准,验证部件标识的永久性标记(包括材质代码、批次号、流向箭头)是否完整可追溯,特别是危险品包装需通过UN38.3认证测试。
检测实施流程与标准
现代成套性检测采用"文件审查→静态检测→动态测试→数据归档"的四阶段模式。运用三维激光跟踪仪、工业内窥镜、频谱分析仪等齐全设备,结合MES系统实现检测数据的实时采集与智能分析。检测标准严格参照GB/T 19001、IEC 61439等国际通用规范,对关键项实施零缺陷管理。
通过系统化的成套性检测,企业可降低30%以上的现场安装调试成本,减少75%的因配件不匹配导致的工期延误。在智能制造与工业4.0时代,这套涵盖机械、电气、信息多维度的检测体系,正成为保障复杂系统可靠运行的核心质量屏障。
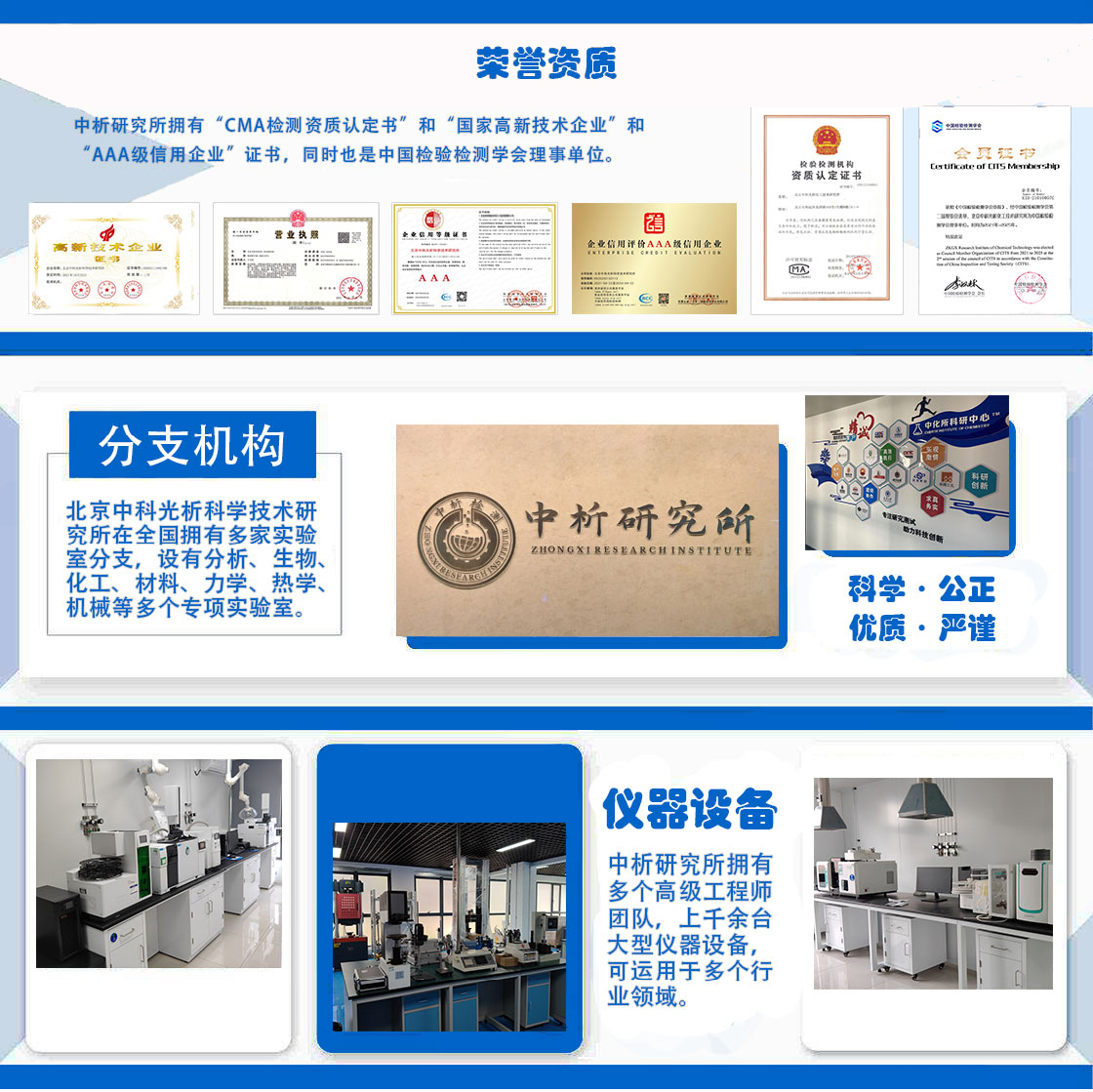
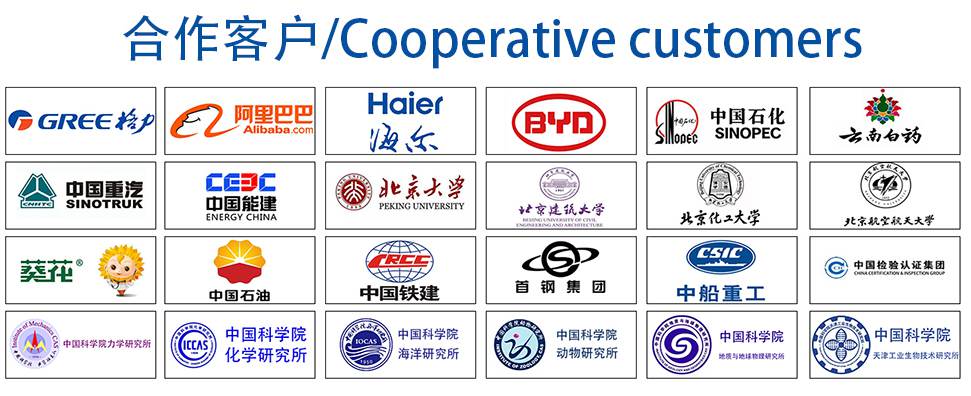