修井转盘检测的重要性与必要性
修井转盘作为石油钻修作业中的核心设备,承担着驱动钻柱旋转、传递扭矩的重要功能。其工作环境恶劣,长期承受高强度载荷、震动及腐蚀介质影响,极易出现机械疲劳、部件磨损等问题。定期开展修井转盘检测是保障设备安全运行、预防井下事故、延长设备使用寿命的关键环节。通过系统化检测可精准识别转盘本体、传动系统、密封装置等核心部件的隐患,确保其在复杂工况下的可靠性和稳定性,同时满足石油行业HSE管理规范要求。
修井转盘主要检测项目及技术要点
1. 结构完整性检测
采用磁粉探伤(MT)或超声波探伤(UT)对转盘本体、法兰连接部位进行裂纹筛查,重点检查应力集中区域。使用三维激光扫描技术评估基体变形量,允许误差不超过JB/T 9043标准规定的0.15mm/m。
2. 轴承系统检测
运用振动频谱分析仪采集主轴承运行数据,对比ISO 10816振动烈度标准。通过温度红外成像监测温升异常,工作温度应控制在75℃以下。检查滚道磨损深度,当超过原始直径0.5%时需立即更换。
3. 齿轮传动系统检测
使用齿轮啮合斑点检测法评估齿面接触精度,接触面积需≥85%。齿侧间隙测量采用压铅法,标准值为0.25-0.40mm。对齿根进行渗透检测,防止疲劳裂纹扩展。
4. 密封系统评估
进行动态压力密封试验,在额定转速下检测泄漏量,要求脂润滑系统泄漏率<3ml/h。检查迷宫密封间隙,径向间隙应保持在0.3-0.5mm范围内。
5. 制动性能测试
使用扭矩传感器测量刹车带制动力矩,需达到设计值的110%以上。制动响应时间检测要求从操作指令发出到完全抱死不超过2秒,重复测试3次取平均值。
6. 驱动系统检测
对链条/万向轴传动系统进行张紧度检测,链条下垂量应<中心距的2%。检测输入轴的同轴度偏差,径向跳动量不得超过0.08mm。
7. 润滑系统检测
采用油液光谱分析技术监测润滑油金属磨粒含量,铁元素浓度预警值为100ppm。检查自动润滑装置工作周期误差,不得超过设定值的±15%。
8. 综合性能试验
在空载、半载、满载三种工况下进行连续72小时运行试验,检测包括:转速波动率(≤±1%)、噪声等级(≤85dB(A))、能耗效率等参数,并绘制扭矩-转速特性曲线。
检测流程与质量控制
规范的检测流程应包含:预检资料审查→目视检查→无损检测→功能测试→数据对比分析→出具检测报告等6个阶段。所有检测数据需录入设备健康管理系统,建立全生命周期档案。检测结果判定严格执行API Spec 7K标准,对关键安全项实行一票否决制。
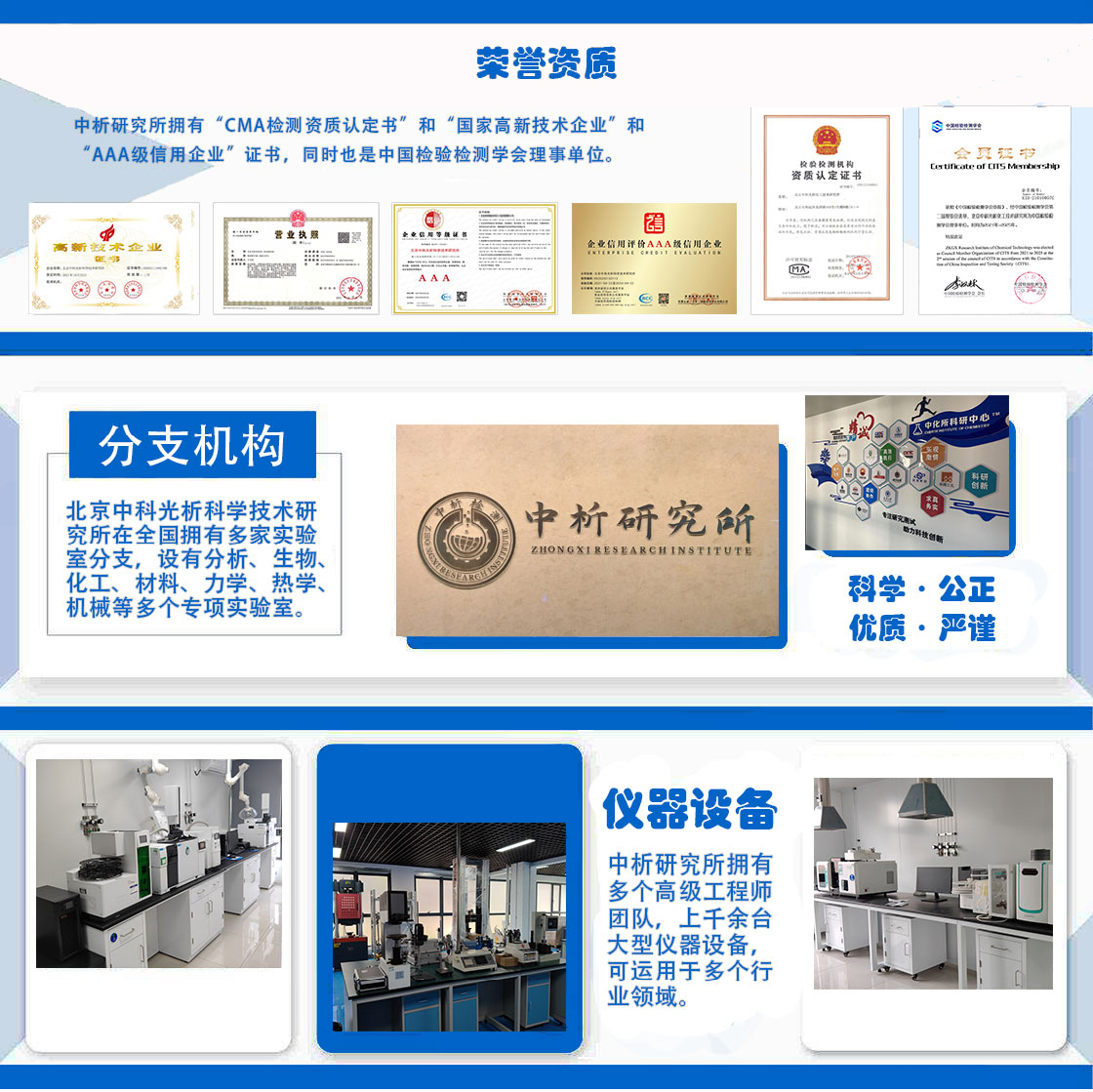
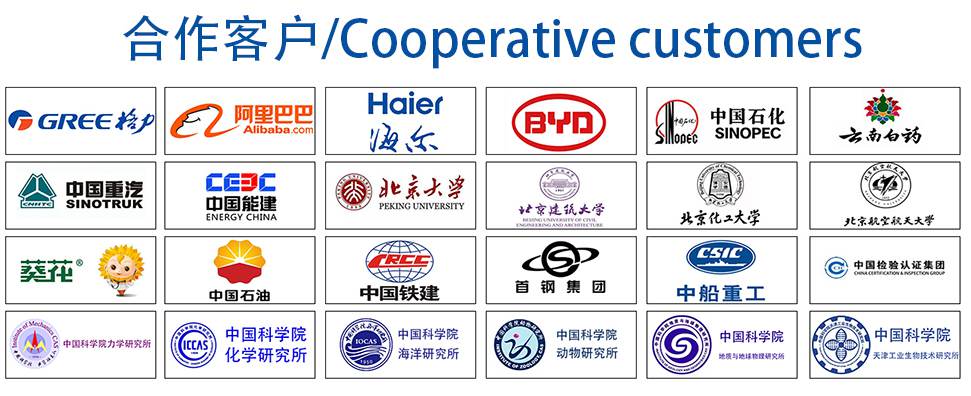