计量罐检测的重要性与必要性
计量罐作为工业生产中常见的储运设备,广泛应用于石油、化工、食品、医药等领域,主要用于液体或气体物料的精确计量与存储。由于其长期处于高压、高温或腐蚀性介质环境中,罐体结构易出现磨损、变形、裂纹等问题,可能导致泄漏、爆炸等严重事故。因此,定期开展计量罐检测是保障生产安全、延长设备寿命、避免经济损失的关键环节。根据《固定式压力容器安全技术监察规程》(TSG 21)及相关国家标准,计量罐需进行系统性检测,涵盖外观、材质、密封性、强度等多个维度,确保其符合安全运行要求。
计量罐检测的核心项目
1. 外观与结构完整性检查
通过目视观察或辅助工具(如内窥镜)检测罐体表面是否存在腐蚀、凹陷、裂纹、焊缝缺陷等问题。重点关注法兰接口、阀门连接处等易损部位,并核对铭牌信息与设计参数是否一致。
2. 壁厚测量与材质分析
使用超声波测厚仪对罐体关键区域(如底部、焊缝周边)进行厚度测量,判断是否存在因腐蚀或机械损伤导致的壁厚减薄。同时通过光谱分析或取样检测,验证材料化学成分是否满足设计要求。
3. 密封性及压力测试
采用气压或水压试验验证罐体密封性,测试压力通常为设计压力的1.25倍。通过保压测试观察压力变化,确认无泄漏现象。对于特殊介质储罐,还需进行气密性专项检测。
4. 安全附件与仪表校验
检查压力表、液位计、温度计、安全阀等附件的有效性,确保其量值准确且在检定周期内。安全阀需进行起跳压力测试,紧急切断装置需模拟动作验证。
5. 基础与支撑系统评估
检测罐体基础沉降情况,检查地脚螺栓、支架的紧固状态及锈蚀程度,评估支撑结构对罐体稳定性的影响,防止因基础变形导致的结构应力集中。
6. 内部腐蚀与缺陷检测
通过磁粉检测(MT)、渗透检测(PT)或射线检测(RT)等无损探伤技术,识别罐体内壁的微观裂纹、气孔等缺陷。针对腐蚀严重区域,可采用导波检测技术进行大范围快速筛查。
检测周期与标准依据
常规检测周期为3-6年/次,高风险环境需缩短至1-2年。检测过程需严格遵循GB 150《压力容器》、NB/T 47013《承压设备无损检测》等标准,并根据介质特性、使用工况制定个性化检测方案。检测报告需包含数据记录、缺陷评级及维修建议,作为设备安全运行的重要依据。
结语
计量罐检测是预防重大事故、保障企业安全生产的核心措施。通过科学规范的检测流程,可及时发现潜在风险并采取修复措施,最大限度降低设备失效概率。建议企业建立完善的检测档案管理制度,结合智能化监测技术(如在线腐蚀监测系统),实现从定期检查到实时预警的全面升级。
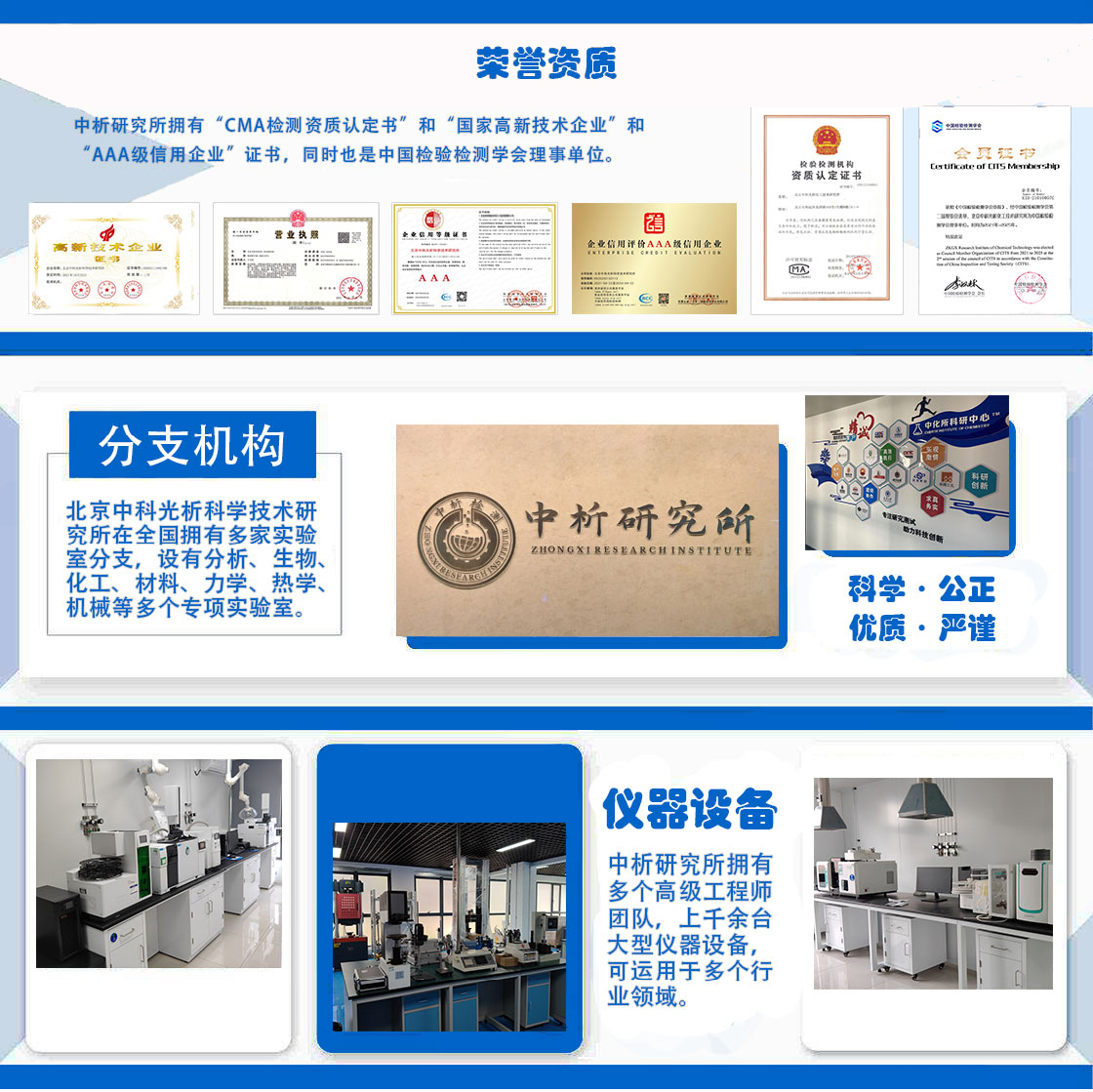
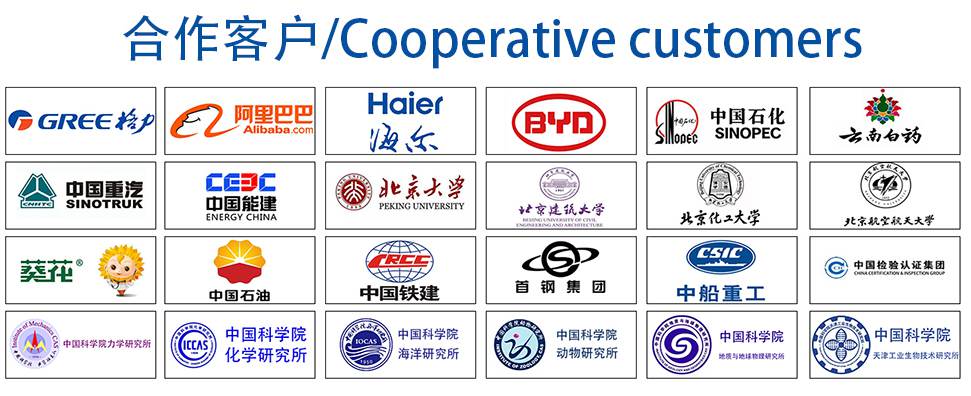