气动调节阀检测的重要性及核心内容
气动调节阀作为工业自动化控制系统的关键执行元件,广泛应用于石油、化工、电力、冶金等领域的流体控制场景。其性能直接影响工艺流程的稳定性、安全性和能效水平。受工作介质腐蚀、压力冲击、长期磨损等因素影响,气动调节阀可能面临密封失效、动作卡滞、响应滞后等问题。因此,定期开展系统性检测是保障设备可靠运行、延长使用寿命和降低故障风险的必要措施。检测项目涵盖阀门本体性能、气动执行机构、附件功能及整体控制精度等多个维度,需结合行业标准和实际工况进行针对性分析。
核心检测项目解析
1. 阀门密封性能检测
通过气密性试验(如气泡法、压降法)检验阀座与阀芯的密封效果,重点关注关闭状态下的泄漏量是否符合GB/T4213标准。对于高压工况,需进行带压密封测试,最大泄漏率应低于规定阈值。
2. 动作特性测试
检测阀门行程时间、开度与信号对应关系,包括:
- 全行程时间测试(4-20mA信号阶跃响应)
- 回差测试(正向/反向输入信号差异)
- 线性度偏差分析(实测开度与理论值对比)
3. 气动执行机构检测
检查气缸密封性、弹簧刚度、膜片/活塞磨损状态,测量供气压力波动对阀位的影响。采用压力传感器监控气室压力曲线,识别气缸漏气或摩擦力异常。
4. 定位器与附件功能验证
智能定位器的校准和通信功能测试(如HART协议),重点验证: - 阀门零点/满量程标定精度 - 故障安全位置动作可靠性 - 反馈信号与阀位实际值匹配度
5. 材料与结构完整性检测
使用超声波测厚仪检测阀体/阀芯腐蚀程度,通过磁粉探伤或渗透检测排查表面裂纹。对于高温高压阀门,需进行金相分析评估材料老化情况。
检测技术发展趋势
随着工业物联网(IIoT)技术的应用,新型检测手段如声发射监测(识别内漏)、振动频谱分析(诊断机械卡涩)、数字孪生模型预测等逐步普及。结合AI算法的智能诊断系统可实现阀门健康状态的实时评估与预警,推动检测从定期维护向预测性维护转型。
通过科学的检测体系,企业可精准掌握气动调节阀的运行状态,避免非计划停机,同时为备件更换周期制定提供数据支持,最终实现生产系统安全性与经济性的双重提升。
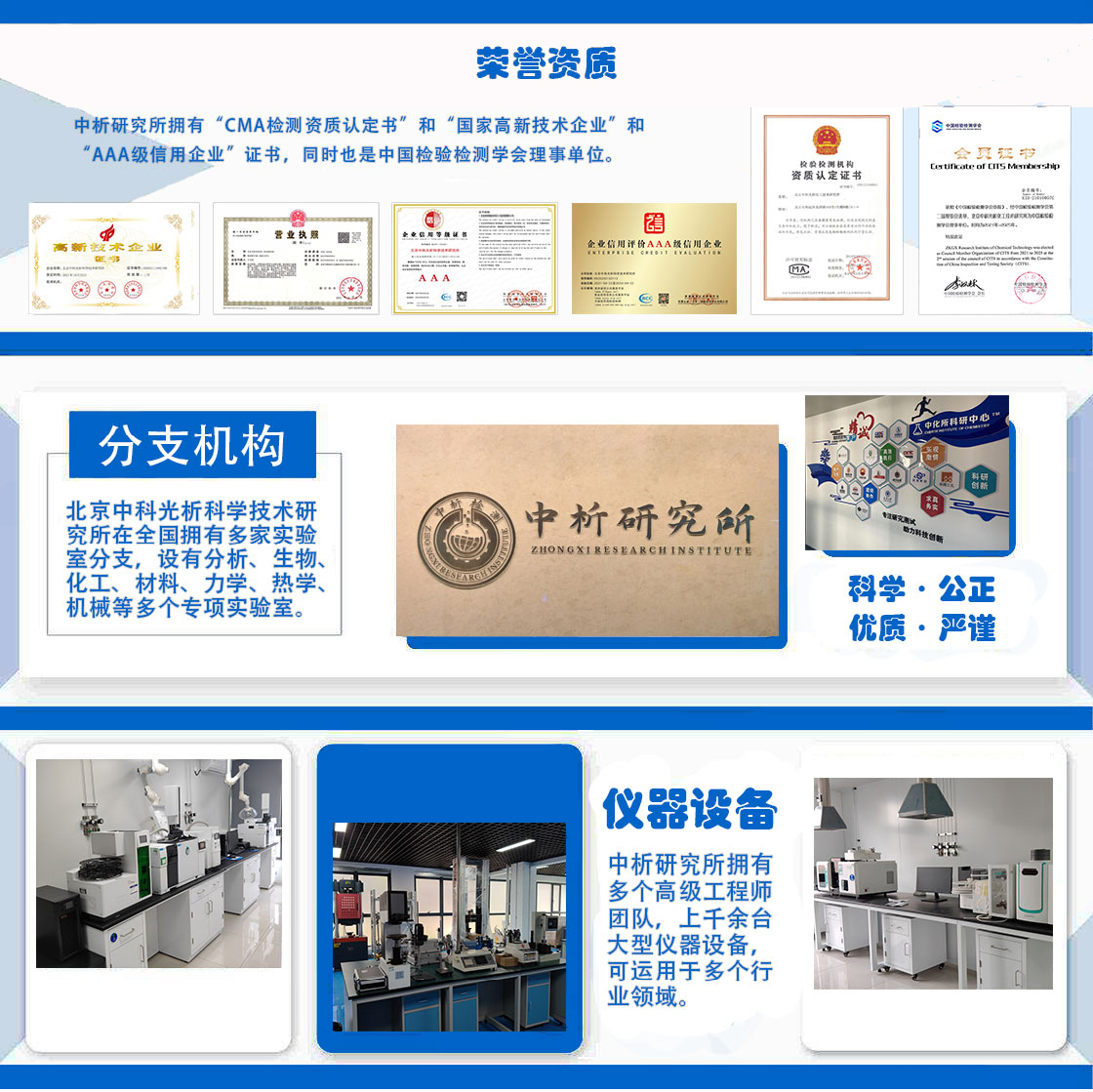
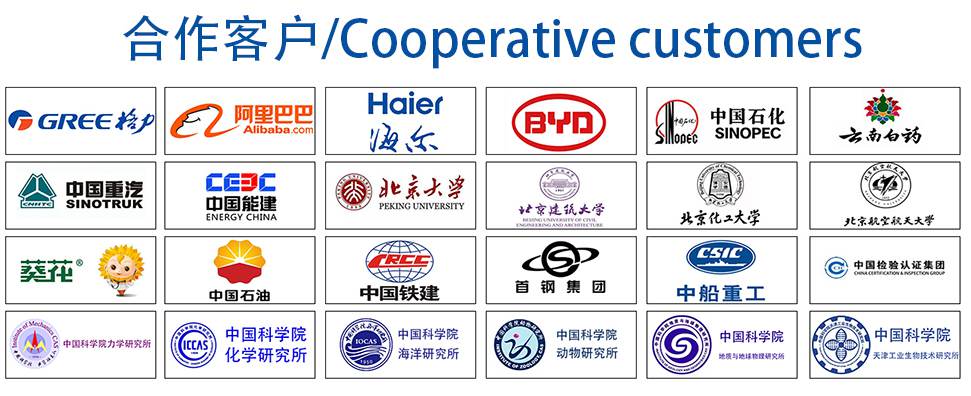