旋转钻井设备水龙带检测的重要性与关键项目
在石油与天然气钻井作业中,旋转钻井设备的水龙带作为连接顶部驱动系统与水龙头的关键部件,承担着输送高压钻井液、传递旋转动力及承受动态载荷的重要任务。由于其长期暴露在高压、腐蚀性介质和复杂工况下,水龙带的性能退化可能引发严重安全事故。因此,定期开展系统性检测是保障钻井作业安全、降低非计划停机的核心措施。
水龙带检测核心项目解析
1. 外观与结构完整性检测
通过目视检查、内窥镜探测等方式,重点排查表面裂纹、磨损、鼓包及接头变形。需特别关注外层橡胶老化龟裂、金属编织层断裂等隐患,使用测厚仪检测各部位厚度均匀性,确保厚度偏差不超过API 7K标准的5%。
2. 压力测试与密封性验证
模拟实际工况进行静态压力测试(1.25倍最大工作压力,保压30分钟)和脉冲压力测试(压力波动幅度±15%,循环次数≥5000次)。同步检测接头密封面的渗漏情况,使用氦质谱检漏仪检测微泄漏量是否超过5×10⁻⁷ mbar·L/s。
3. 材料性能退化分析
截取样品段进行拉伸强度测试(对比原始值下降不超过20%)、橡胶硬度测试(邵氏A型硬度变化±5点以内)及耐化学腐蚀试验。利用红外光谱分析橡胶组分是否发生氧化降解,检测金属编织层的抗拉强度保留率。
特殊工况适应性检测
低温/高温性能测试
模拟-40℃至120℃极端温度环境,验证橡胶弹性模量变化率是否超过15%,观察低温脆化或高温软化现象。通过动态弯曲试验(弯曲角度≥60°,循环频率2Hz)评估柔性保持能力。
动态疲劳寿命评估
建立基于S-N曲线的疲劳寿命预测模型,结合现场工况数据(压力波动频率、弯曲运动幅度)进行加速寿命试验,确保剩余寿命满足至少2个钻井周期的需求。
检测周期与管理建议
常规检测周期应控制在每季度1次,高强度作业环境下需缩短至每月检测。建议建立包含12项关键参数的数字化检测档案,采用RFID标签实现全生命周期追踪。对于出现3处以上表层裂纹或承压能力下降超10%的水龙带,应立即启动更换程序。
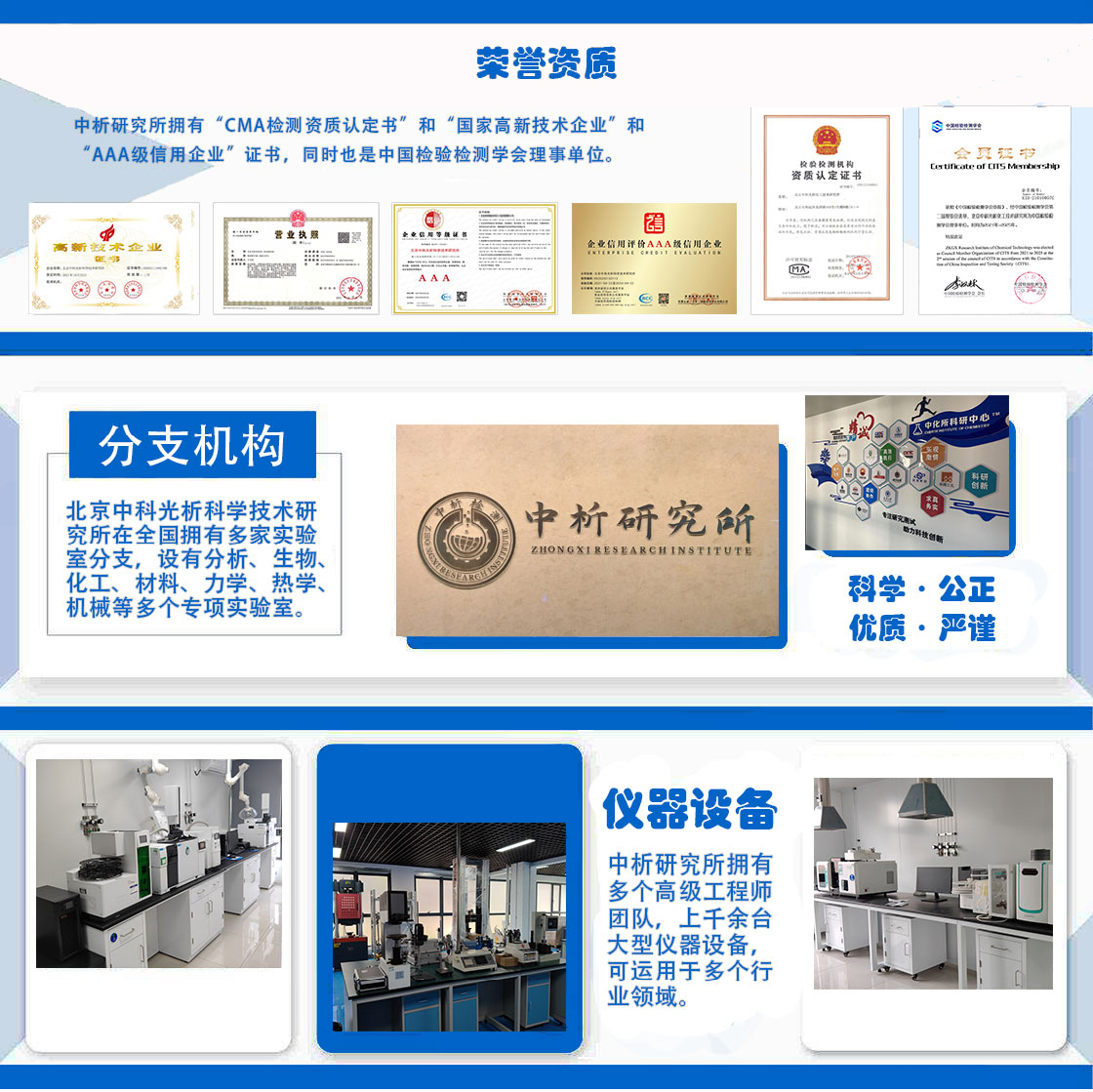
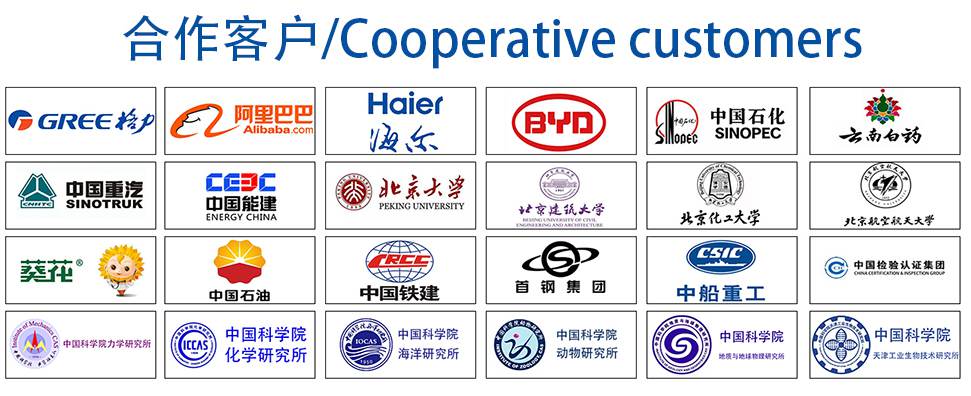