液压系统检测的重要性与核心内容
液压系统作为工业设备、工程机械和航空航天等领域的关键动力传输装置,其稳定性和安全性直接影响设备运行效率与人员安全。由于液压系统长期处于高压、高负荷工况下,元件磨损、油液污染、密封失效等问题可能导致系统性能下降甚至突发故障。因此,定期开展系统性检测是预防故障、延长设备寿命的核心措施。根据行业统计,规范的液压检测可降低60%以上的非计划停机风险,同时减少30%-50%的维护成本。
关键检测项目清单
1. 液压油质量检测
通过专业仪器分析液压油的污染度(NAS等级)、黏度、水分含量和酸值。重点检测油液中金属颗粒含量,判断泵体、阀门等核心部件的磨损情况,同时检查油液氧化程度是否超出ISO 4406标准限值。
2. 系统密封性检测
使用压力衰减法进行静压测试,检测管路、接头和执行器的泄漏情况。采用荧光检漏剂辅助定位微小渗漏点,配合热成像仪识别异常温升区域,确保系统压力保持能力符合GB/T 17489标准要求。
3. 压力元件功能验证
对液压泵、溢流阀、减压阀等压力控制元件进行阶梯压力测试,记录各设定压力点的响应时间和稳态偏差。使用压力传感器矩阵监测系统压力波动,确保动态特性满足设备工况需求。
4. 执行机构性能检测
针对液压缸、液压马达等执行元件,测试其行程精度、输出扭矩和速度稳定性。通过负载模拟装置检测带载工况下的压力-流量特性曲线,评估元件效率衰减程度。
5. 控制阀组响应测试
运用电液伺服测试平台检测比例阀、换向阀的阶跃响应时间和滞环特性。重点验证阀芯位移传感器信号与执行器动作的同步精度,确保控制精度在±1.5%FS范围内。
6. 温度及振动监控
在典型工况下连续记录系统油温变化曲线,结合红外热像仪检测局部过热部位。安装振动传感器分析泵组振动频谱,识别轴承磨损、气蚀等早期故障特征频率。
检测实施注意事项
检测前需制定详细的测试方案,包括工况模拟程序和安全防护措施。建议采用PHM(预测与健康管理)系统进行在线监测,结合离线实验室检测实现全生命周期管理。检测数据应建立趋势分析模型,为预防性维护提供决策支持。
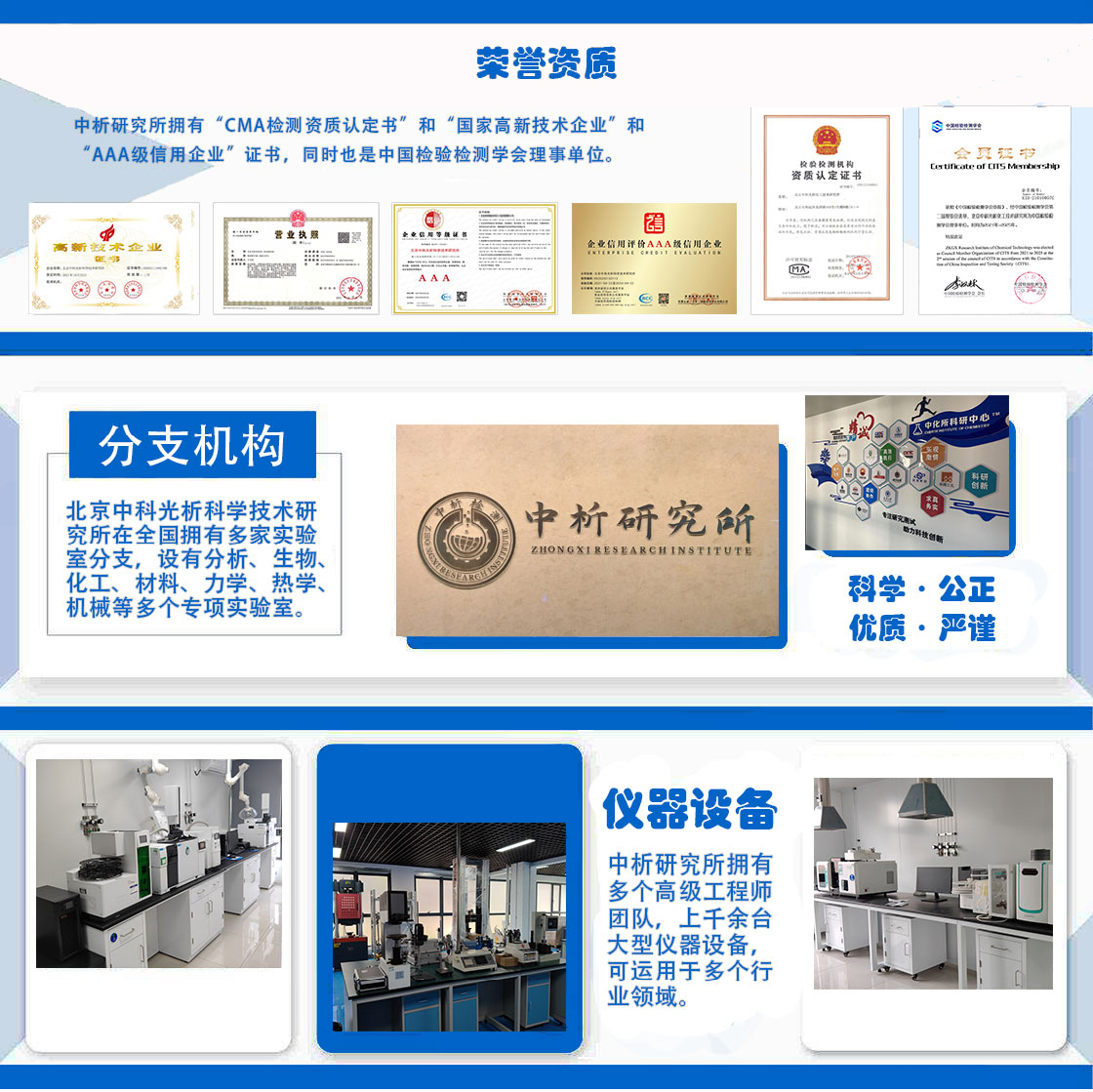
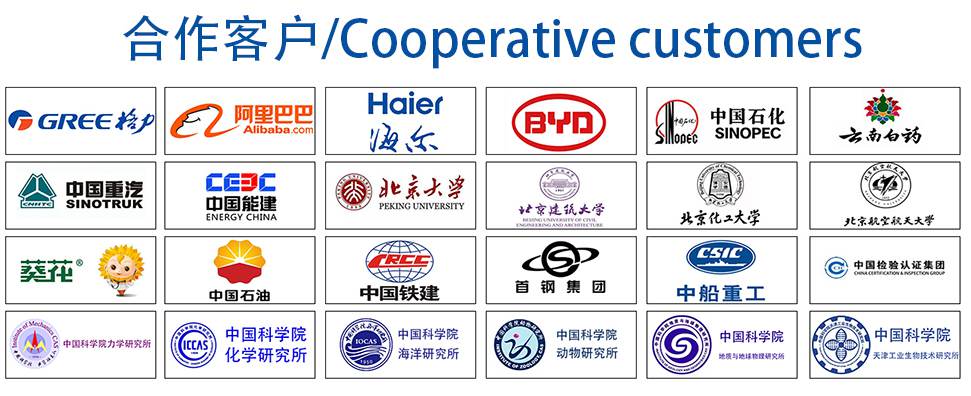