钢质管道环氧粉末外涂层检测的重要性
钢质管道广泛应用于石油、天然气、化工等领域的输送系统,其外表面防腐涂层的质量直接关系到管道的使用寿命和安全性。环氧粉末外涂层因其优异的附着力、耐腐蚀性和机械性能,成为钢质管道防腐蚀的主流选择。然而,在生产、施工及服役过程中,涂层可能因工艺缺陷、机械损伤或环境侵蚀出现质量问题。因此,系统化的检测项目是确保涂层完整性、延长管道寿命的核心手段。通过科学检测,可有效预防泄漏、腐蚀穿孔等事故,降低维护成本并保障工程安全。
检测项目及技术要求
1. 涂层外观检查
采用目视或放大镜检查涂层表面是否有气泡、裂纹、橘皮、流挂等缺陷,确保涂层均匀、平整。根据标准SY/T 0315-2013,不允许存在直径超过2mm的颗粒或明显色差。
2. 涂层厚度测量
使用磁性测厚仪或超声波测厚仪,对管道轴向和环向随机选取测点。要求平均厚度不小于设计值(通常≥400μm),单点最小厚度不低于设计值的80%,且最大值不超过设计值的200%。
3. 附着力测试
通过划格法(ASTM D3359)或拉开法(ISO 4624)评估涂层与基材的粘结强度。划格法要求等级≤2级,拉开法需达到≥5MPa的粘结强度。测试需在不同管段取样,确保结果代表性。
4. 针孔检测
采用高压电火花检测仪(检测电压5kV/mm),扫描涂层表面是否漏电。若发现针孔,需标记位置并进行修补,确保涂层无连续导电缺陷。
5. 耐化学性及耐磨性测试
依据ISO 21809-2标准,通过浸泡试验(如10%NaOH、3%NaCl溶液)评估涂层耐腐蚀性;使用落砂法或Taber磨耗仪测试耐磨性能,要求磨耗量≤40mg(1000转/1kg载荷)。
6. 阴极剥离试验
模拟管道阴极保护环境,施加1.5V电压持续28天后,测量涂层剥离半径。合格标准为剥离半径≤8mm,以验证涂层在电化学环境下的长期稳定性。
检测流程与质量控制
检测需贯穿材料验收、施工过程及竣工验收三个阶段。施工前需验证粉末涂料的固化曲线和粒度分布;涂覆过程中需监控预热温度、喷涂参数;固化后需进行全面的物理化学性能测试。对于长输管道,还需结合现场补口检测和3PE层间粘结力抽查,确保全生命周期质量可控。
结语
环氧粉末外涂层的检测是保障钢质管道服役性能的关键环节。通过建立多维度的检测体系,结合齐全仪器与标准方法,可精准识别涂层缺陷并及时干预。随着智能检测技术(如红外热成像、AI图像识别)的应用,检测效率和准确性将进一步提升,为管道安全运行提供更有力的技术支撑。
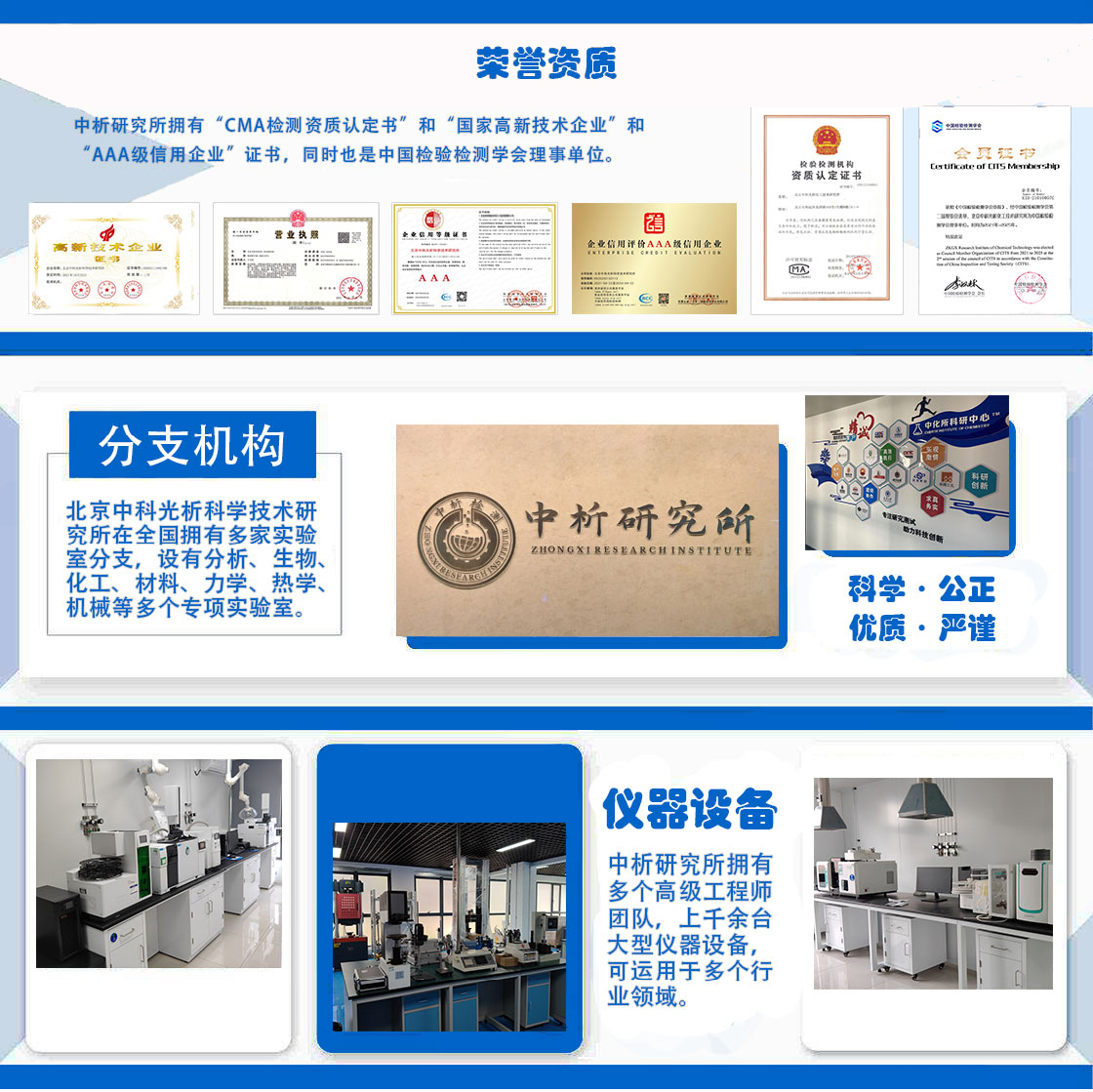
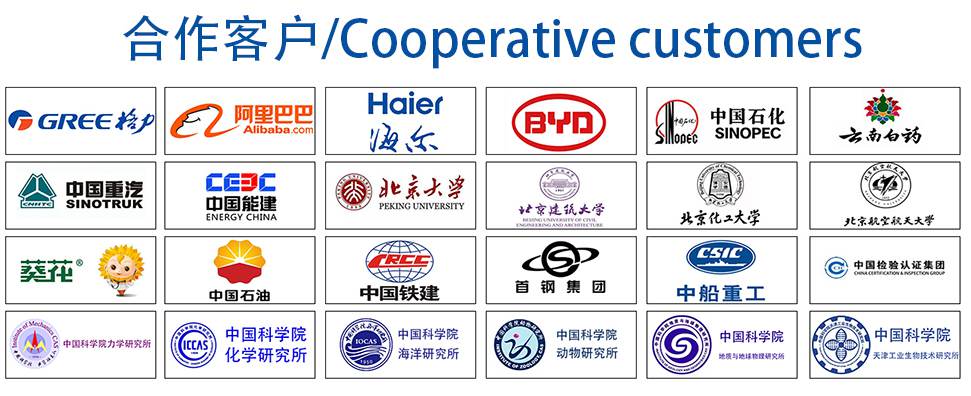