燃气户外管道耐候性涂层检测的重要性
燃气户外管道作为城市能源输送的重要基础设施,长期暴露于复杂自然环境中,经受紫外线、雨水、温差变化、化学腐蚀等外部因素考验。耐候性涂层是保护管道金属基材、防止腐蚀的第一道防线,其性能直接关系到管道的使用寿命和运行安全。若涂层出现老化、剥落或缺陷,可能导致管道锈蚀、泄漏甚至安全事故。因此,定期开展耐候性涂层检测成为保障燃气管道安全的关键环节,需通过科学手段评估涂层状态,及时发现隐患并采取维护措施。
主要检测项目与技术方法
1. 涂层外观检测
通过目视检查或高精度仪器(如数字显微镜)观察涂层表面是否均匀完整,排查龟裂、起泡、剥落、粉化等缺陷。重点关注焊接接头、弯头等应力集中区域,记录异常现象的位置与面积。
2. 附着力测试
采用划格法(ASTM D3359)或拉开法(ISO 4624)评估涂层与金属基材的结合强度。测试时需在涂层表面制作标准划痕或使用专用拉力仪,通过剥离强度值判断涂层附着力是否达标(通常要求≥5MPa)。
3. 涂层厚度测量
使用磁感应测厚仪(磁性基材)或超声波测厚仪(非磁性基材)多点测量涂层厚度,确保符合设计规范(如≥200μm)。数据需覆盖管道不同部位,分析厚度均匀性及是否存在漏涂区域。
4. 耐腐蚀性评估
通过盐雾试验(ASTM B117)模拟海洋或工业污染环境,或湿热试验(GB/T 1740)加速涂层老化,检测涂层抗腐蚀能力。同时可结合电化学阻抗谱(EIS)技术量化涂层防护性能。
5. 耐紫外线老化测试
采用紫外灯老化箱(QUV-ASTM G154)模拟长期光照条件,检测涂层光泽度、颜色变化及抗粉化性能。老化周期结束后,对比色差值(ΔE≤2为合格)并观察表面状态。
6. 环境适应性检测
针对极端气候条件,开展冷热循环试验(-40℃至80℃)、冻融循环试验或酸碱浸泡试验,验证涂层在温度骤变、化学介质侵蚀下的稳定性。
齐全检测技术的应用
随着技术发展,红外热成像、电磁感应涂层缺陷扫描仪(如PCS系统)等无损检测手段逐步普及。例如,红外热成像可通过温差识别涂层剥离区域,而电磁感应技术能快速定位涂层厚度不足或隐藏缺陷,显著提升检测效率与精度。
检测标准与周期建议
需遵循《GB/T 23257 埋地钢质管道聚乙烯防腐层技术标准》《SY/T 0414 钢质管道聚烯烃胶粘带防腐层技术规范》等行业标准。常规检测周期为3-5年,但在高腐蚀区域、地质灾害频发区或涂层服役超过10年时,应缩短至1-2年。
结语
燃气户外管道耐候性涂层的系统性检测是预防泄漏事故的核心措施。通过多维度技术组合与周期性评估,可动态掌握涂层退化规律,为维修决策提供科学依据。同时,需结合管道实际运行环境制定个性化检测方案,最大限度延长管道寿命,保障能源输送安全。
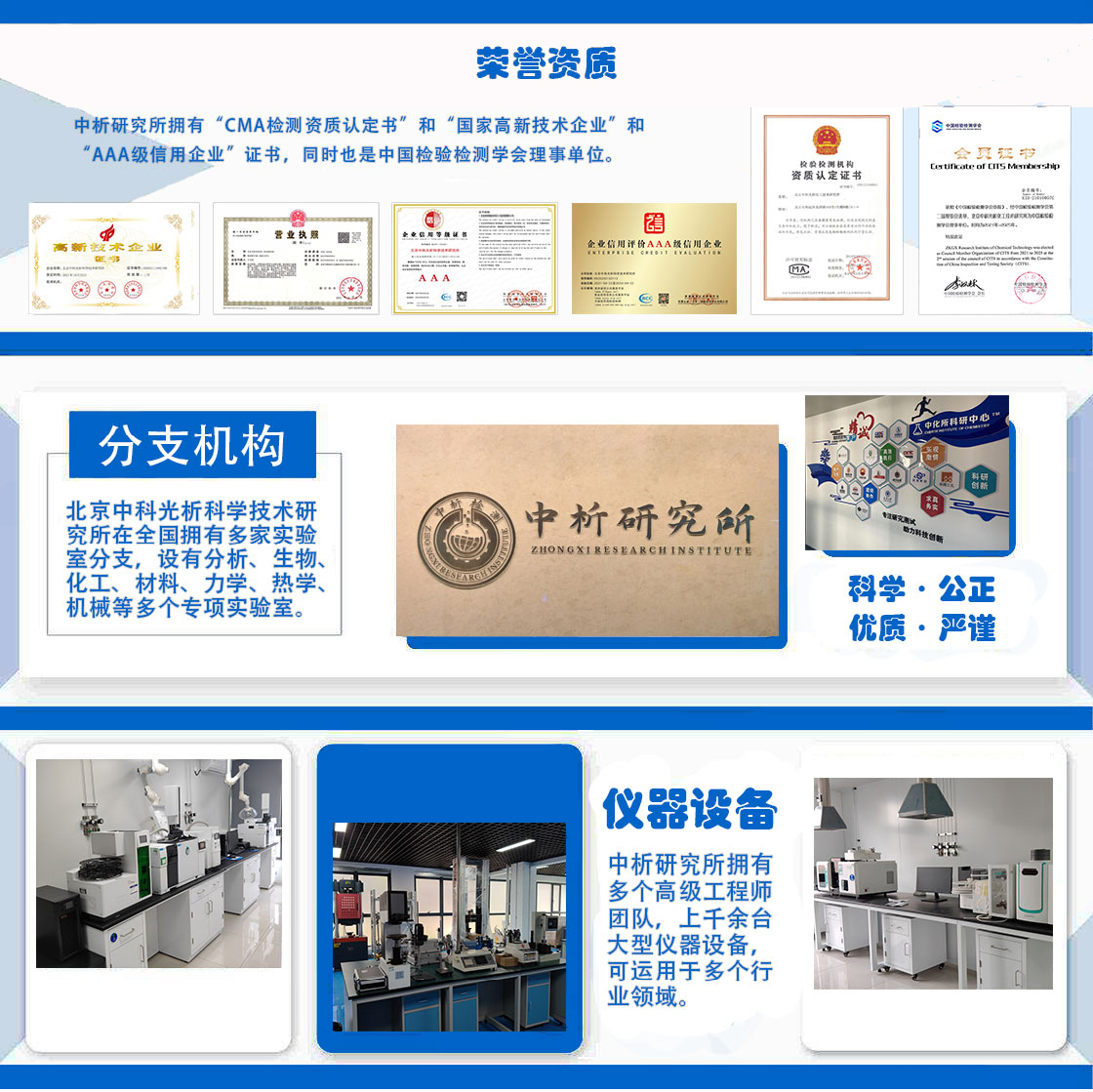
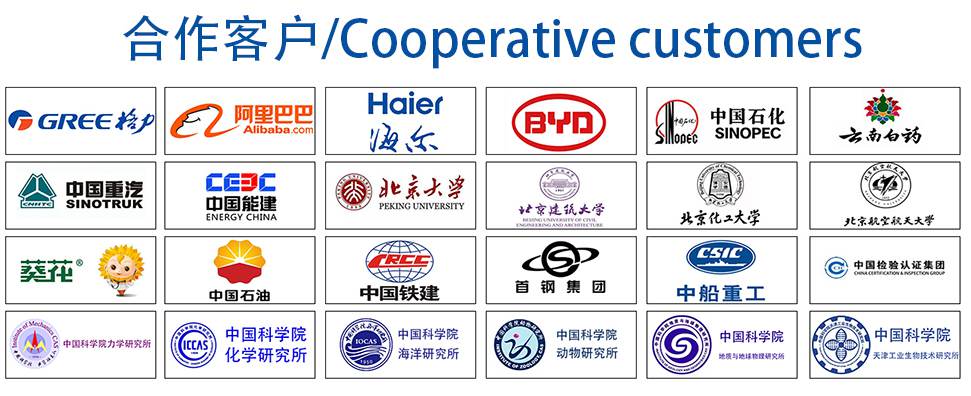