机器人系统电缆检测的关键项目与技术要求
随着工业自动化与智能制造的快速发展,机器人系统电缆作为动力传输、信号控制的核心载体,其性能稳定性直接影响设备运行安全与生产效率。在复杂振动、高温、油污等恶劣工况下,电缆需要承受机械应力、电磁干扰等多重考验。通过系统化检测可有效预防线路老化、绝缘失效等隐患,降低设备故障率。本文针对机器人系统电缆的核心检测项目展开详细说明。
一、外观与物理性能检测
采用目视检测与测量工具对电缆外护套进行全方位检查,重点关注表面是否存在划痕、压痕、气泡等缺陷。使用千分尺测量绝缘层厚度均匀性,确保公差范围符合GB/T 5023标准要求。同时验证电缆弯曲半径是否满足机器人关节活动需求,通过反复弯折试验验证材料的抗疲劳特性。
二、电气性能测试
使用绝缘电阻测试仪在500V DC电压下测量导体间及导体对屏蔽层的绝缘电阻值,要求达到100MΩ/km以上。耐压测试采用工频交流3kV电压持续5分钟,观察是否出现击穿现象。通过回路阻抗测试验证导体导电性能,确保电能传输效率符合设计指标。
三、电磁兼容性评估
利用频谱分析仪检测电缆屏蔽层的衰减效能,要求高频段(1GHz以上)屏蔽效率不低于90%。通过串扰测试验证多芯电缆的信号隔离度,采用脉冲群抗扰度试验模拟工业环境中的电磁干扰场景,确保控制系统信号传输稳定性。
四、环境适应性验证
将电缆样本置于温度循环箱中执行-40℃至+125℃的冷热冲击试验,每个温区保持2小时后观察材料形变情况。盐雾试验按照IEC 60068-2-11标准进行96小时喷洒,检测金属部件腐蚀程度。油污浸泡测试使用ISO 1817标准规定的IRM903油液,评估护套材料耐化学腐蚀性能。
五、动态性能监测
在电缆运动测试平台上模拟机器人实际工作状态,记录200万次弯曲循环后的导体断裂情况。使用三坐标测量仪检测扭转角度偏差,验证多轴联动时的抗扭性能。通过加速度传感器采集振动频响数据,分析谐波共振对信号质量的影响。
专业检测机构建议采用ASTM B193/IEC 60228等国际标准体系,结合具体工况制定检测方案。企业应建立周期性检测计划,重点关注连接器插拔部位、弯曲半径最小处等故障高发区域,通过预防性维护保障机器人系统的长效稳定运行。
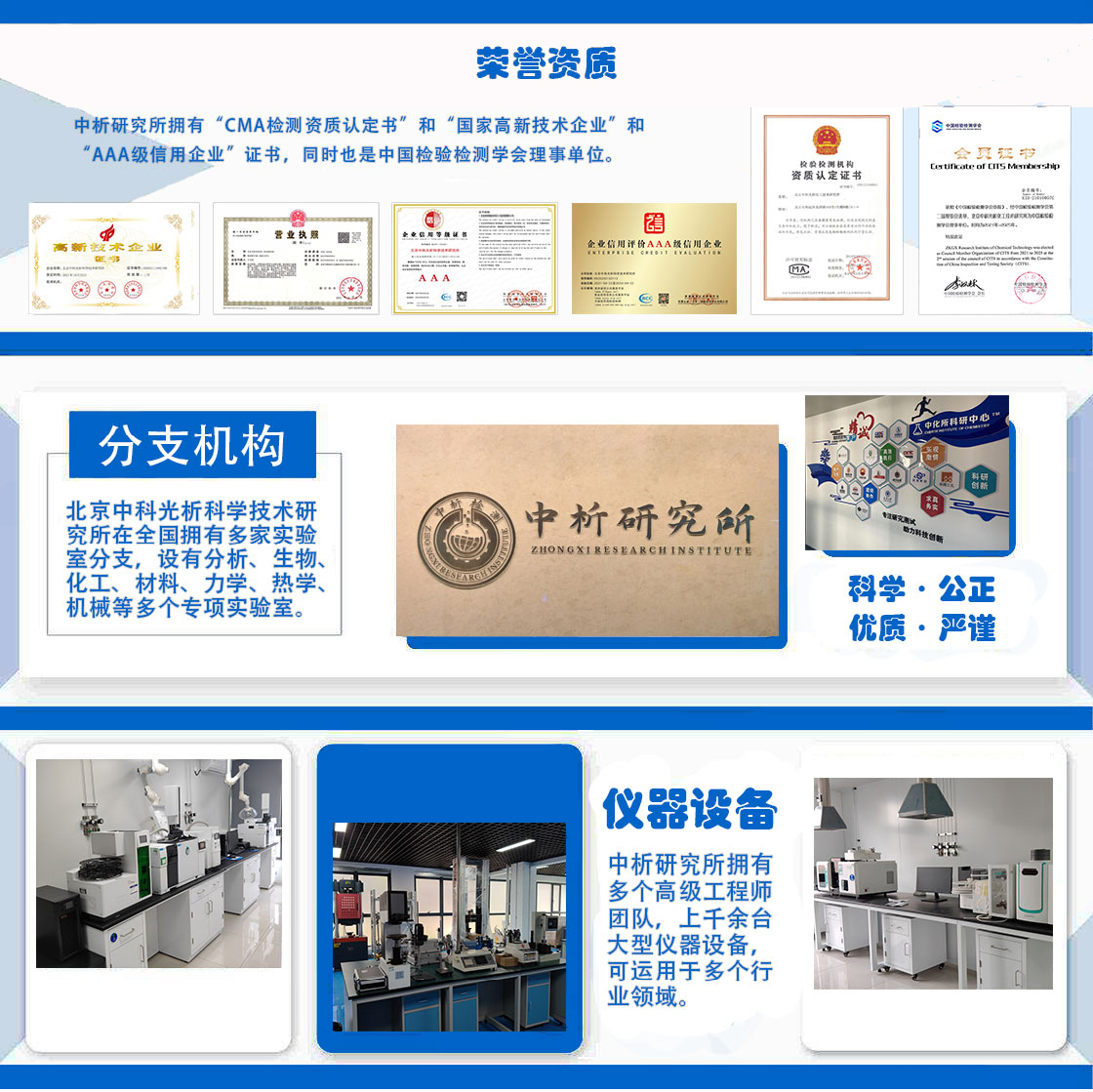
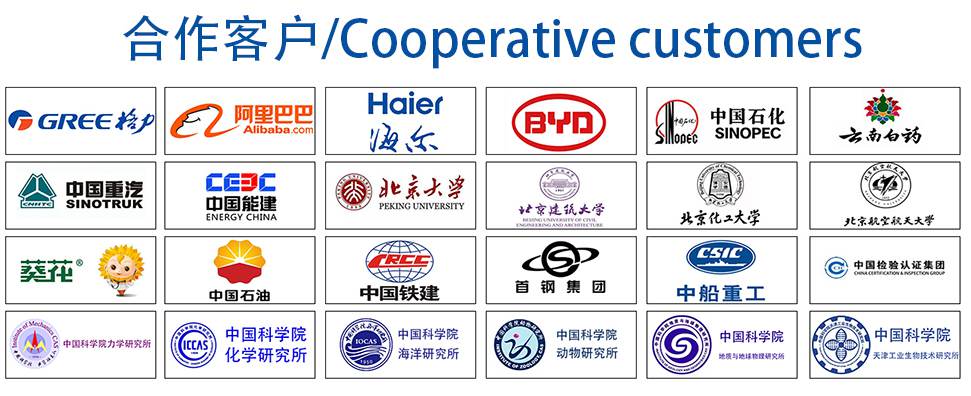