称量式液体添加系统检测的关键技术与应用
称量式液体添加系统作为工业自动化生产中的核心设备,广泛应用于化工、食品、制药等领域。该系统通过高精度称重传感器实时监测液体质量变化,结合闭环控制算法实现精准添加,其性能直接影响到生产效率和产品质量。因此,定期开展系统检测与校准是确保其稳定运行的必要手段。检测过程需覆盖机械结构、传感器精度、控制逻辑等核心模块,同时关注环境因素对测量结果的影响。通过科学的检测流程和数据分析,可有效规避因设备老化、参数偏移或操作失误导致的误差风险。
核心检测项目及技术要求
1. 称重传感器精度校准
使用标准砝码进行多点标定,检测量程内线性度、重复性及蠕变误差,误差应≤±0.05%FS。需模拟实际工况下的振动与温度变化,验证动态测量稳定性。
2. 密封性测试
对输送管路、阀门和执行机构进行0.6MPa压力测试,保压30分钟压降不超过5%。采用氦质谱检漏法定位微渗漏点,确保无液体挥发或污染风险。
3. 流量稳定性分析
通过质量流量计与系统输出值对比,评估不同粘度液体的流速波动。要求连续运行6小时流量偏差≤±1%,峰谷值波动控制在设定值的2%范围内。
4. 控制逻辑验证
模拟断料、过载、通讯中断等异常工况,测试急停响应时间(≤100ms)和数据恢复能力。检查PID参数自整定功能的有效性,确保加减量过程无超调振荡现象。
检测流程优化策略
建议采用分级检测模式:日常点检侧重基础功能验证,月度检测进行关键参数校准,年度大检需拆解维护核心部件。引入数字孪生技术建立虚拟仿真模型,通过对比实际运行数据与理论模型预测值,提前识别潜在故障风险点。
常见问题与解决方案
对于称量漂移问题,需检查传感器接地电阻(≤4Ω)并屏蔽电磁干扰源。当出现批次间添加量差异时,应排查气动阀响应延迟或液体温度补偿失效因素。建议建立检测数据库,通过趋势分析预判部件寿命周期。
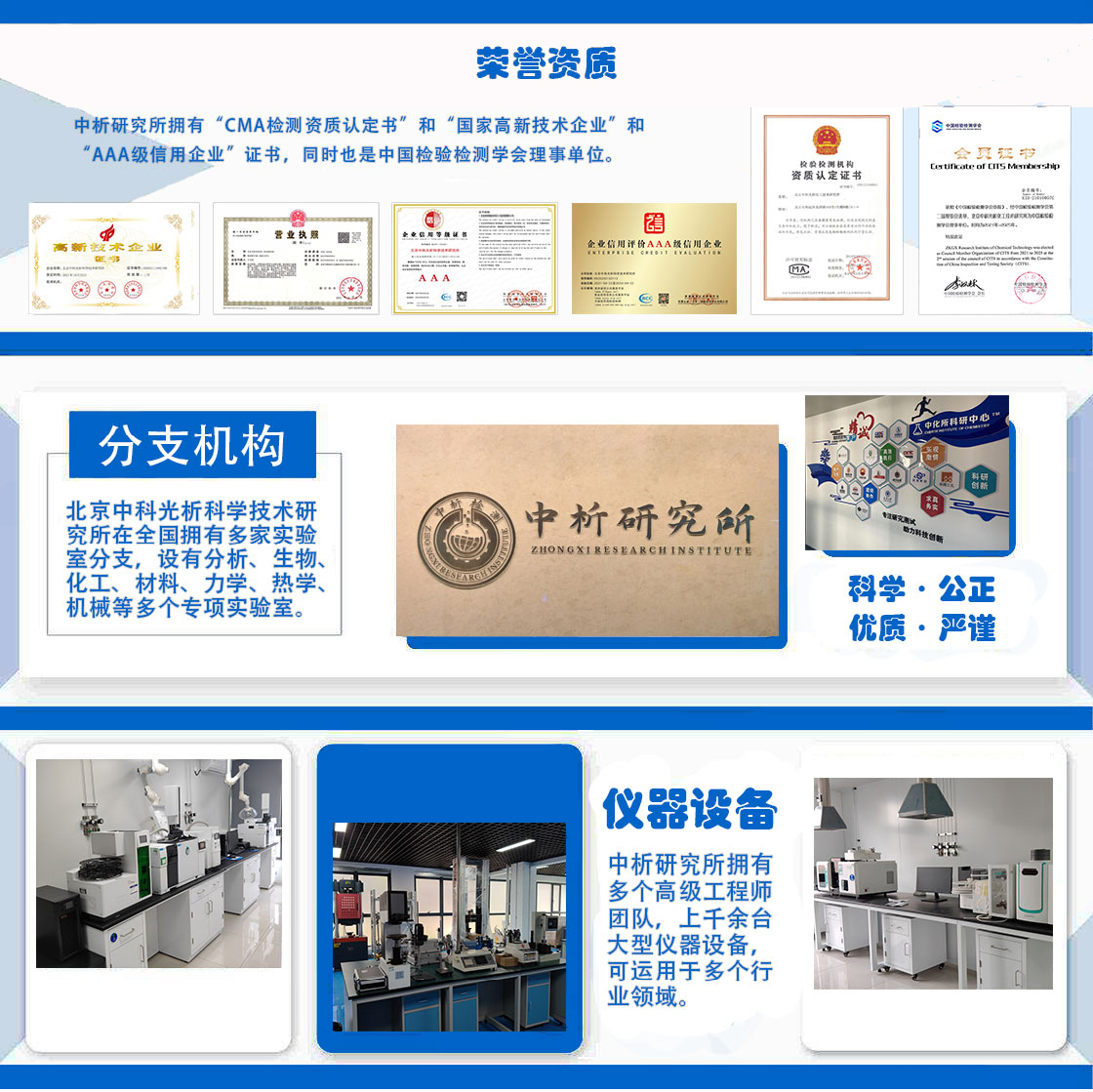
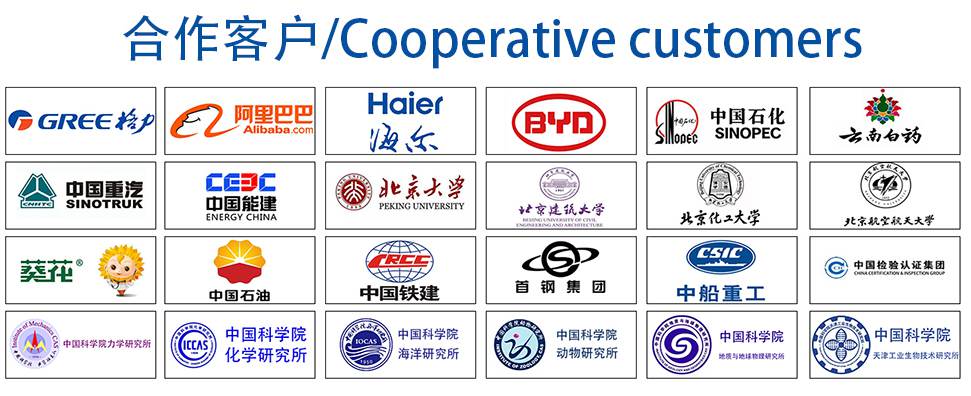