尺寸公差检测的核心价值与应用领域
在精密制造领域,尺寸公差检测是确保零部件互换性和装配精度的关键环节。作为现代质量控制体系的核心组成部分,它通过测量实际加工尺寸与设计要求的偏差范围,保障机械零件在运动配合、承载能力、密封性能等方面的功能实现。这项技术广泛应用于汽车制造、航空航天、模具加工、医疗器械等对精度要求严苛的行业,特别是在新能源汽车动力总成、半导体设备精密部件等前沿领域,公差检测精度已突破微米级要求。
基础线性尺寸检测
作为最基础的检测项目,线性尺寸检测涵盖长度、宽度、高度等单一方向尺寸测量。工程师使用电子数显卡尺(分辨率0.01mm)、外径千分尺(精度1μm)或激光位移传感器进行检测。在自动化生产线中,常配备机器视觉系统配合高精度标定板,实现每分钟200件以上的在线检测速度,公差带控制范围可达±0.005mm。
几何公差复合检测
该检测项目包含形状公差(直线度、平面度、圆度)和位置公差(平行度、垂直度、同轴度)的复合测量。三坐标测量机(CMM)通过接触式探针或光学扫描头获取三维点云数据,配合专业测量软件进行GD&T分析。例如发动机缸体的主轴承孔同轴度检测,要求多个轴孔的轴线偏差不超过φ0.015mm,通常采用温度补偿型CMM在恒温车间完成测量。
表面形貌综合检测
现代检测体系将表面粗糙度、波纹度等形貌特征纳入公差控制范畴。白光干涉仪可实现0.1nm级纵向分辨率,精确测量微观表面轮廓。在光学元件加工中,表面粗糙度Ra值需控制在0.02μm以内,同时要满足功率谱密度(PSD)曲线要求。新型智能检测设备已实现表面纹理特征与加工参数的智能关联分析。
动态配合间隙检测
针对运动副零件的装配检测,需要模拟实际工况进行动态测量。机器人辅助测量系统可加载不同扭矩,检测齿轮副啮合间隙的变化情况。在自动变速箱阀体检测中,利用气动量仪配合专用测头,可在0.5秒内完成多孔系位置度及配合间隙的同步检测,检测重复性达到±1.5μm。
多维度数据融合分析
现代尺寸检测不再局限于单一参数判定,而是通过SPC系统整合历史检测数据,建立过程能力指数CPK分析模型。智能测量设备配备边缘计算模块,可实时进行测量数据趋势预测,当检测到连续7个点呈单调变化趋势时自动触发工艺调整预警,实现真正的预防性质量控制。
新型检测技术突破
随着X射线计算机断层扫描(工业CT)技术的普及,可实现复杂内腔结构的无损检测。在增材制造领域,微焦点CT系统可检测0.05mm级的内部缺陷。量子测量技术的突破使得纳米级位移传感器逐步实用化,为下一代超精密制造提供检测支撑。值得关注的是,基于数字孪生的虚拟检测技术开始与物理测量系统深度融合,推动检测效率提升40%以上。
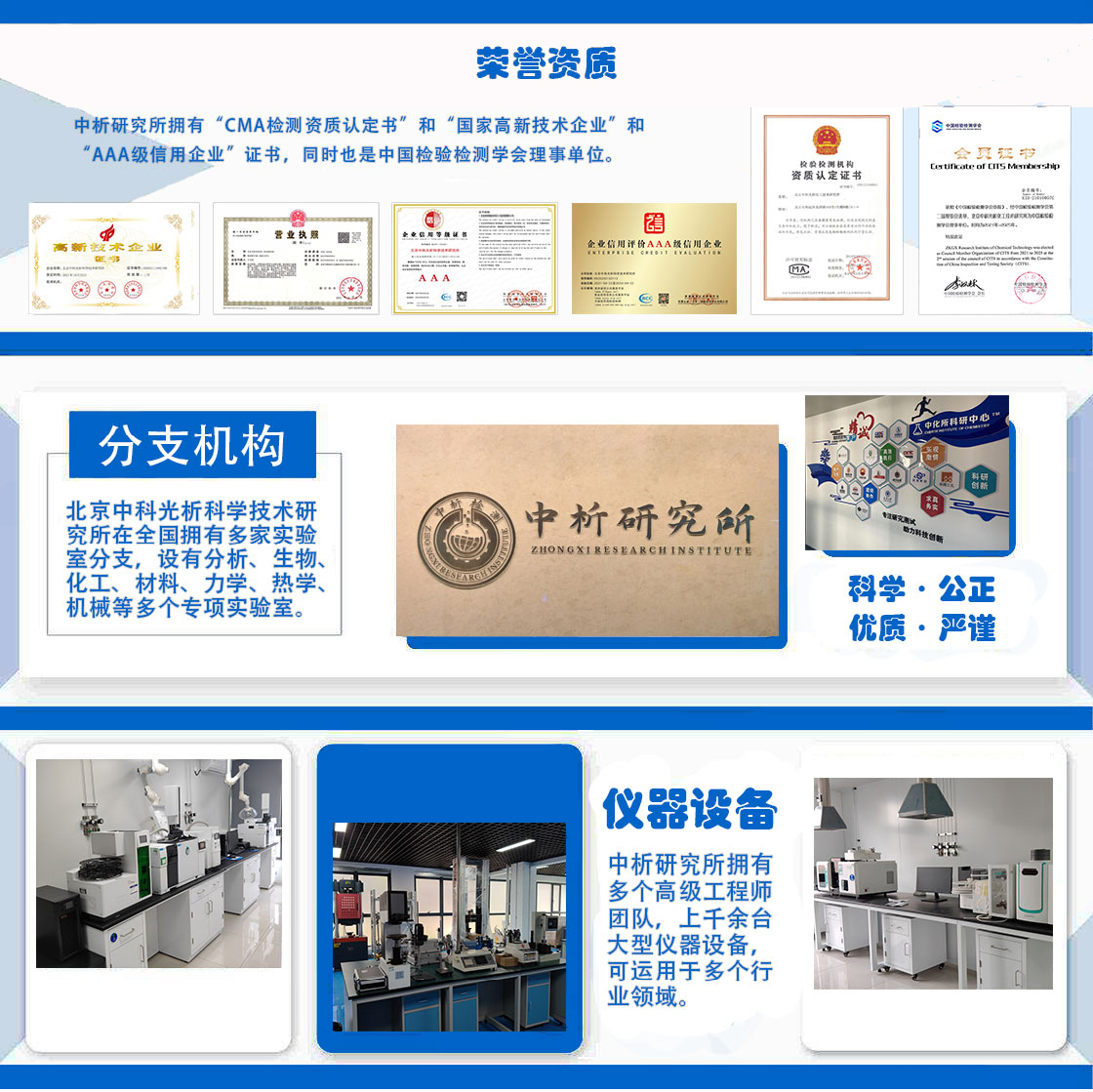
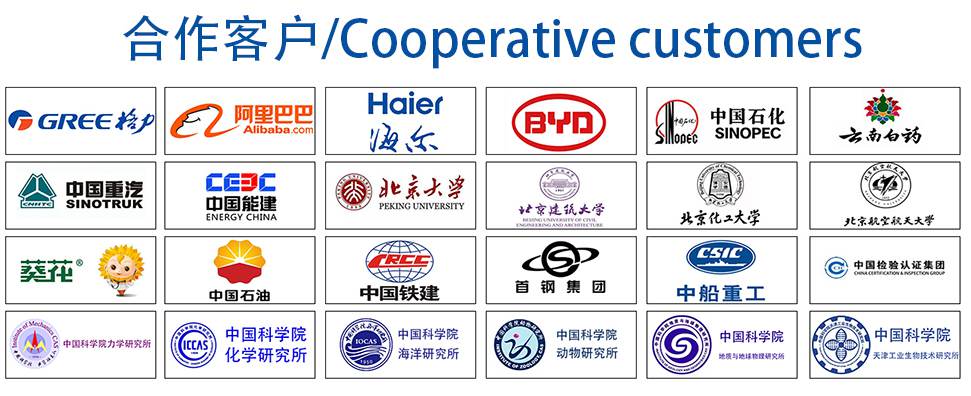