测压装置检测的重要性与应用场景
测压装置作为工业生产、医疗设备、航空航天等领域中不可或缺的监测工具,其准确性直接关系到设备运行安全与测量数据可靠性。随着技术发展,测压装置从传统的机械式压力表到智能数字传感器不断迭代,但无论哪种类型,定期检测校准都是确保其性能的核心环节。未通过检测的装置可能导致压力参数误判,轻则影响生产效率,重则引发设备损坏甚至安全事故。因此,测压装置检测已成为设备维护和质量管理体系中的强制性要求。
测压装置检测的核心项目
在检测过程中,需针对以下关键指标进行系统性验证:
1. 压力范围校核
检测装置的量程覆盖能力,包括最大工作压力和最小分辨率,确保其适应实际工况需求。实验室环境下通过标准压力发生器模拟不同压力点,对比被测装置输出值与标准值的偏差。
2. 精度与线性度测试
使用高精度校准仪验证装置在全量程范围内的误差率,分析其线性响应特性。非线性误差或回差超过标准值时需进行调校或更换。
3. 密封性与耐压性检测
通过加压保持试验验证装置在极限压力下的密封性能,观察是否存在泄漏、变形或结构损坏,持续时间通常为30分钟至2小时。
特殊功能与环境的附加检测
1. 动态响应特性
对于高频压力监测场景(如液压系统),需测试装置的响应时间、频率带宽及信号稳定性,使用快速压力脉冲发生器模拟突变工况。
2. 环境适应性验证
在极端温度(-40℃~150℃)、湿度(95%RH)或振动条件下测试装置性能,确保其在复杂环境下的可靠性。
3. 信号输出完整性
针对智能数字测压装置,需检测模拟信号(4-20mA)或数字信号(RS485、HART协议)的传输稳定性与抗干扰能力。
检测标准与周期管理
检测需依据GB/T 1226-2017《一般压力表》或ISO 国际标准执行,不同行业另有补充规范(如TSG 21-2016特种设备规范)。常规检测周期为6-12个月,高风险领域需缩短至3个月。检测后需出具包含修正系数、不确定度分析的技术报告,并加贴校准标识。
通过系统化的检测流程,可最大限度降低测压装置失效风险,为设备安全运行和工艺优化提供数据支撑。企业应建立完整的检测档案,结合物联网技术实现装置状态的实时监控与预测性维护。
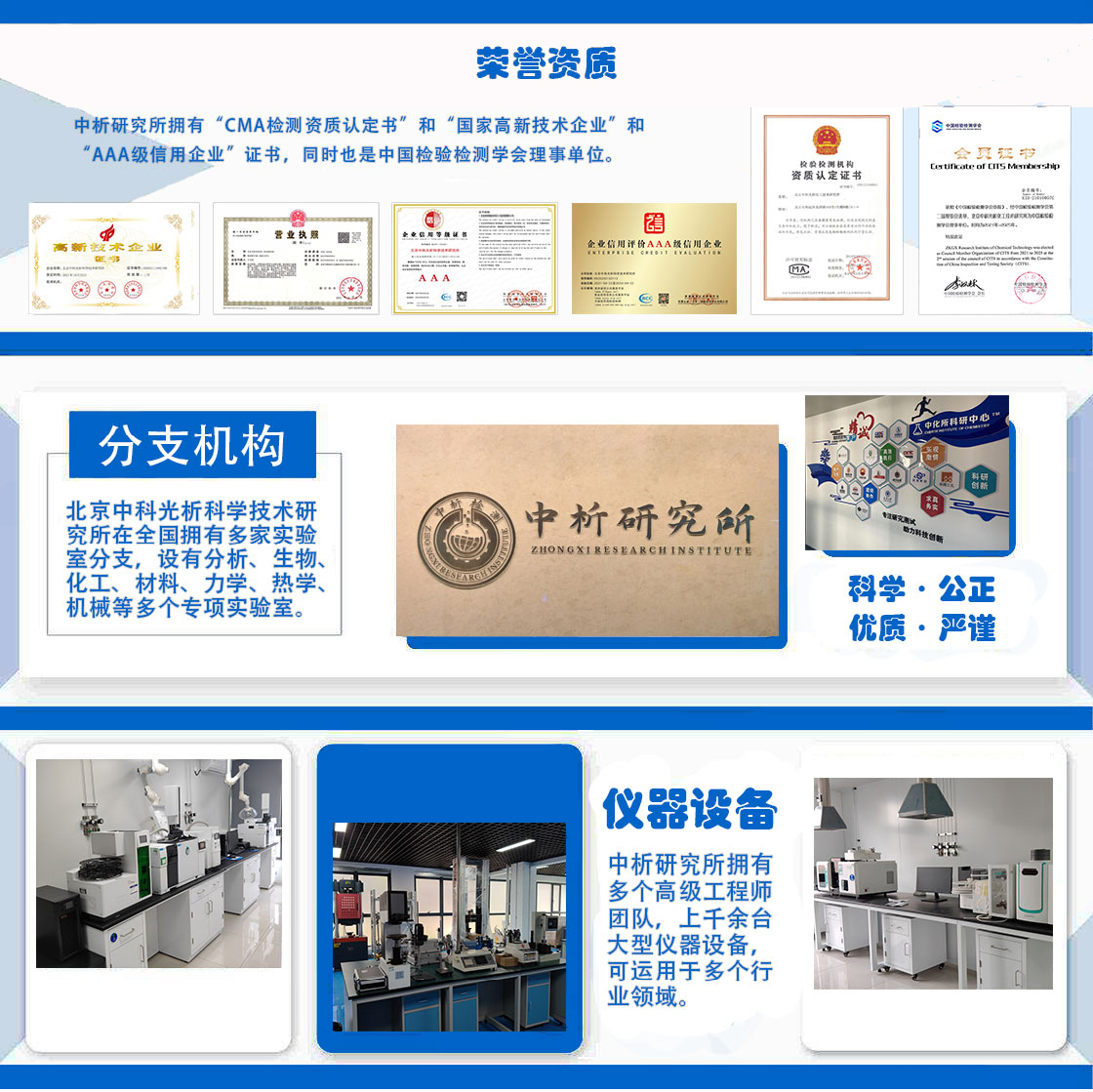
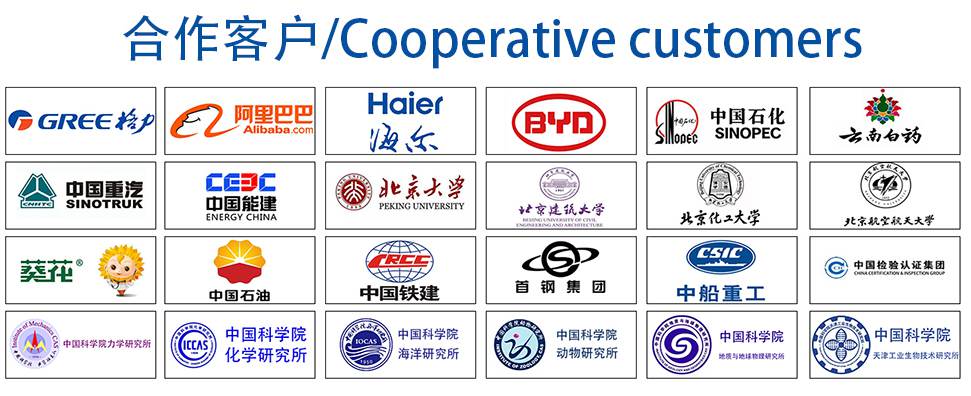