压力连接器检测的重要性与关键项目
压力连接器作为工业管道系统、液压设备及高压容器中的核心组件,承担着传递流体介质、维持密封性和承受工作压力的关键作用。其性能直接关系到设备运行的安全性、稳定性和使用寿命。在石油化工、航空航天、能源电力等高风险领域,一旦压力连接器因质量问题发生泄漏或结构失效,可能引发严重的安全事故和财产损失。因此,通过系统性检测评估其力学性能、密封效果及材料可靠性,成为保障工业安全的重要环节。
压力连接器检测的核心项目
1. 外观与尺寸检测
通过目视检查与精密测量工具(如游标卡尺、投影仪等)对连接器表面质量进行评估,重点检测裂纹、划痕、锈蚀等缺陷,同时验证螺纹精度、端面平面度及关键尺寸是否符合设计标准(如ISO 8434、SAE J514)。
2. 密封性能测试
采用气压试验(最高达设计压力的1.5倍)或液压试验(保压时间≥30分钟),结合检漏液、氦质谱仪等设备检测微泄漏。对于动态连接器还需模拟实际工况下的振动密封性能,确保反复拆装后的密封可靠性。
3. 耐压与爆破压力测试
通过分级增压法验证连接器的静态承压能力,记录变形量与压力曲线;爆破试验则需持续加压至部件失效,实测爆破压力值需达到额定值的2.5倍以上(依据ASME B16.34标准)。
4. 材料理化分析
使用光谱仪、金相显微镜等设备对材质成分、硬度(洛氏/维氏硬度计)、金相组织进行检测,确认材料牌号是否匹配(如316L不锈钢、钛合金等),并评估热处理工艺对强度的影响。
5. 疲劳寿命试验
模拟交变载荷环境,执行高频次(≥10^5次)压力循环测试,检测连接器在脉动压力下的抗疲劳性能,结合断口分析预测实际使用寿命。
6. 环境适应性检测
包括盐雾试验(按ASTM B117标准)、高温蠕变试验(200-400℃)、低温冲击测试(-50℃)等,评估连接器在极端温度、腐蚀介质等复杂工况下的性能表现。
检测技术的创新与发展
当前行业已逐步引入数字射线检测(DR)、相控阵超声检测(PAUT)等无损检测技术,结合有限元分析(FEA)进行应力分布模拟,实现缺陷的精准定位与寿命预测。部分高端检测机构还建立了智能监测系统,通过嵌入式传感器实时采集压力、温度等参数,推动检测过程向智能化、在线化方向发展。
通过上述多维度的检测体系,可有效识别压力连接器的潜在风险,为产品质量控制提供科学依据,同时为优化设计和工艺改进指明方向。规范的检测流程不仅是行业准入的硬性要求,更是保障工业安全、提升企业核心竞争力的重要手段。
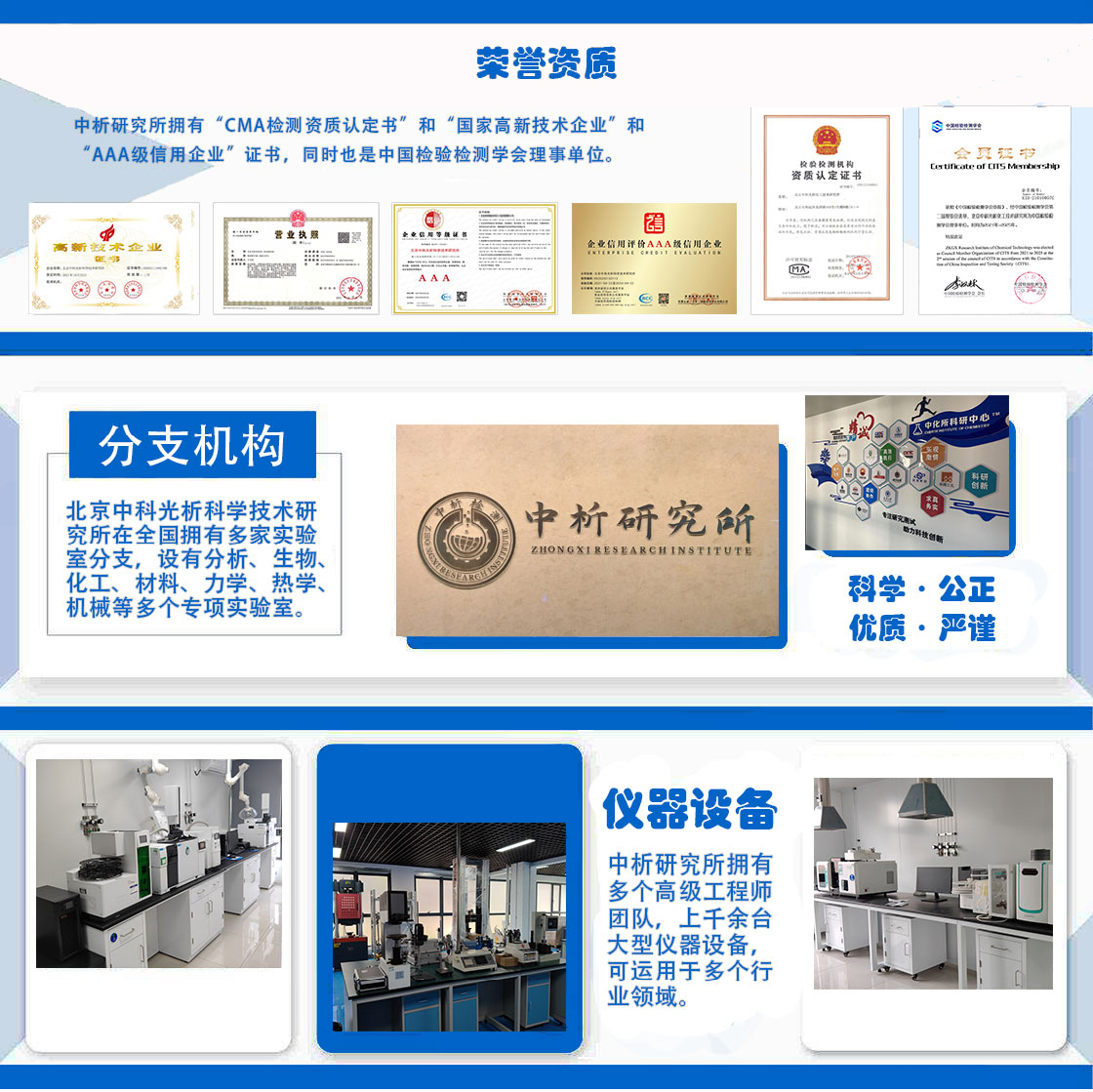
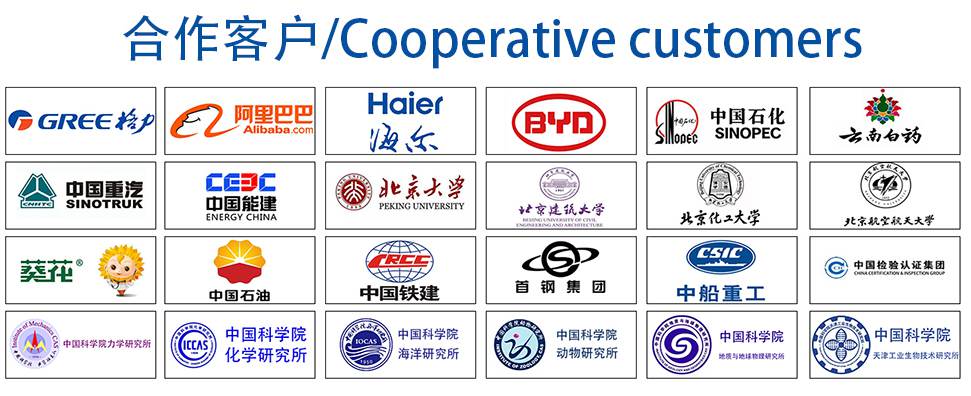