铸铁机体检测技术与关键项目解析
铸铁机体作为机械设备的核心承力部件,广泛应用于发动机、机床、压缩机等工业领域。其质量直接关系到设备的使用寿命、运行稳定性和安全性。随着工业制造对精度和可靠性要求的提升,铸铁机体检测已成为生产流程中不可或缺的环节。本文将从材料特性、加工质量到使用性能等维度,系统阐述铸铁机体的检测要点。
一、化学成分检测
通过光谱分析仪对碳、硅、锰、磷、硫五大元素进行定量分析,确保符合GB/T 9439标准要求。碳当量(CE)需控制在3.6-4.3范围内,磷含量严格限制在0.15%以下,以防止冷脆现象。特殊牌号铸铁需额外检测铬、钼等合金元素。
二、金相组织检测
采用显微镜观察石墨形态(A型为优)、基体组织(珠光体含量≥95%)、化合物分布等微观结构。依据JB/T 9211标准评定石墨长度(100-300μm)、珠光体片间距(0.01-0.03mm)等关键指标,确保材料具备均匀的力学性能。
三、机械性能检测
按照GB/T 228.1进行拉伸试验,抗拉强度需达到HT250(≥250MPa)以上等级。布氏硬度测试(HBW 10/3000)应分布在180-250区间,配合冲击试验(≥12J/cm²)评估材料韧性。对于大型机体需进行局部硬度梯度检测。
四、尺寸精度检测
使用三坐标测量仪对主轴承孔、缸孔等关键部位的孔径(公差H7)、圆度(≤0.02mm)、同轴度(≤0.05mm)进行精密检测。平面度要求控制在0.1mm/m以内,螺栓孔位置度偏差需小于0.3mm。
五、无损检测项目
磁粉探伤(MT)检测表面裂纹,渗透检测(PT)发现0.1mm级缺陷,超声波探伤(UT)评估内部缩孔、夹渣等缺陷。根据ASTM E125标准,不允许存在长度超过5mm的线性缺陷,单个气孔直径需小于3mm。
六、特殊环境适应性检测
高温蠕变试验(400℃×1000h变形量≤0.2%)、耐腐蚀试验(盐雾试验48h表面无红锈)、振动疲劳测试(10⁷次循环无裂纹)等专项检测,模拟实际工况验证机体可靠性。
通过上述系统的检测体系,可有效控制铸铁机体从原材料到成品的全流程质量。建议生产企业建立包含来料检测、过程抽检、成品全检的三级检测制度,并定期进行检测设备校准(符合ISO/IEC 17025要求),确保检测数据的准确性和可追溯性。专业的检测方案能为铸铁机体的安全使用提供有力保障。
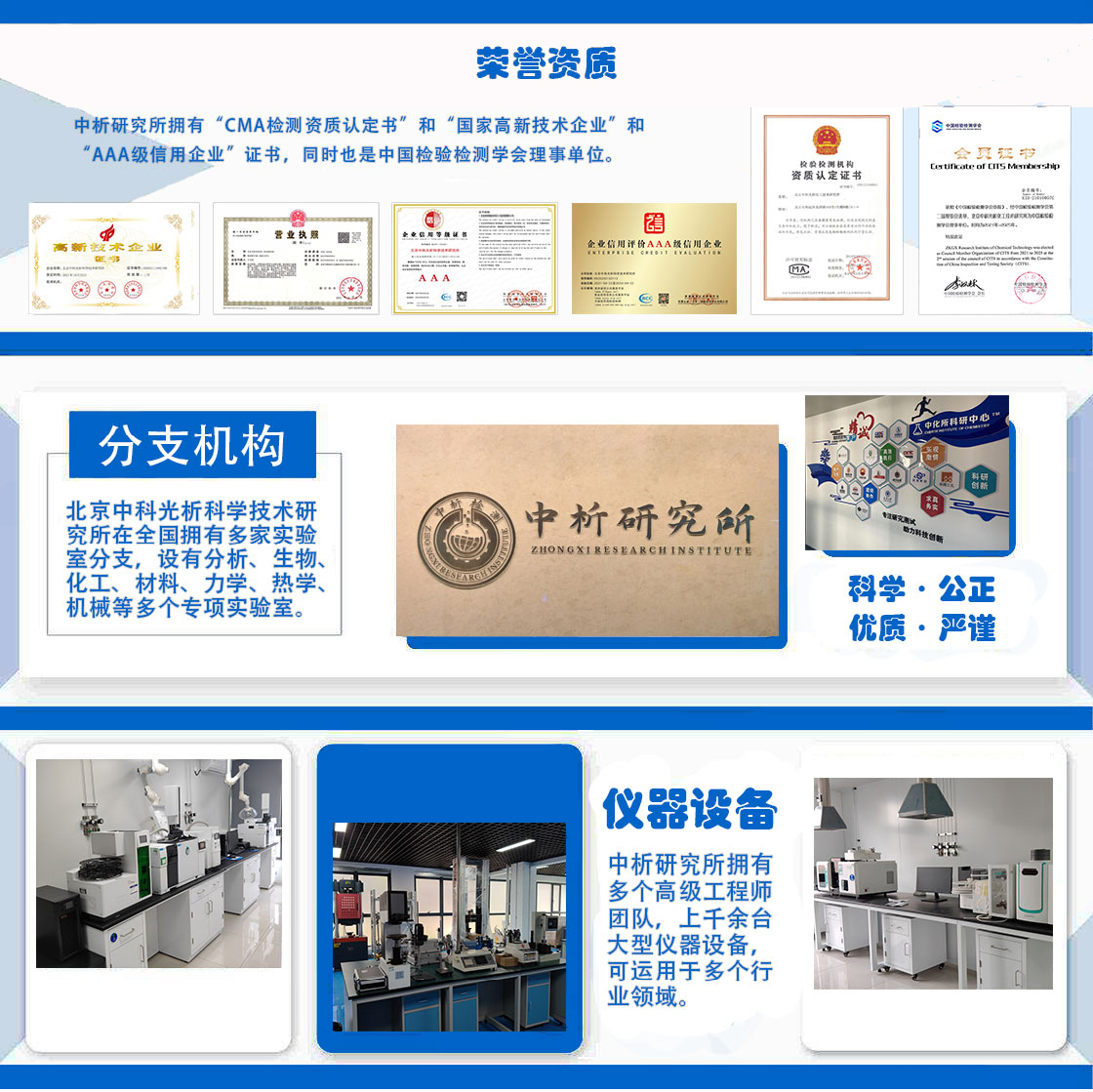
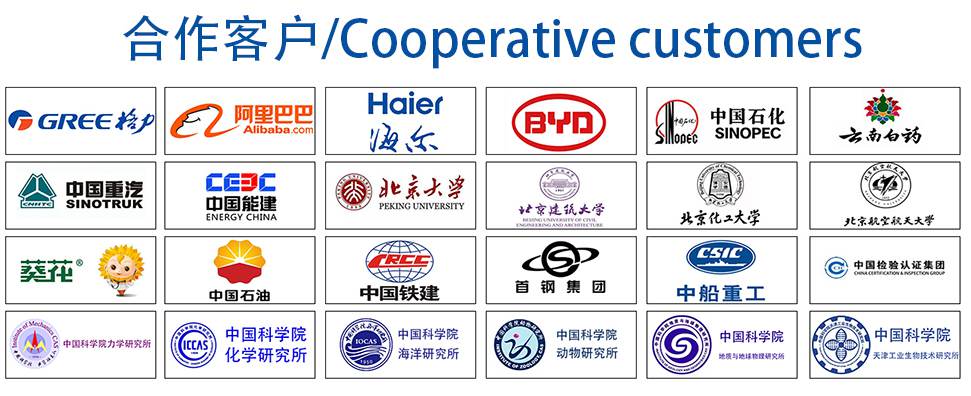