多功能装盒机检测的关键项目与标准化流程
在食品、医药、日化等行业的自动化生产线中,多功能装盒机作为核心包装设备,承担着产品入盒、封口、贴标等关键任务。其性能直接影响生产效率、包装质量和企业运营成本。为确保设备在高速运行、复杂工况下的稳定性和安全性,需通过系统性检测验证其机械、电气及功能性指标。本文将重点解析多功能装盒机的核心检测项目,帮助企业建立科学的质量控制体系。
一、机械结构稳定性检测
针对传动系统、模具适配性及振动噪声进行多维评估:通过持续72小时负载测试验证齿轮箱温升≤45℃;采用激光测距仪检测装盒模具与产品尺寸的匹配精度(误差≤±0.5mm);在最大运行速度下测量机身振动幅度(≤0.15mm)及噪音等级(≤75dB)。重点排查输送链卡滞、同步带打滑等机械故障隐患。
二、电气控制系统检测
使用数字示波器检测PLC信号响应时间(≤5ms),验证光电传感器触发精度;通过EMC测试确保在300V/m电磁干扰下仍能稳定运行;模拟突发电压波动(±15%)时设备断电保护功能。同时检测伺服电机过载保护阈值是否符合ISO13849标准要求。
三、包装功能性能验证
按照GB/T 26989标准开展包装质量测试:连续处理1000件样品时,检测开盒成功率(≥99.8%)、折页到位率(≥99.5%)及喷码识别率(≥99.9%)。特别需要验证异型包装物的适应性,测试设备在3分钟内完成模具切换的可靠性。
四、安全防护系统测试
采用安全回路检测仪验证急停按钮响应时间≤0.1秒;安装光幕传感器测试遮挡报警延迟≤20ms;模拟机械臂异常位移时,检测安全联锁装置是否在0.5秒内切断动力源。所有防护装置需通过EN ISO 14119标准认证。
通过上述检测项目的严格实施,可系统评估装盒机的综合性能指标,帮助企业建立设备全生命周期管理档案。建议每季度开展预防性检测,并根据生产需求升级检测标准,切实保障自动化包装线的稳定高效运行。
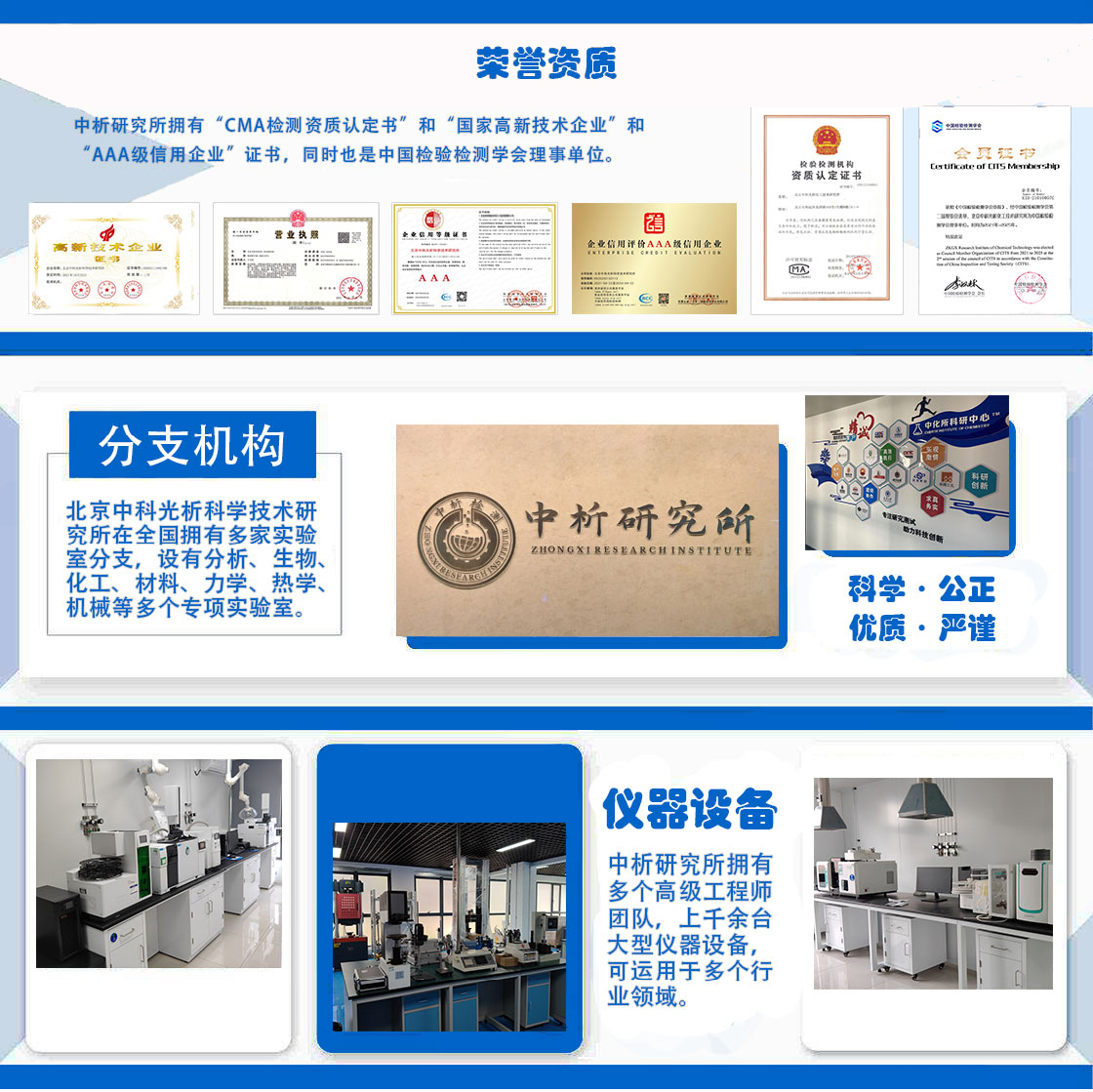
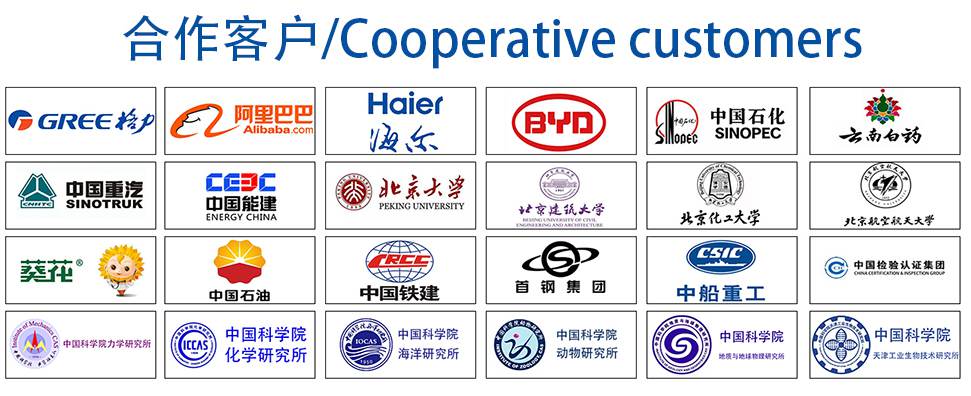