胶带断裂标称应变检测的重要性
在工业生产和日常生活中,胶带作为一种广泛使用的粘接材料,其力学性能直接影响产品的可靠性和安全性。断裂标称应变(Nominal Strain at Break)是衡量胶带在拉伸过程中变形能力的重要指标,指试样在断裂前的最大应变值。通过检测这一参数,可以评估胶带在承受外力时的延展性、抗撕裂性及耐久性,为产品设计、质量控制和工程应用提供关键数据支撑。尤其在包装、电子、汽车制造等领域,胶带若在低于标称应变值时发生断裂,可能导致设备失效、密封泄漏甚至安全事故,因此建立科学的检测流程至关重要。
检测项目内容与标准
胶带断裂标称应变检测的核心项目包括:试样制备、拉伸测试、数据采集与分析三个主要阶段。根据国际标准(如ISO 29863、ASTM D3759)和行业规范,检测需在恒温恒湿环境下进行。试样需按标准尺寸裁剪(通常为25mm宽、150mm长),并确保无气泡、折痕等缺陷。测试过程中,万能材料试验机以恒定速率(通常5mm/min)施加拉力,实时记录应力-应变曲线,最终通过断裂点对应的应变值计算标称应变。
关键检测设备与技术要点
检测系统通常由高精度电子拉力机、非接触式光学应变测量仪(如DIC数字图像相关系统)和数据采集软件组成。设备需定期校准以保证测量误差≤1%。技术要点包括:夹具防滑设计避免试样打滑;应变片或激光位移传感器的高频采样(≥100Hz);以及环境温湿度控制(23±2℃,50±5%RH)。特殊胶带(如双面胶、导电胶)还需考虑附加参数,如剥离强度对测试结果的交叉影响。
数据解释与质量控制
合格判定需结合标称应变值与离散系数(CV值)。行业通常要求均值达到标称值的90%-110%,且CV≤15%。异常数据需排查试样制备误差(如厚度不均)或设备系统偏差。对于各向异性胶带,需测试纵向和横向的应变差异。近年来,部分企业引入人工智能算法,通过历史数据建模预测胶带疲劳寿命,进一步扩展了断裂应变检测的应用价值。
行业应用与发展趋势
该检测技术已广泛应用于3M、德莎等胶带制造商的品控体系,并在新能源电池封装、柔性显示屏贴合等新兴领域发挥关键作用。随着材料科学的进步,针对超薄纳米胶带(厚度<10μm)和高弹性体胶带(应变>500%)的检测方法正逐步标准化。未来,在线实时检测系统和多参数耦合分析技术将成为提升检测效率的重要方向。
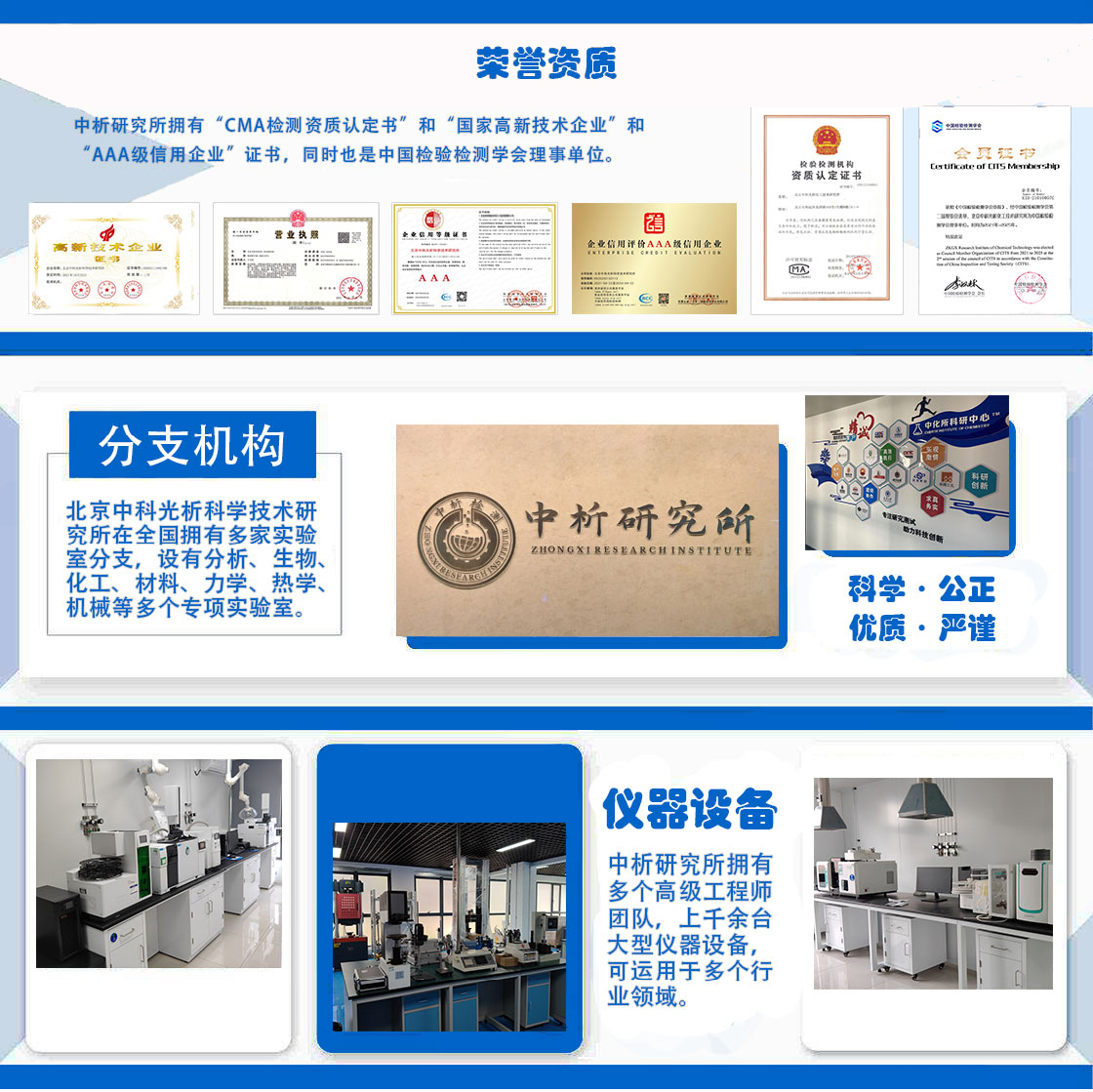
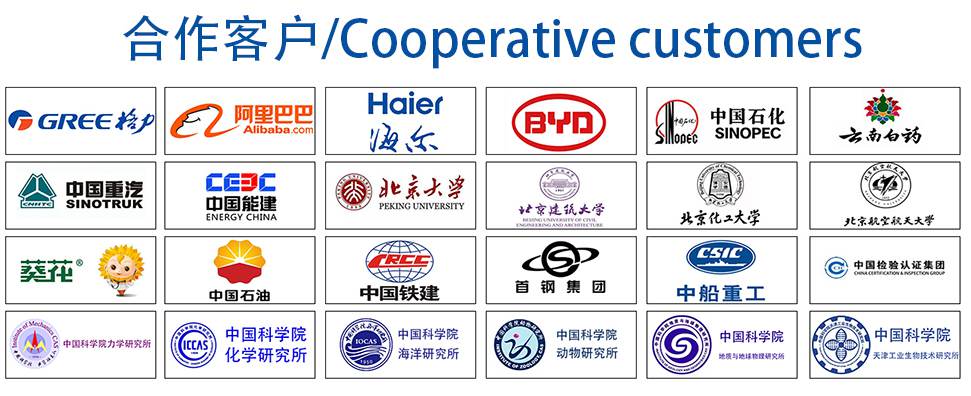