玻璃印刷机检测项目及技术要求
玻璃印刷机作为深加工玻璃生产的核心设备,其印刷精度、稳定性和可靠性直接影响产品合格率与生产效率。随着光伏玻璃、电子显示玻璃等高端领域对印刷质量要求的持续提升,系统化、规范化的设备检测体系显得尤为重要。常规检测需覆盖机械传动、定位系统、油墨传输、烘干固化四大模块,结合动态测试与静态分析,确保设备在±0.05mm的印刷误差范围内稳定运行。
核心检测项目分类
1. 印刷精度检测
采用高精度激光位移传感器与CCD视觉系统,重点检测网版定位重复精度(≤±0.03mm)、刮刀压力均匀性(波动值<5%)以及印刷套位误差(多层印刷偏移量<0.1mm)。通过模拟不同速度(10-30m/min)下的连续印刷,验证设备动态稳定性。
2. 油墨传输系统检测
使用流量计与黏度计监控油墨泵送效率(误差±2%以内),检测喷墨头堵塞率(单次工作周期<0.5%异常喷射)及管路压力波动(压力波动值<0.1MPa)。同步开展72小时持续供墨测试,验证系统密封性与抗沉淀能力。
3. 烘干固化单元检测
通过红外热成像仪测量烘箱温度均匀性(温差≤±3℃),使用UV能量计核查固化灯功率衰减(500小时衰减率<8%)。重点监测玻璃表面温升曲线,确保基材受热变形量<0.02mm/m。
4. 机械传动系统检测
采用振动分析仪评估导轨和丝杠的磨损状态(振动幅值<5μm),测试伺服电机扭矩输出稳定性(波动值<额定值3%)。同步检查同步带张紧力(张力计读数误差±2N)和轴承温升(连续运行温度≤65℃)。
功能性验证与安全检测
执行急停响应测试(制动时间<0.5秒)、静电消除效率(表面电阻<10^6Ω)以及防爆装置有效性(危险区域氧浓度<8%)。通过3000次连续启停实验验证系统耐久性,故障间隔时间(MTBF)需达到2000小时以上。
完善的检测体系需结合ISO 9001质量管理规范与设备制造商技术手册,建议每季度开展预防性检测,并在产品规格变更后执行专项性能验证。企业应建立检测数据库,通过趋势分析实现预测性维护,将设备非计划停机率控制在1%以内。
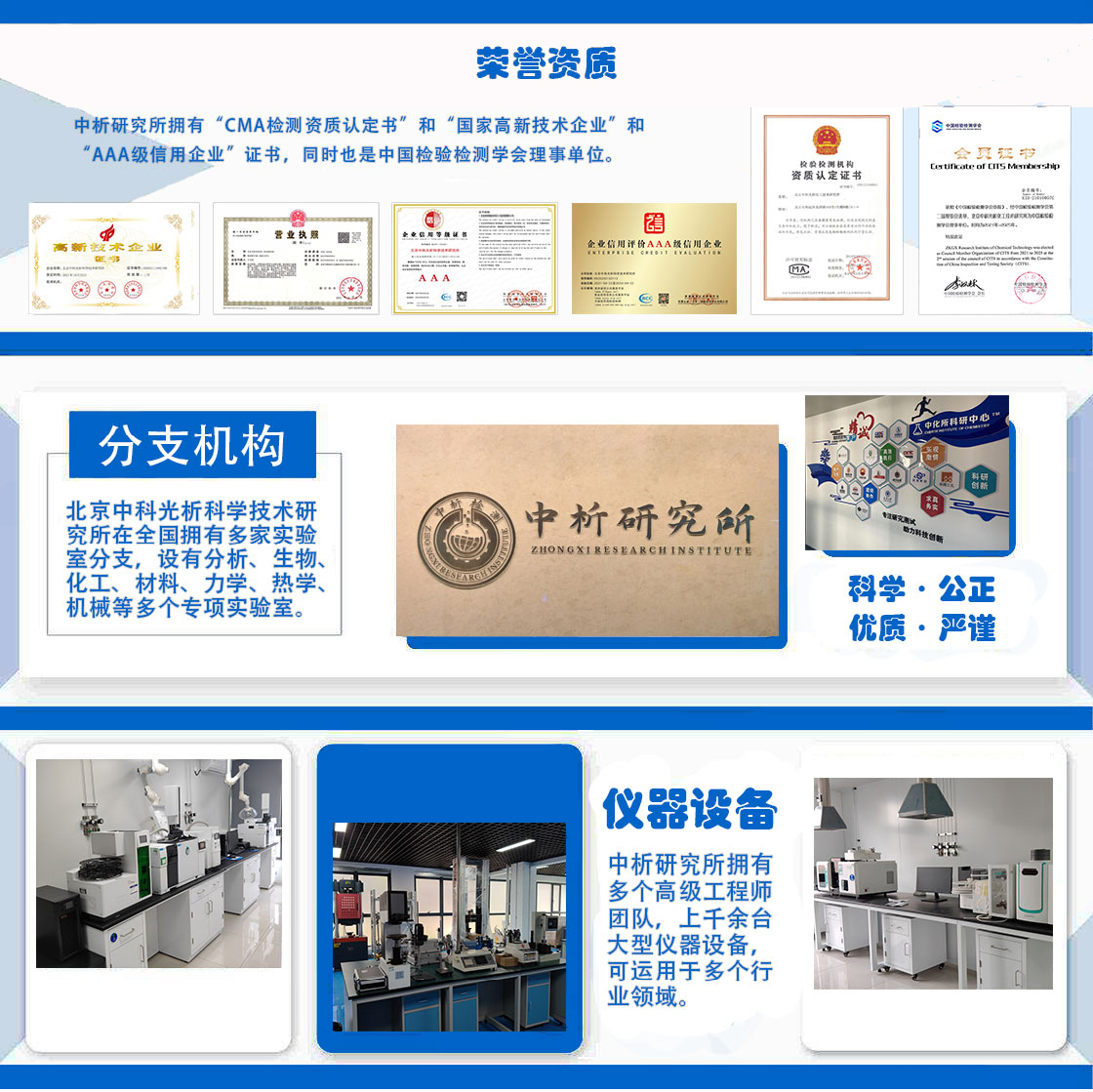
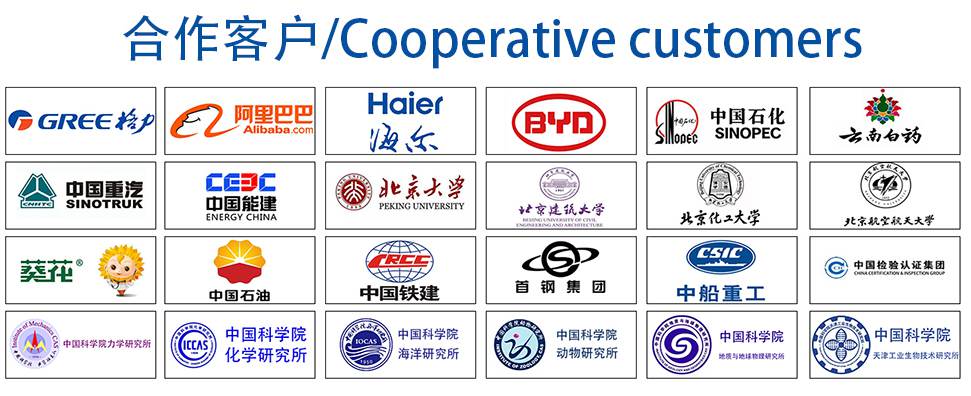