汽车传动轴总成检测的重要性与核心内容
汽车传动轴总成作为动力传输系统的核心部件,承担着将发动机扭矩传递至驱动轮的关键任务。其性能直接关系到车辆的行驶安全性、动力效率及使用寿命。由于传动轴长期承受交变载荷、高速旋转和复杂路况的冲击,任何细微的损伤或装配偏差都可能导致振动加剧、异响甚至断裂风险。因此,针对传动轴总成的系统性检测是车辆维修、生产质检和定期保养中不可或缺的环节。本文将从核心检测项目出发,详细解析传动轴总成的检测流程与技术要点。
一、外观与几何尺寸检测
首先需对传动轴总成进行目视检查,包括表面是否存在裂纹、锈蚀、变形或焊接缺陷,并确认防尘罩、平衡块等附件的完整性。使用卡尺、千分尺等工具测量轴管直径、长度及法兰盘安装孔位尺寸,确保符合原厂设计公差(通常要求轴管直线度误差≤0.3mm/m)。同时通过三坐标测量仪验证花键轴与万向节叉的配合间隙,防止因磨损导致动力传递失效。
二、动平衡性能测试
传动轴不平衡是引发车辆共振的主要原因。检测时需将总成置于专用动平衡机上,在模拟工作转速(通常为800-4000r/min)下测量不平衡量。根据国家标准GB/T 9239,乘用车传动轴允许残留不平衡量应小于15g·cm,超标时需通过增减平衡块或调整装配角度进行校正,直至径向跳动量≤0.8mm。
三、万向节磨损与润滑检测
使用百分表测量十字轴轴承的轴向间隙(标准值通常<0.05mm),若超过0.15mm则需更换轴承组件。借助内窥镜检查万向节内部滚针磨损情况,同时评估润滑脂的污染度和填充量(填充率应达85%以上)。对于带伸缩花键的传动轴,需检测花键副的侧隙(允许范围0.1-0.3mm)及滑动顺畅性。
四、材料强度与耐久性试验
通过硬度计检测轴管表面硬度(通常要求HRC28-32),并取样进行金相分析以确认材料组织无脱碳、晶粒粗化等缺陷。在疲劳试验机上模拟50万次循环载荷(扭矩波动范围±30%额定值),检测传动轴是否出现裂纹扩展或永久变形。根据QC/T 29082标准,合格产品应能承受1.5倍额定扭矩的静态扭转试验而不发生断裂。
五、NVH特性与动态性能验证
在整车或台架试验中,通过加速度传感器监测传动轴在加速/减速工况下的振动频谱,主要关注80-200Hz频段的异常峰值。同时使用噪声计测试传动系噪音水平(要求≤72dB(A)@3000r/min)。对于四驱车型还需验证传动轴与分动箱、差速器的相位匹配性,避免产生干涉振动。
六、综合功能测试与数据判定
最终检测需结合扭矩测试仪、红外热像仪等设备,在模拟真实负载条件下连续运行2小时,记录以下关键参数:
1. 最大传递扭矩偏差≤±5%
2. 温升幅度≤40℃(环境温度25℃基准)
3. 万向节工作角度变化率<2°/s
所有检测数据需与QCDS(质量控制系统)中的历史记录对比,运用SPC统计方法判定产品状态,确保不合格品拦截率≥99.7%。
通过以上系统的检测流程,可全面评估传动轴总成的机械性能、可靠性和匹配精度。随着智能检测技术的发展,基于工业CT的内部缺陷扫描、基于AI的振动模式识别等新技术正在逐步推广应用,推动汽车传动系统的检测体系向更高精度、更高效率方向演进。
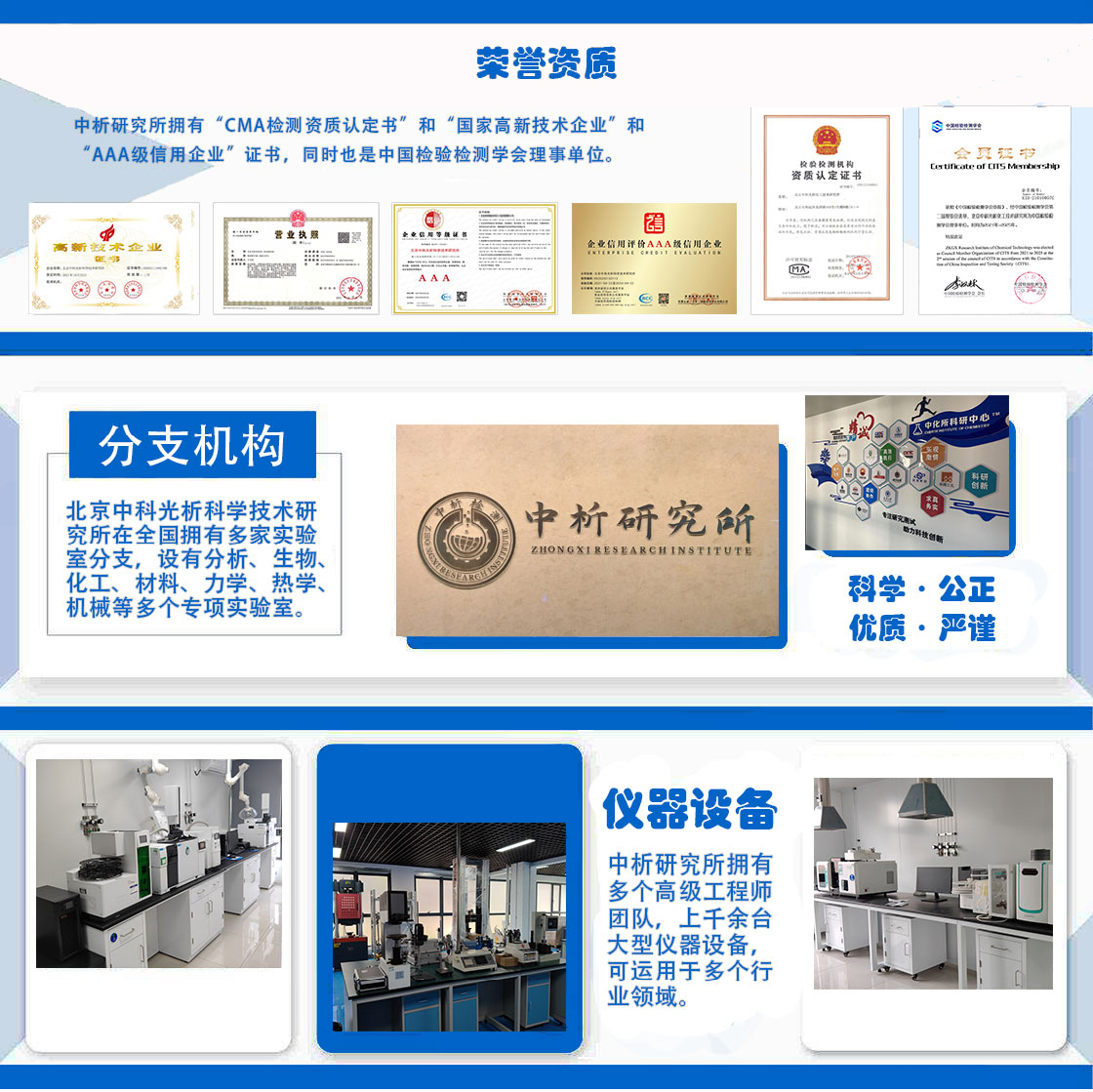
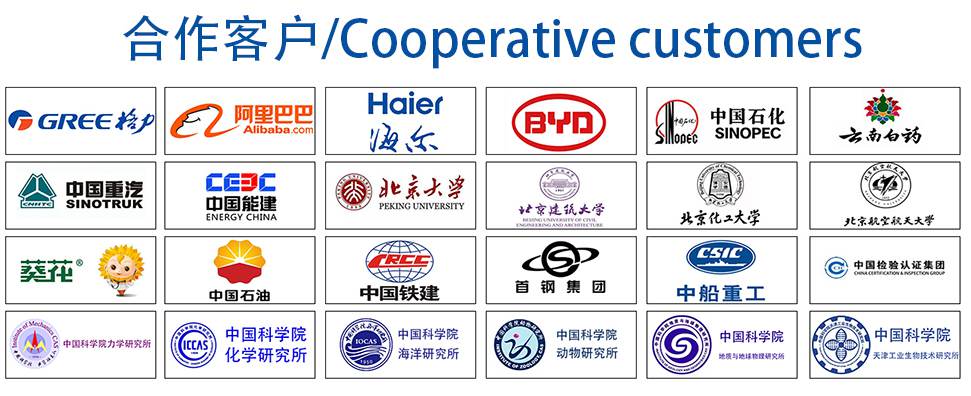