冶金检测:工业质量的守护者
冶金检测是材料科学与工业制造领域的核心技术之一,其核心目标是通过系统性分析、测试和评估手段,确保金属材料的成分、性能及结构符合生产标准和实际应用需求。在航空航天、汽车制造、能源装备、建筑桥梁等关键领域,冶金检测贯穿于原材料筛选、工艺优化、成品验收及服役监测的全生命周期,为产品的安全性和可靠性提供科学依据。随着智能制造和高端装备的快速发展,冶金检测技术已从传统经验判断发展为高精度仪器分析与数字化智能诊断相结合的现代化体系。
1. 材料成分分析
作为冶金检测的基础环节,材料成分分析通过光谱分析仪(如ICP-OES、XRF)、碳硫测定仪等设备,精确测定金属中主要合金元素(如Cr、Ni、Mo)及杂质元素(如S、P)的含量。例如,航空发动机叶片要求钛合金中氧含量低于0.15%,需采用惰性气体熔融法进行超低氧分析。齐全的激光诱导击穿光谱(LIBS)技术可实现现场快速检测,大幅提升生产线质控效率。
2. 力学性能测试
通过万能材料试验机、冲击试验机等设备,评估金属材料的拉伸强度、屈服强度、延伸率、冲击韧性等核心指标。核电主管道用钢需在-40℃下仍保持高于41J的夏比冲击功,此时需配置低温环境箱的试验系统。近年兴起的数字图像相关(DIC)技术可实时捕捉材料变形过程,为微观力学行为研究提供可视化数据支持。
3. 金相组织分析
借助光学显微镜、扫描电镜(SEM)及电子背散射衍射(EBSD)技术,观察金属晶粒尺寸、相组成、夹杂物分布等微观特征。汽车齿轮渗碳处理后需检测有效硬化层深度及马氏体形态,金相制样需经过切割、镶嵌、研磨、腐蚀等15道精密工序。三维X射线显微镜(3D XRM)的引入,实现了非破坏性三维显微结构重建。
4. 无损检测技术
涵盖超声波检测(UT)、射线检测(RT)、磁粉检测(MT)、渗透检测(PT)及涡流检测(ET)五大常规方法。高铁轮对探伤采用相控阵超声波技术,可检出0.5mm级的疲劳裂纹。太赫兹波检测、红外热成像等新型技术正在航空复合材料检测中崭露头角,检测精度可达微米级。
5. 耐腐蚀性检测
通过盐雾试验箱模拟海洋大气环境,评估镀层、涂层及基材的抗腐蚀能力。深海石油管道需进行长达3000小时的加速腐蚀试验,同时结合电化学阻抗谱(EIS)分析钝化膜稳定性。微区电化学扫描技术(SECM)可实时观测局部腐蚀起始点,为耐蚀合金开发提供关键数据。
6. 高温性能测试
采用高温蠕变试验机、热膨胀仪等设备,研究材料在极端温度下的力学行为。燃气轮机叶片需在900℃环境下持续工作,必须通过长达万小时的高温持久试验。同步辐射光源技术可实时观测高温下晶界滑移过程,为超合金设计提供原子尺度洞察。
7. 尺寸与几何精度检测
运用三坐标测量机(CMM)、激光扫描仪等设备,确保零部件尺寸公差符合设计要求。航空发动机叶片型面检测精度需达到±3μm,需采用非接触式白光干涉测量技术。工业CT扫描可实现复杂内腔结构的全尺寸数字化逆向建模,检测效率较传统方法提升5倍以上。
在智能化转型背景下,冶金检测正与物联网、大数据深度融合。基于机器学习的缺陷自动识别系统可将探伤误判率降低至0.1%以下,区块链技术则为检测数据溯源提供了可信解决方案。未来,随着材料基因工程和量子传感技术的发展,冶金检测将进入"预测式检测"的新纪元,为高端制造领域持续赋能。
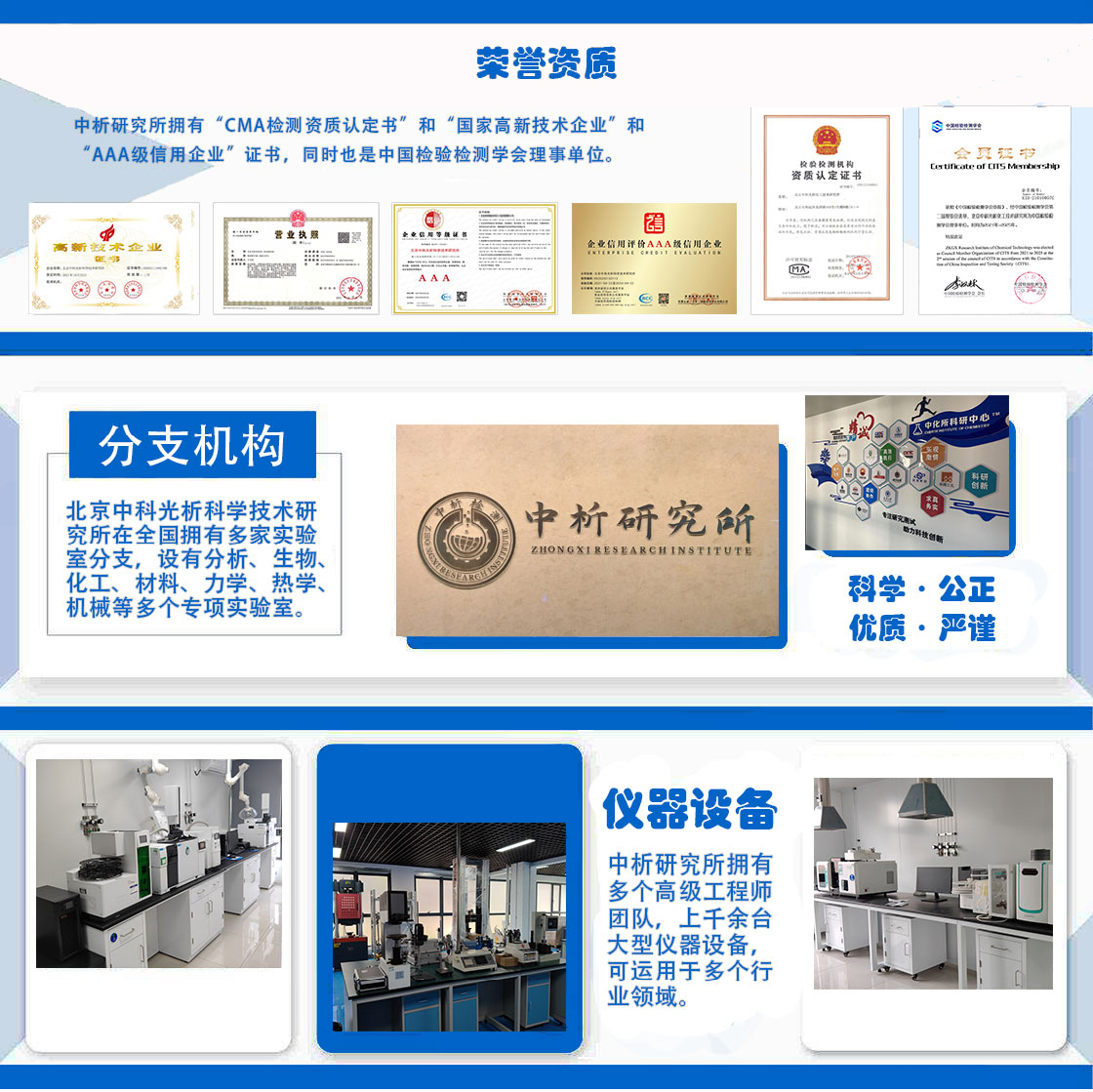
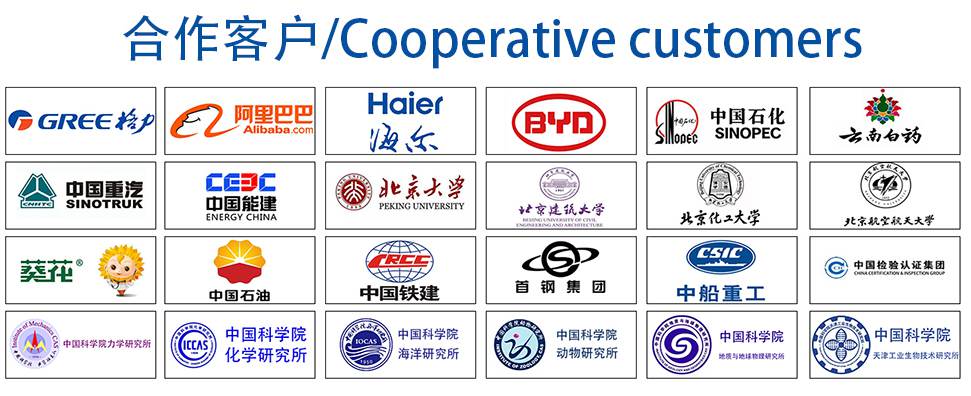