机器人用齿轮传动装置(技术条件)检测的重要性
随着工业自动化与智能制造的快速发展,机器人用齿轮传动装置作为核心动力传递部件,其性能直接影响机器人运行的精度、稳定性和使用寿命。根据GB/T 10095《圆柱齿轮精度》及ISO 1328等标准,针对齿轮传动装置的技术条件检测成为保障机器人可靠性的关键环节。检测内容需涵盖材料特性、几何精度、传动效率、耐久性等维度,同时结合动态负载模拟与环境适应性测试,确保装置满足高速、重载、低噪音等严苛工况需求。
主要检测项目及技术要求
1. 材料性能检测
通过光谱分析、硬度测试(洛氏/维氏)及金相组织观察,验证齿轮材料(如20CrMnTi、42CrMo等)的化学成分、表面硬化层深度及基体强度是否符合设计要求。抗疲劳强度需达到≥800MPa,齿面硬度HRC58-62。
2. 几何精度检测
使用三坐标测量仪、齿轮测量中心等设备检测齿形误差(fa)、齿向误差(Fβ)及齿距累积偏差(Fp),要求精度等级达到ISO 6-7级。同轴度误差≤0.015mm,端面跳动量≤0.02mm。
3. 传动性能测试
在封闭功率试验台上进行空载/负载效率测试,传动效率应≥98%。通过扭矩传感器监测额定转速(3000-6000rpm)下的扭矩波动值,允许误差±2%,反向间隙≤5角分。
4. 耐久性与环境适应性测试
采用加速寿命试验模拟107次循环负载,检测齿面磨损量(≤0.03mm)及点蚀情况。高低温(-40℃~120℃)、湿热(RH95%)、粉尘等环境测试中需保持密封性(IP65)与传动稳定性。
5. 振动与噪音评估
依据ISO 8579-2标准,在消声室内测量1米距离的声压级,要求空载噪音≤65dB(A),满载工况下振动加速度≤2.5m/s²,频谱分析需排除异常谐波成分。
检测方法与设备配置
采用接触式与非接触式检测技术结合:激光干涉仪用于背隙测量,工业CT进行内部缺陷扫描,油液颗粒计数器监测润滑系统清洁度(NAS 6级)。智能检测系统整合DMC数据管理模块,实现检测报告自动生成与SPC过程控制。
结语
机器人齿轮传动装置的标准化检测不仅需要完善的硬件设施,更依赖于多学科交叉的检测体系。随着数字孪生技术的应用,未来将实现实时在线监测与预防性维护,进一步推动机器人传动系统向高精度、高可靠性方向发展。
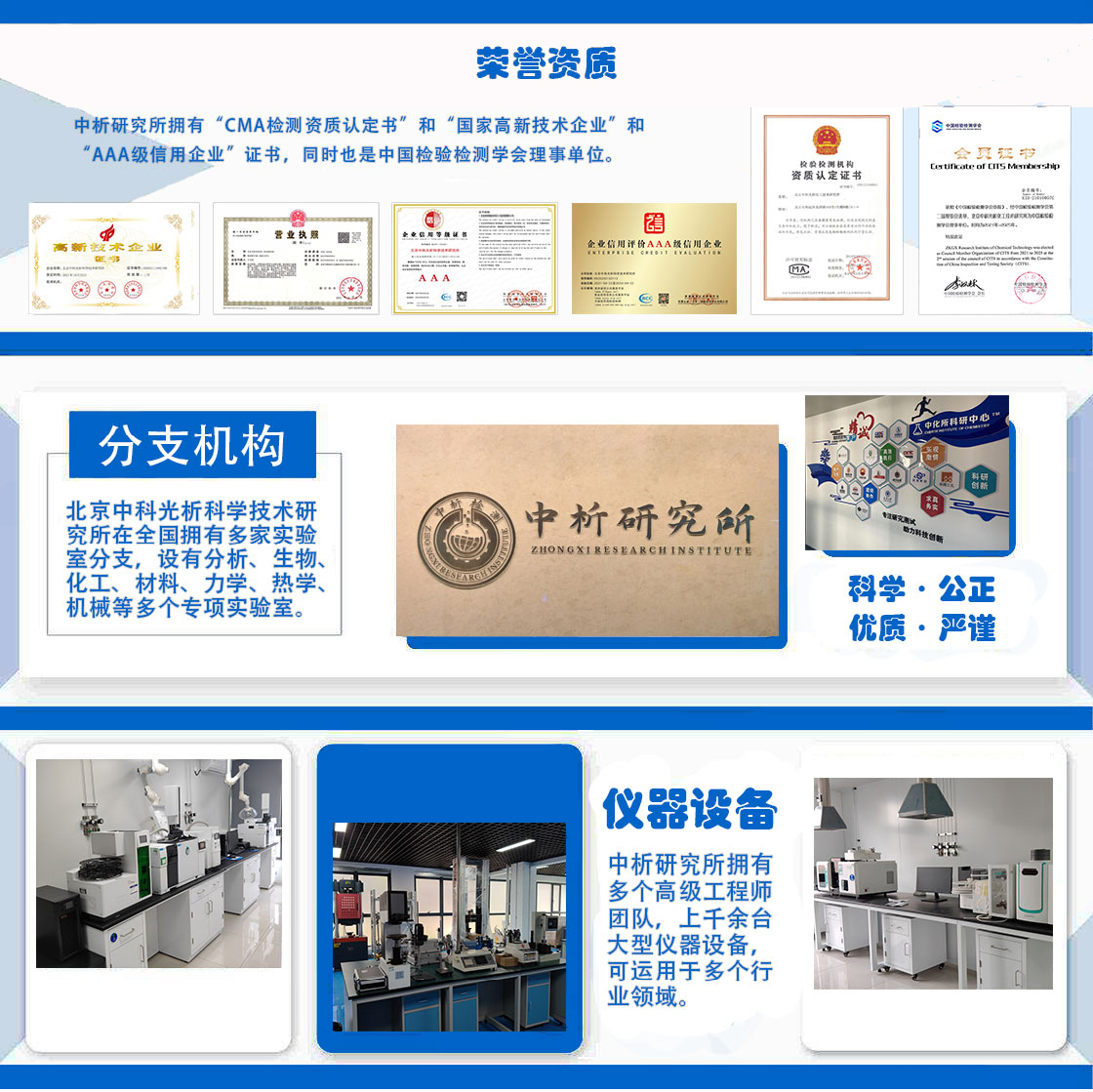
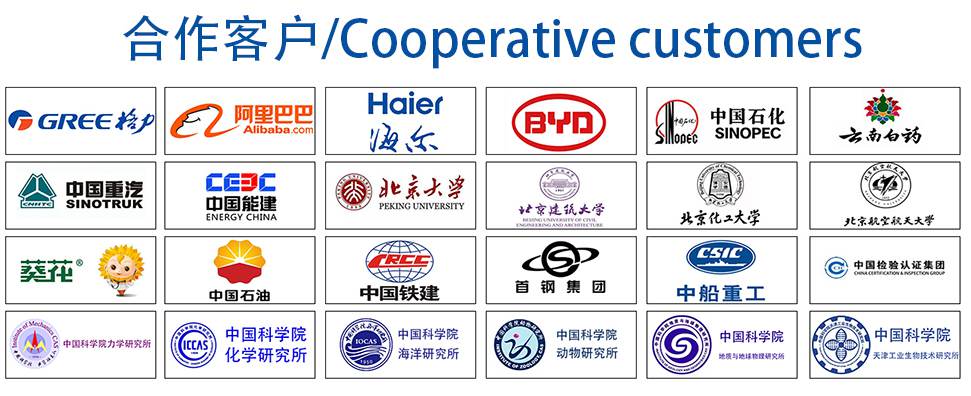