风力发电机组润滑剂检测的重要性
在风力发电机组运行过程中,润滑剂承担着减少机械磨损、散热、防腐蚀等关键功能。随着机组长期处于高负荷、复杂环境(如高湿度、温差大、沙尘等)中运行,润滑剂的性能会逐渐劣化,直接影响齿轮箱、轴承等核心部件的寿命与机组发电效率。定期开展润滑剂检测能够精准评估其理化特性变化,及时发现潜在风险,避免因润滑失效导致的停机损失和维修成本上升。据统计,超过60%的齿轮箱故障与润滑剂问题相关,科学检测可为运维决策提供重要依据。
核心检测项目及技术标准
1. 理化性能检测
通过黏度、水分含量、酸值(TAN)、碱值(TBN)等指标评估润滑剂基础状态。黏度异常可能反映氧化或污染;水分超过0.1%会加速油品氧化并诱发点蚀;酸值升高表明添加剂损耗或氧化产物积累。检测方法遵循ASTM D445(黏度)、ISO 12937(水分)等国际标准。
2. 污染度与颗粒物分析
采用自动颗粒计数器(APC)和铁谱分析技术,检测油液中金属磨屑、粉尘等污染物浓度。齿轮箱润滑剂要求ISO 4406等级不高于18/16/13,超标颗粒会加剧部件磨损。铁谱分析可识别磨损颗粒形态,判断故障类型(如疲劳剥落或切削磨损)。
3. 添加剂成分检测
利用光谱分析(如ICP-OES)定量测定抗氧剂、极压剂(如磷、硫)、防锈剂等关键添加剂的残余浓度。例如,齿轮油中锌(Zn)元素含量低于初始值50%时需补充或换油,确保极压保护性能。
4. 氧化安定性与老化评估
通过旋转氧弹试验(ASTM D2272)和傅里叶红外光谱(FTIR)分析氧化产物(如羰基峰强度),预测润滑剂剩余使用寿命。老化严重的油品会生成胶质、漆膜,堵塞过滤系统。
5. 摩擦磨损特性测试
采用四球试验机(ASTM D4172)模拟极端工况下的润滑性能,测量磨斑直径(WSD)和摩擦系数,验证油膜强度是否满足齿轮箱高负载需求。
检测周期与结果应用
建议每3-6个月对齿轮箱润滑剂进行全套检测,恶劣环境下需缩短至1-3个月。检测数据应与设备振动分析、温度监测结合,建立多维健康评估模型。当关键指标(如酸值上升20%、黏度变化±15%)超出阈值时,需立即采取过滤净化或换油措施,并结合磨粒特征排查机械损伤风险。
结语
风力发电机组润滑剂检测是实现预防性维护的核心环节,通过系统化的数据采集与分析,可延长设备寿命10%-30%,降低运维成本。建议风电场建立标准化的油液监测体系,结合智能传感器与大数据平台,实现润滑状态的实时预警与精准管理。
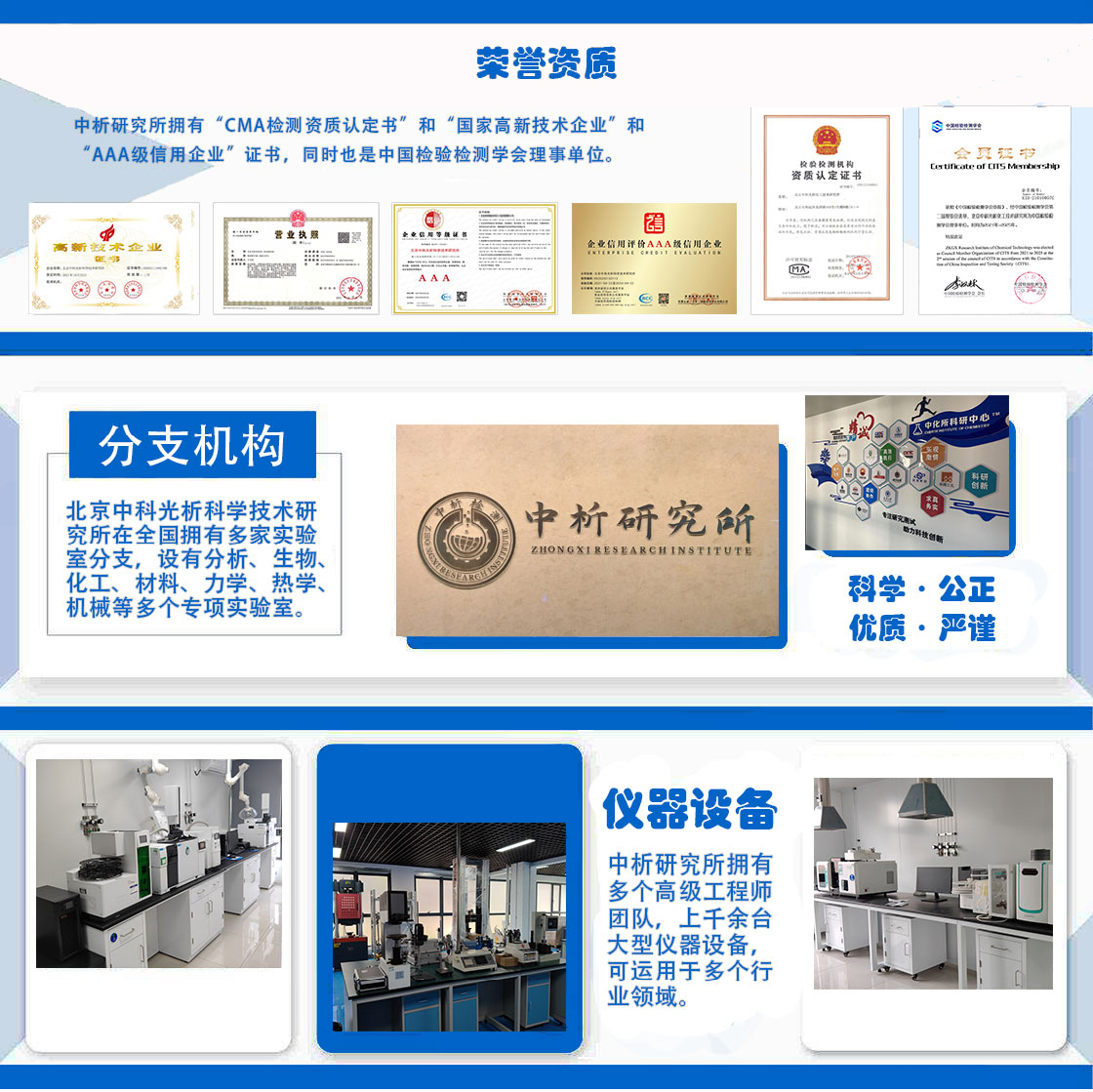
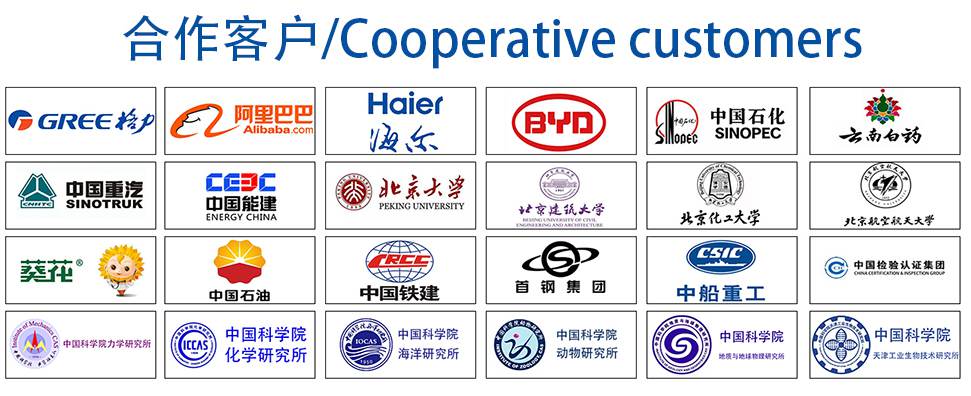