电火花线切割机(单向走丝型)检测的重要性
电火花线切割机(单向走丝型)作为精密加工领域的核心设备,广泛应用于模具制造、航空航天零部件加工等高精度场景。其通过电极丝与工件间的脉冲放电实现材料蚀除,加工精度可达微米级。然而,设备长期运行后易受机械磨损、电气参数漂移、环境温湿度等因素影响,导致加工质量下降。因此,定期开展系统化检测是确保设备性能稳定、延长使用寿命、保障生产安全的关键措施。检测项目需覆盖机械结构、电气系统、加工能力及安全防护等维度,同时需参照国家标准(如GB/T 5291-2018《电火花线切割机床精度检验》)和行业规范执行。
核心检测项目及实施规范
1. 几何精度检测
几何精度是衡量设备基础性能的核心指标,包含以下重点内容:
(1)工作台平面度检测:采用电子水平仪或激光干涉仪,依据GB/T 17421.1标准,要求平面度误差≤0.01mm/m²;
(2)X/Y轴运动垂直度检测:使用直角规配合千分表测量,允差范围应≤0.004mm/200mm;
(3)电极丝导向器同轴度检测:通过专用检具测试各导向轮的同轴偏差,确保≤0.002mm。
2. 加工性能检测
通过标准试件加工验证实际加工能力:
(1)切割速度检测:采用厚度20mm的Cr12MoV模具钢试件,记录单位时间切割面积;
(2)表面粗糙度测试:使用表面轮廓仪测量Ra值,应满足Ra≤1.6μm(精加工模式);
(3)尺寸精度验证:加工标准方孔试件,三坐标测量机检测尺寸偏差需≤±0.005mm。
3. 电气系统检测
(1)脉冲电源参数校核:检测峰值电流、脉宽、间隔时间的设定值与实际输出偏差应<3%;
(2)伺服系统响应测试:通过示波器监测各轴电机的动态响应特性,确保无异常振荡;
(3)绝缘电阻检测:动力线路对地绝缘电阻值需≥20MΩ(500V兆欧表测试)。
4. 安全防护与辅助系统检测
(1)急停装置功能性测试:触发后应在0.5秒内切断所有动力电源;
(2)工作液循环系统检测:过滤精度应达到5μm以下,流量稳定性偏差≤5%;
(3)防电解装置有效性验证:通过铝材试件加工试验观察表面有无异常腐蚀现象。
5. 环境适应性检测
(1)温湿度影响试验:在20-25℃范围内检测加工精度变化量应≤0.003mm/℃;
(2)抗振动性能测试:模拟4Hz-200Hz振动环境,检测设备定位精度衰减率;
(3)电磁兼容性验证:依据GB/T 5226.1标准进行辐射骚扰和抗扰度测试。
检测周期与数据分析
建议每500小时运行后实施日常检测,年度全面检测应包含所有项目。检测数据需录入设备健康管理系统,通过趋势分析预测关键部件寿命。对于重复性超差项目,应及时调整机床参数或更换磨损部件,确保设备始终处于最佳加工状态。
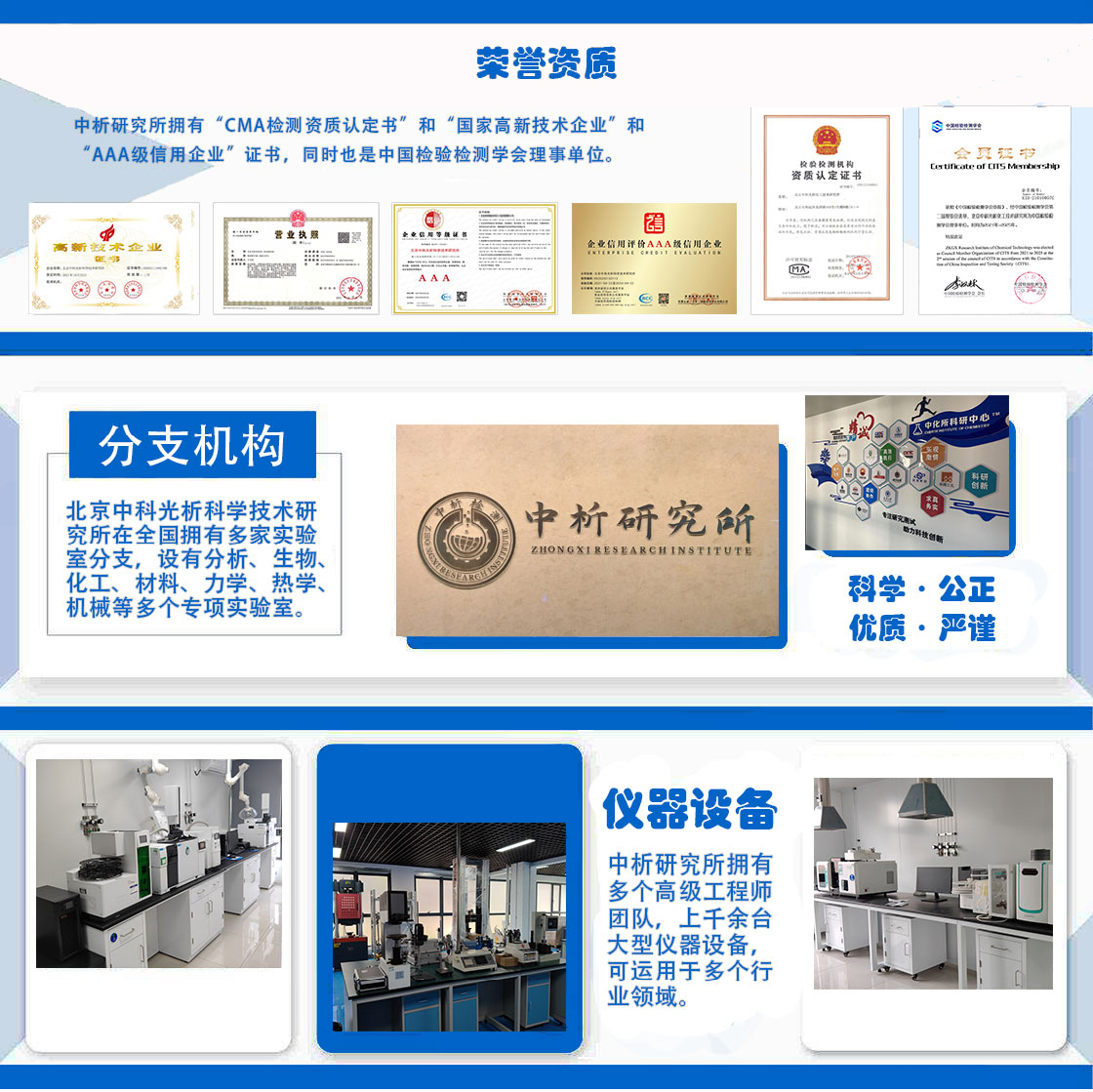
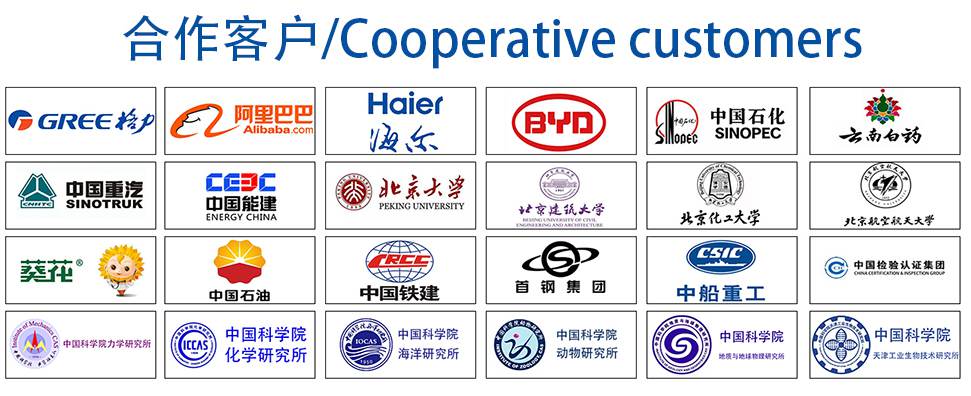