煤矿气体检测用氧气元件检测的重要性与技术要求
在煤矿安全生产中,氧气浓度检测是保障作业人员生命安全的核心环节。煤矿井下环境复杂,氧气含量直接影响人员生存条件和设备运行安全。氧气检测元件作为气体监测系统的"感知器官",其性能直接关系到预警的及时性与准确性。据统计,30%的煤矿气体事故与传感器失效相关,因此针对氧气元件的定期检测与校准已成为行业强制性规范要求。
氧气检测元件的核心检测项目
1. 传感器准确性检测:通过标准气体(如20.9% O₂氮氧混合气)进行标定测试,要求示值误差不超过±0.5%VOL。采用三通阀连接检测装置,对比传感器输出信号与标准值的偏差率。
2. 零点漂移与量程稳定性测试:在洁净空气中连续运行48小时,记录初始值和终止值的波动范围。行业标准AQ1029-2019规定,零点漂移量不得超过±2%FS,量程变化率应小于±3%。
3. 响应时间与恢复时间验证:使用动态配气系统模拟浓度突变场景。优质氧气元件应在15秒内达到目标值90%的响应,恢复至基线的时间不超过30秒。
4. 交叉敏感性测试:评估CH₄、CO₂等干扰气体的影响程度。要求10%浓度CH₄干扰下的氧气检测误差不超过±0.3%VOL,确保复杂气体环境中的测量可靠性。
特殊环境适应性检测
针对煤矿井下高温高湿环境,需进行温湿度循环试验:在温度(-20℃~60℃)、湿度(15%~95%RH)范围内进行100次循环测试,检测元件密封性及性能衰减。同时模拟瓦斯突出时的冲击振动(频率10-2000Hz,加速度20g),验证机械结构稳定性。
检测设备与周期管理
专业检测需配备二级标准气体(不确定度≤1%)、恒温恒湿试验箱、数字万用表(精度0.1mV)等设备。根据MT445标准,建议每3个月进行现场校准,每年返厂全面检测。建立元件全寿命周期档案,记录每次检测数据和性能曲线,实现预测性维护。
通过系统化的检测流程管理,可将氧气检测元件的故障率降低75%,有效预防因缺氧或富氧引发的安全事故,为智慧矿山建设提供基础保障。
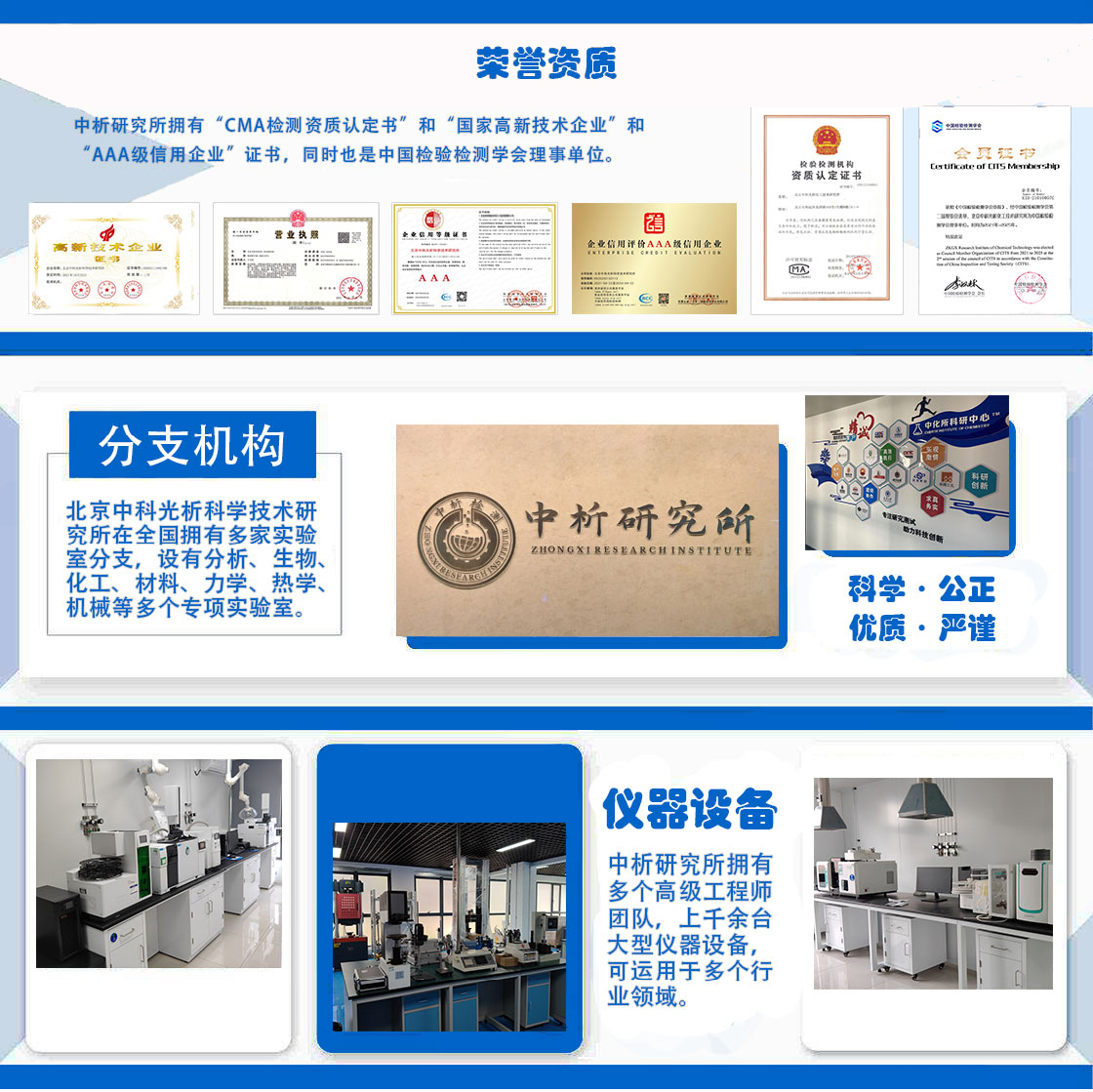
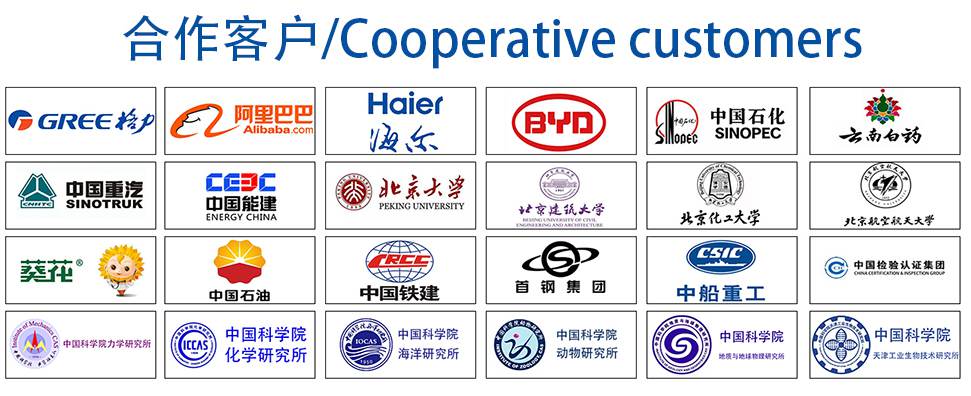