汽车线束和连接器检测的重要性
在现代汽车中,线束和连接器是电气系统的核心组成部分,承担着电力传输、信号控制及数据通信的关键任务。随着汽车智能化、电动化的快速发展,线束的复杂度显著提升,连接器的可靠性直接影响着车辆安全性、功能稳定性及用户体验。据统计,汽车电气系统故障中约40%与线束和连接器相关。因此,通过科学的检测手段确保其质量成为汽车制造和售后维护的核心环节。检测项目需覆盖物理性能、电气特性、环境适应性等多个维度,以全面保障产品在极端工况下的耐久性和功能完整性。
核心检测项目及方法
1. 外观与结构检测
通过目视检查或影像分析设备(如AOI自动光学检测仪)对线束的护套完整性、端子压接状态、连接器插针排列等进行检测。重点核查是否存在磨损、变形、氧化或污染等问题,确保端子与导线的压接强度符合行业标准(如USCAR-21)。
2. 电气性能测试
包括导通性测试、绝缘电阻测试、耐压测试及接触电阻测量。使用高精度万用表和耐压测试仪验证线束的电气连通性,确保绝缘材料在高压(如1500V DC)下无击穿风险,同时通过微欧计检测端子接触电阻(通常要求≤5mΩ),防止因电阻过大导致过热。
3. 机械耐久性试验
模拟车辆使用中的振动、插拔、弯曲等工况。例如: - **振动测试**:依据ISO 16750-3标准,施加5-2000Hz随机振动,持续96小时; - **插拔寿命测试**:对连接器进行5000次以上插拔,监测接触电阻变化; - **线束弯折测试**:评估导线在反复弯曲后的断裂风险,常见标准为LV 214-2。
4. 环境适应性验证
通过高低温循环试验(-40℃至+125℃)、湿热试验(85℃/85%RH)、盐雾试验(如480小时)等模拟极端环境,检测材料老化、密封性和耐腐蚀性。针对新能源车高压线束,还需验证其在浸水、化学液体浸泡后的绝缘性能。
5. 信号完整性测试
针对高速数据传输线束(如CAN FD、以太网线),需使用网络分析仪和示波器检测信号衰减、串扰、阻抗匹配(如100Ω±10%)等参数,确保数据传输速率达到设计要求。
智能化检测趋势
随着工业4.0技术的普及,线束检测正向自动化、数字化发展。例如: - AI视觉系统可实时识别端子压接缺陷; - 在线测试(EOLT)设备实现全流程数据追溯; - 基于大数据的寿命预测模型助力预防性维护。 这些技术大幅提升了检测效率,同时降低了人为误判风险。
结语
汽车线束和连接器的检测体系需兼顾传统可靠性要求与新兴技术挑战,尤其在新能源车和自动驾驶领域,检测标准正不断升级。通过多维度的科学检测,不仅能规避潜在故障风险,更能推动汽车电气系统向更高安全性、智能化方向演进。
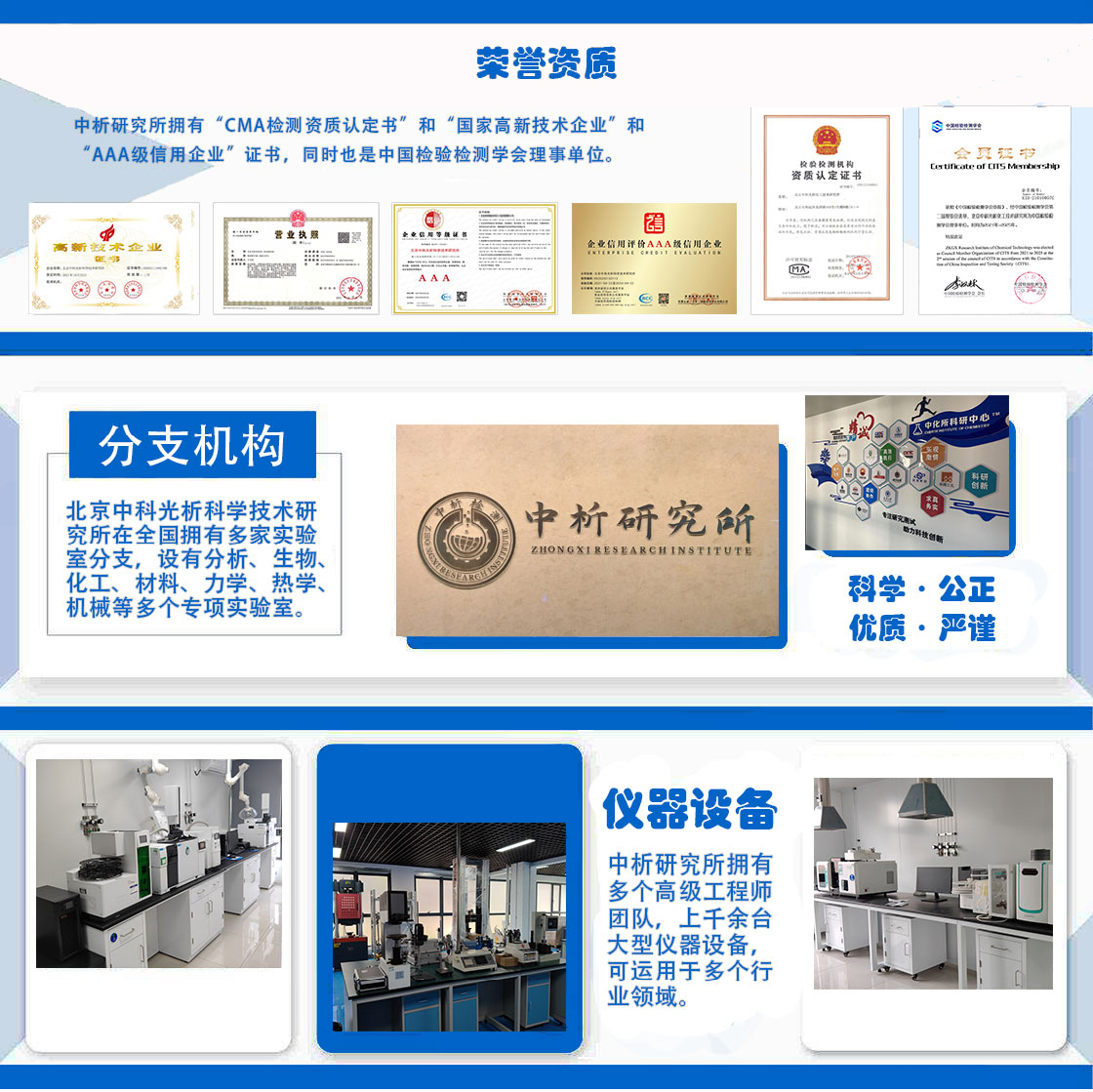
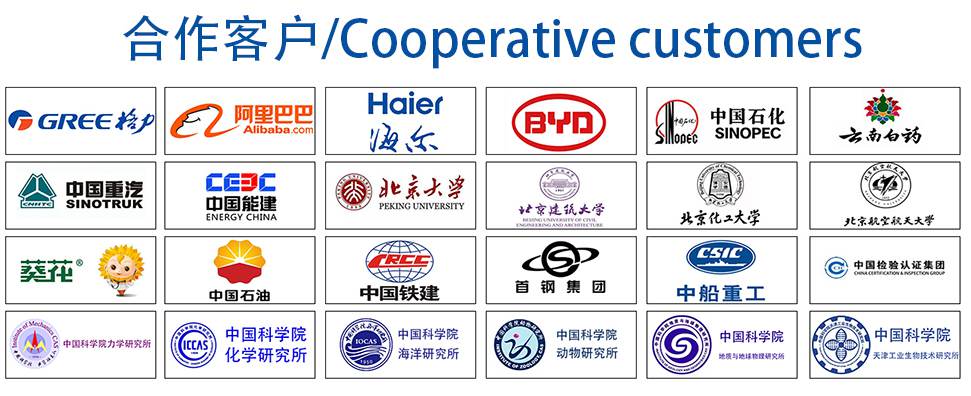