煤矿用电容式发爆器检测技术要点解析
在煤矿安全生产中,电容式发爆器作为爆破作业的核心设备,其性能稳定性直接关系到井下作业的安全性与可靠性。该设备通过存储并释放高能电荷实现精准起爆,而长期处于高湿度、高粉尘的井下环境,可能导致电容老化、绝缘性能下降等问题。因此,按照《GB 7958-2018 煤矿用电容式发爆器》等国家标准要求,实施系统化检测项目,已成为预防哑炮、误爆等事故的关键手段。
一、外观与结构完整性检测
采用目视检查与三维测量结合的方式,重点核查外壳防爆性能、接线端子密封性及机械损伤情况。要求壳体无裂痕变形,防爆接合面间隙≤0.3mm,标识标牌清晰完整,符合MA安全标志认证要求。
二、电容容量及放电性能检测
使用LCR数字电桥测量储能电容容值,偏差不应超出标称值的±10%。通过专用测试台模拟负载,检测放电电压波形上升时间(应<3μs)和峰值电压稳定性,要求连续10次放电能量波动≤5%。
三、绝缘电阻与耐压测试
采用500V兆欧表测量充电回路对地绝缘电阻,新设备应≥100MΩ,在用设备≥50MΩ。工频耐压测试时,充电端子与外壳间施加1500V/1min应无击穿现象。
四、安全保护装置验证
重点测试短路保护响应时间(≤0.1s)、过压保护阈值(标称电压115%±3V)和放电自锁功能。模拟异常工况下,装置应能可靠切断电路并保持闭锁状态。
五、环境适应性试验
在温度-20℃~+60℃、湿度95%RH条件下进行72小时老化测试,检测参数漂移量。振动试验模拟煤矿运输环境,要求3Hz~150Hz扫频振动后功能正常。
六、周期性维护检测规程
根据MT/T 408标准,新设备投入使用前需完成全项目检测,日常使用中每6个月应进行功能性检测,每24个月需返厂进行深度标定。检测数据需同步录入煤矿安全监控系统,实现全生命周期管理。
通过上述系统性检测,可有效识别电容漏液、介质损耗增大等潜在故障。检测中发现电容容量衰减超15%、绝缘电阻持续下降等情况时,应立即停用并更换核心部件。建议煤矿企业建立数字化检测档案,结合物联网技术实现远程状态监测,进一步提升本质安全水平。
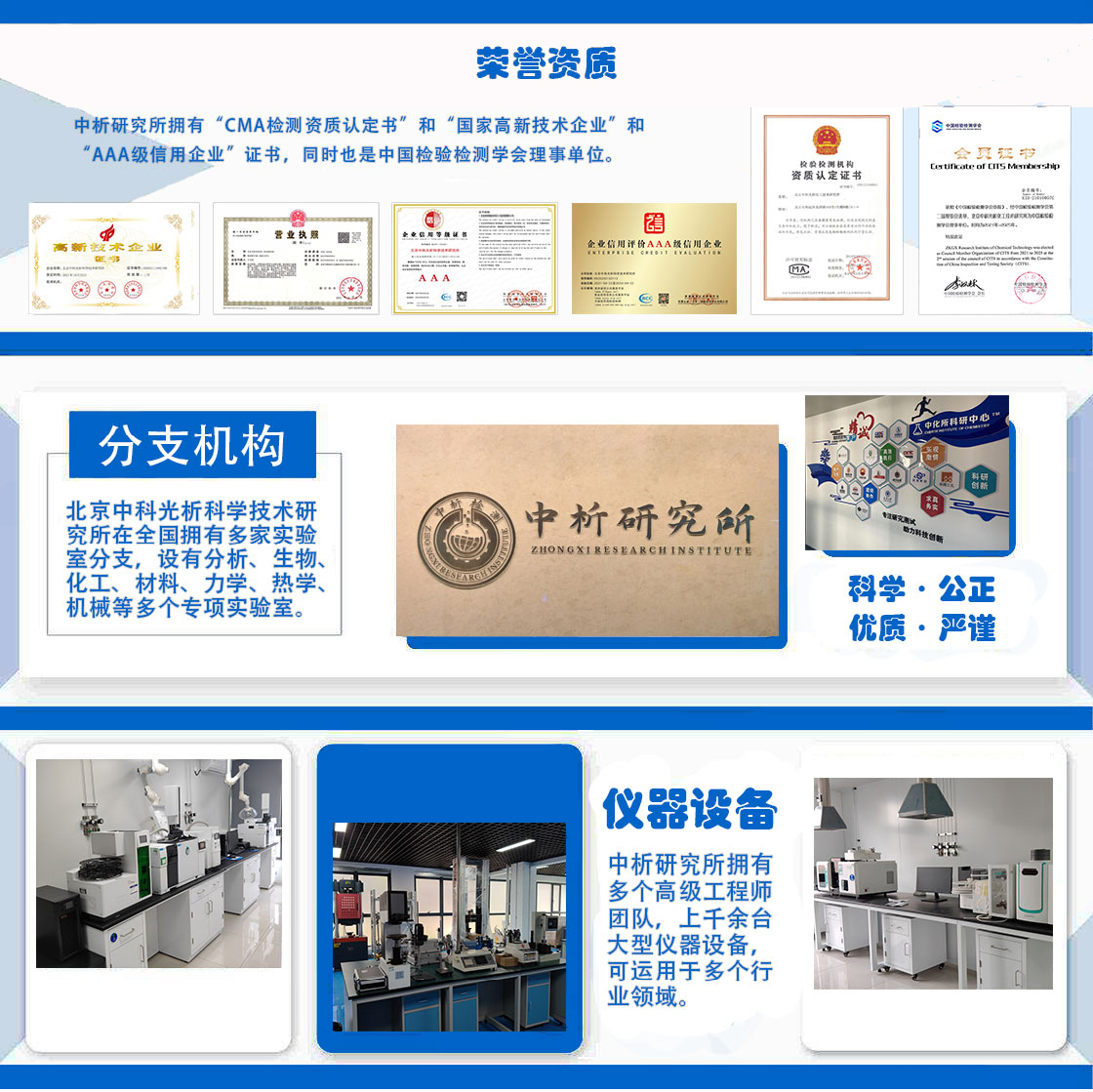
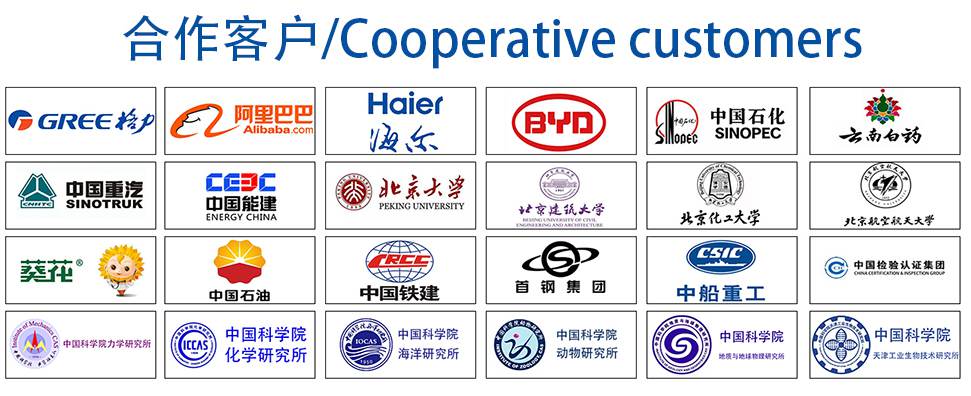