内燃机柴油燃料和汽油过滤器检测的重要性
燃料过滤器是内燃机燃油系统中至关重要的组件,其主要功能是拦截燃油中的颗粒污染物、水分及其他杂质,确保进入发动机的燃料清洁度。对于柴油和汽油发动机而言,过滤器的性能直接影响燃油喷射系统的稳定性、燃烧效率及设备寿命。随着使用时间增加,过滤器可能因堵塞、破损或材料老化导致过滤效率下降,轻则引发功率损失、油耗升高,重则造成喷油嘴堵塞、发动机异常磨损甚至停机故障。因此,定期开展柴油和汽油过滤器的系统性检测,是保障内燃机安全高效运行的必要措施。
核心检测项目与技术要求
1. 外观完整性检查
通过目视和工具测量评估过滤器外壳是否存在变形、锈蚀或泄漏痕迹,密封圈是否弹性良好。使用显微镜观察滤纸褶皱是否均匀,判断是否有机械损伤或局部破损。柴油过滤器需额外关注水分离装置的结构完整性。
2. 过滤效率测试
采用ISO 19438标准规定的多通道颗粒计数法,模拟实际工况向过滤器输入含特定粒径颗粒(如5μm、10μm)的试验燃料,通过上下游颗粒浓度对比计算过滤效率。合格标准通常要求对10μm以上颗粒的截留率≥95%。
3. 压差耐受性验证
在流量测试台架中,逐步提升燃油流量至额定值的1.5倍,监测过滤器进出口压差变化。新过滤器初始压差应低于0.3bar,极限工况下压差增幅不超过20%。柴油过滤器需额外测试低温(-30℃)条件下的流动性表现。
4. 材料兼容性检测
将滤芯浸泡于柴油/汽油与生物燃料混合液(如B20柴油)中500小时,测试滤材抗溶胀、抗水解能力。关键指标包括质量变化率(≤2%)、抗拉强度保留率(≥85%)及纤维结构稳定性。
5. 密封性验证
采用气压试验法,将过滤器浸入水中并施加0.5-0.7bar气压,观察30秒内是否出现连续气泡。柴油过滤器需额外进行水压测试(≥6bar)以验证高压环境下的密封可靠性。
6. 污染物沉积分析
拆解使用后的过滤器,通过光谱仪和电子显微镜对截留污染物进行成分鉴定。柴油过滤器需重点检测硫酸盐灰分和微生物滋生情况,汽油过滤器则需关注胶质物和金属碎屑的积累量。
检测周期与维护建议
建议柴油过滤器每300-500小时或燃油消耗量达1000L时进行检测,汽油过滤器可延长至每800小时检测。若在检测中发现压差超过初始值2倍、过滤效率下降10%以上或存在结构性损伤,应立即更换。同时推荐建立过滤器寿命数据库,结合燃油品质和工况动态调整维护计划。
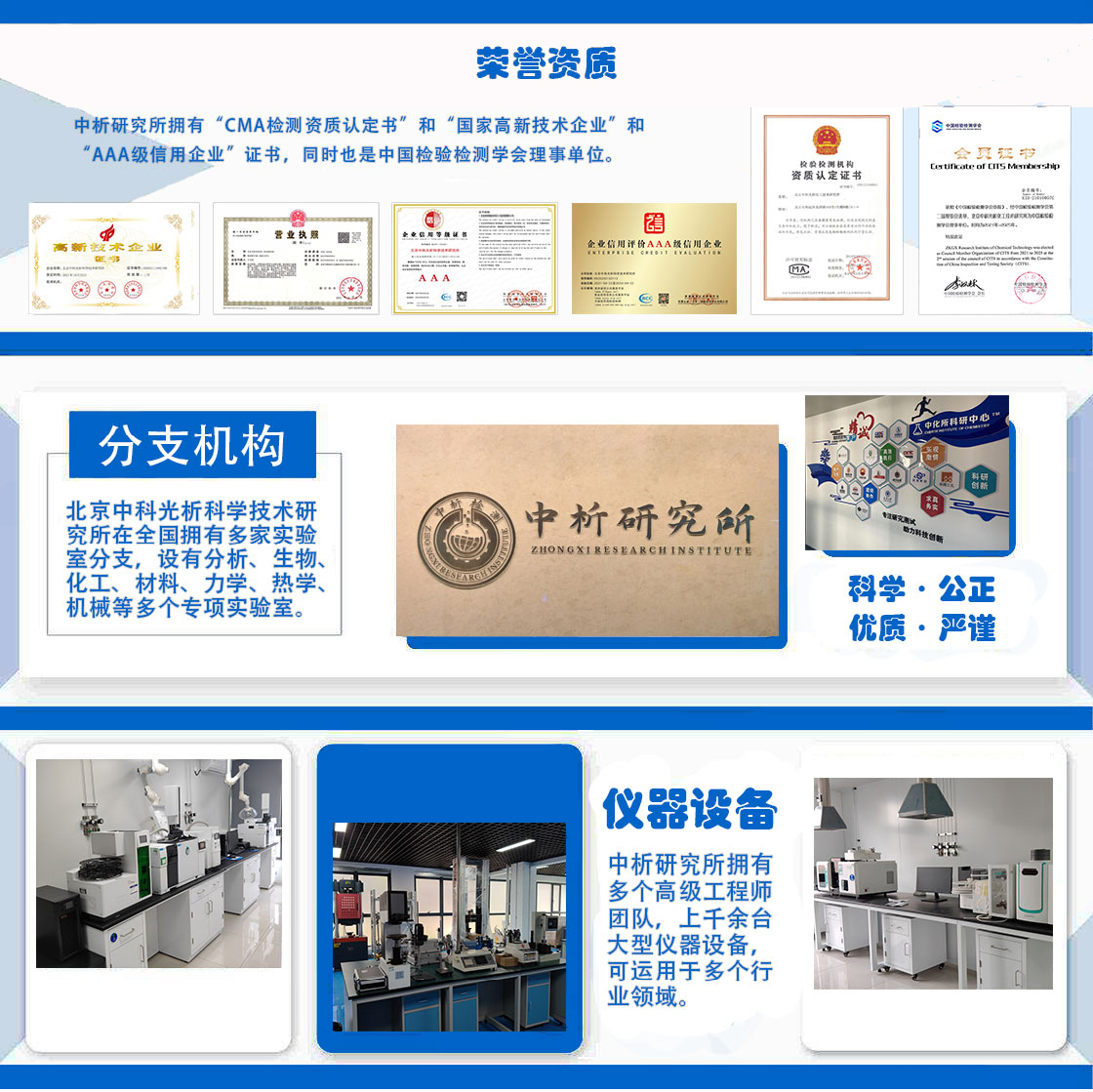
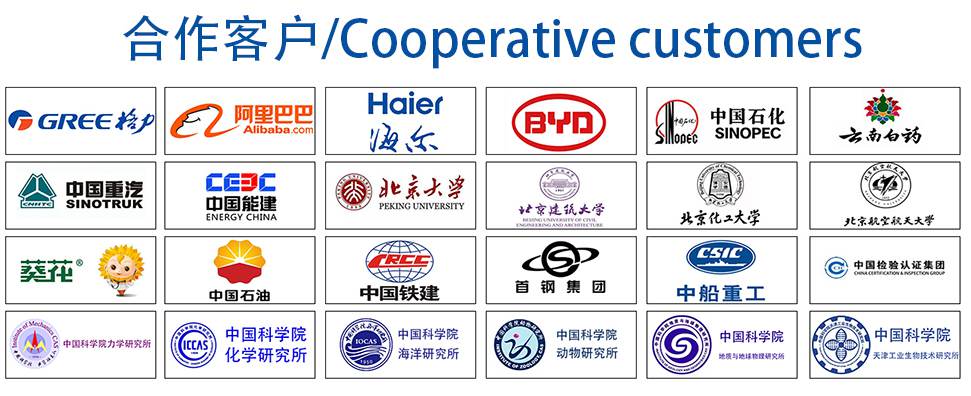