快插式二甲醚汽车加注口检测
实验室拥有众多大型仪器及各类分析检测设备,研究所长期与各大企业、高校和科研院所保持合作伙伴关系,始终以科学研究为首任,以客户为中心,不断提高自身综合检测能力和水平,致力于成为全国科学材料研发领域服务平台。
立即咨询快插式二甲醚汽车加注口检测的必要性与标准
随着清洁能源汽车的快速发展,二甲醚(DME)作为低碳环保替代燃料,在商用车领域的应用日益广泛。快插式二甲醚加注口作为燃料加注系统的核心组件,其性能直接关系车辆安全性和使用效率。由于二甲醚具有强渗透性、易挥发性和对部分材料的腐蚀性,加注口的密封性、耐压性及耐久性需经过严格检测。行业标准要求,此类产品需满足GB/T 34537-2017《车用二甲醚燃料加注口》及QC/T 932-2022《液化石油气/二甲醚汽车专用装置技术条件》等规范,确保在复杂工况下的可靠运行。
核心检测项目及技术要求
1. 密封性能检测
通过氦质谱检漏或压力衰减法测试,在1.5倍工作压力(通常为3.3MPa)下保压3分钟,泄漏率需≤1×10⁻⁶ Pa·m³/s。重点检查O型密封圈与阀芯的配合状态,模拟燃料加注时液态二甲醚的渗透特性。
2. 耐压强度测试
采用液压爆破试验,按工作压力的2.5倍(约5.5MPa)持续加压30秒,结构不得出现塑性变形。爆破压力需≥10MPa,验证材料在极端工况下的机械强度。
3. 材料兼容性试验
将密封件浸泡在纯度≥99.9%的液态二甲醚中(40℃±2℃),经过1000小时老化测试后,体积膨胀率应<15%,硬度变化不超过±5 Shore A。关键考核丁腈橡胶、氟橡胶等材料的耐溶胀特性。
4. 快速插拔寿命测试
在模拟加注频率下进行5000次插拔循环,每次插拔需施加30N·m的轴向扭矩。试验后仍须满足密封等级要求,检测锁止机构的磨损情况及弹簧复位性能。
5. 环境适应性检测
包含高低温交变(-40℃至85℃)、盐雾腐蚀(5%NaCl溶液,480小时)、振动冲击(频率10-2000Hz,加速度30g)等复合环境试验,评估部件在极端气候和路况下的可靠性。
6. 防误操作验证
通过尺寸公差检测(接口公差±0.05mm)和颜色标识检查,确保加注口与柴油/汽油系统不兼容,防止燃料误加事故。需符合ISO 15500-20关于替代燃料接口的防错设计要求。
检测设备与认证要求
检测需使用专用试验台架,包含精密压力控制系统(精度±0.25%FS)、多通道数据采集仪及环境模拟舱。通过 认证的实验室应依据GB/T 34537附录B的试验方法出具检测报告,产品需取得CCC强制性认证及ECER67车载燃料系统认证后方可上市。
行业发展趋势
随着智能网联技术的应用,新一代加注口开始集成RFID识别芯片和压力传感器,检测项目已扩展至电子元件的EMC抗干扰测试(30V/m场强下功能正常)和CAN总线通讯验证。未来检测标准将更注重系统级的兼容性评估,推动行业向智能化、高可靠性方向发展。
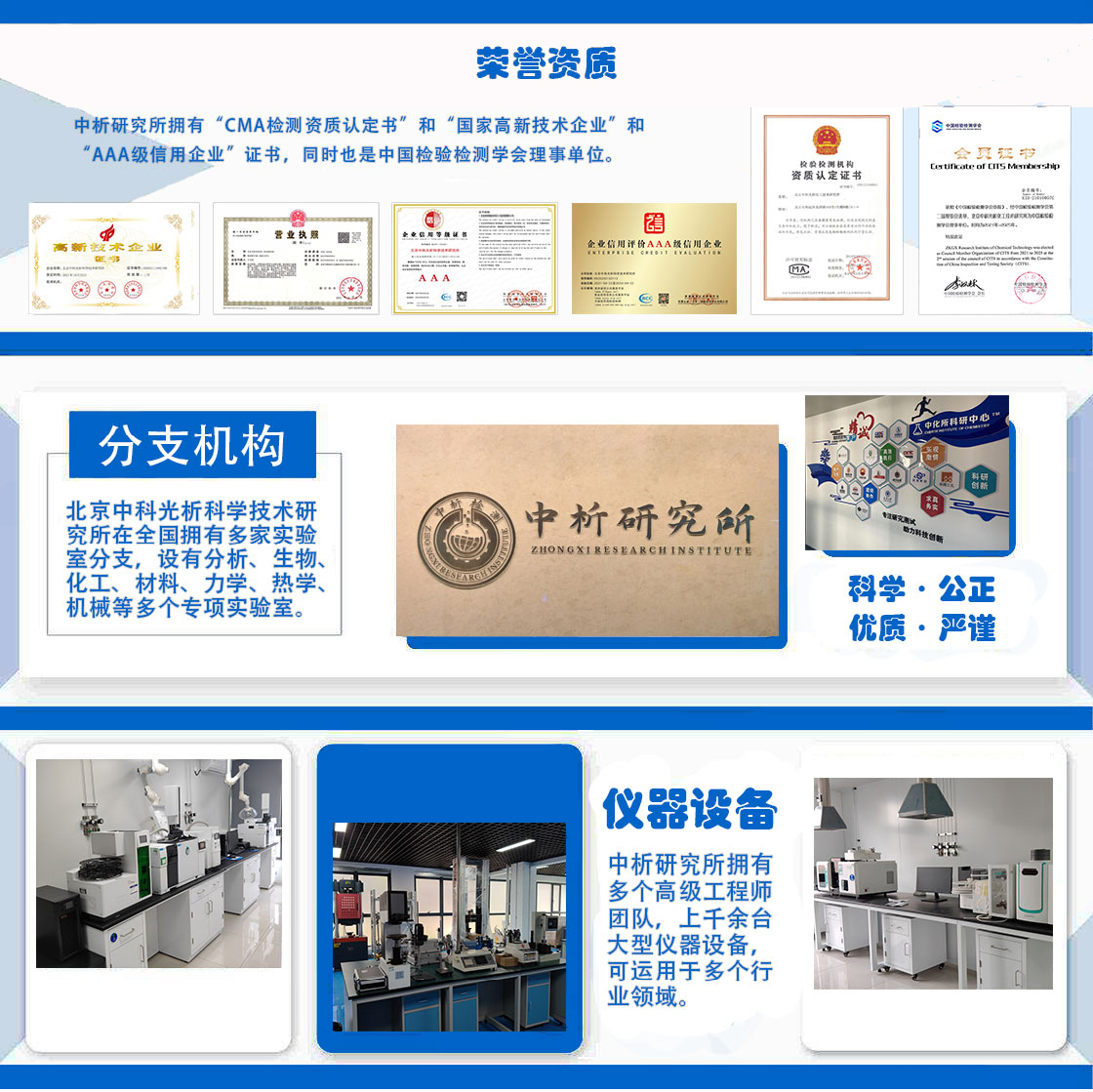
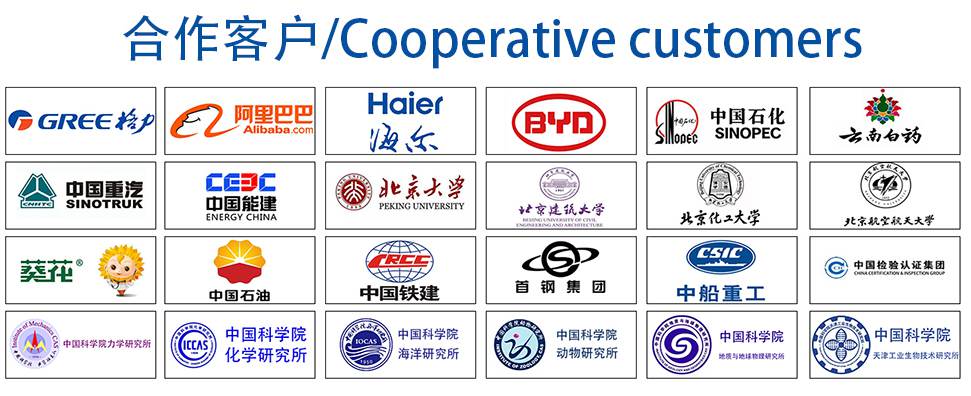