爆炸性环境用工业车辆检测的重要性
在石油化工、矿山、制药、粉尘加工等存在易燃易爆气体或粉尘的工业环境中,特种工业车辆(如防爆叉车、防爆牵引车等)的安全运行直接关系到人员生命和财产安全。由于这类环境对点火源极为敏感,任何微小的机械摩擦、电气火花或设备温升都可能引发灾难性事故。因此,针对爆炸性环境用工业车辆的检测不仅是法规强制要求,更是保障生产安全的核心环节。检测需覆盖车辆结构设计、电气系统、机械组件及动态运行状态,确保其满足国际标准(如IEC 60079系列、ATEX指令)和国内标准(如GB 3836),同时需通过周期性复检实现全生命周期管理。
核心检测项目及技术要求
1. 防爆结构完整性认证
检测车辆防爆结构类型(如隔爆型、增安型、本质安全型)是否符合设计规范,包括外壳强度、接合面间隙、紧固件扭矩等。例如,隔爆型设备需通过1.5倍最大爆炸压力测试,确保外壳能有效抑制内部爆炸扩散。
2. 电气系统防爆性能检测
对电机、控制器、电缆及接线盒进行Ex防爆认证验证,检测内容包括:
- 电气间隙与爬电距离是否符合防爆等级(如IIA/IIB/IIC)要求
- 本安电路的能量限制测试
- 电缆引入装置的密封性试验
3. 机械部件火花抑制测试
评估制动系统、传动装置等运动部件在极端工况下的火花风险:
- 使用非铁质材料(如铜基合金)验证摩擦副的防爆性能
- 模拟负载条件下检测制动鼓温升(需≤设备组别T4-T6限值)
- 液压系统防泄漏及抗冲击试验
4. 气体与粉尘防渗透检测
通过压力衰减法测试车辆密闭舱室的密封性,确保可燃气体或粉尘无法侵入电气仓。同时验证呼吸装置、排水阀等特殊设计的有效性。
5. 静电防护与接地连续性测试
测量整车接地电阻(要求≤1Ω),检查轮胎、货叉等部位的导电性能。对非金属部件进行表面电阻测试(需≤1×10^9Ω),避免静电积聚。
6. 动态运行安全评估
在模拟爆炸性环境中进行实载运行试验,监测:
- 紧急制动时的机械火花产生概率
- 电池组在冲击振动下的安全性能
- 车载监控系统(如温度、气体浓度传感器)的响应精度
7. 定期维护与复检机制
建立基于风险的检测周期(通常为12-24个月),重点复查防爆标志清晰度、紧固件状态、保护装置功能等。对改造或维修后的车辆需重新进行整体防爆认证。
通过上述系统性检测,可确保工业车辆在爆炸性环境中实现“本质安全”,最大限度降低因设备缺陷导致的爆炸风险,为高危行业提供可靠的技术保障。
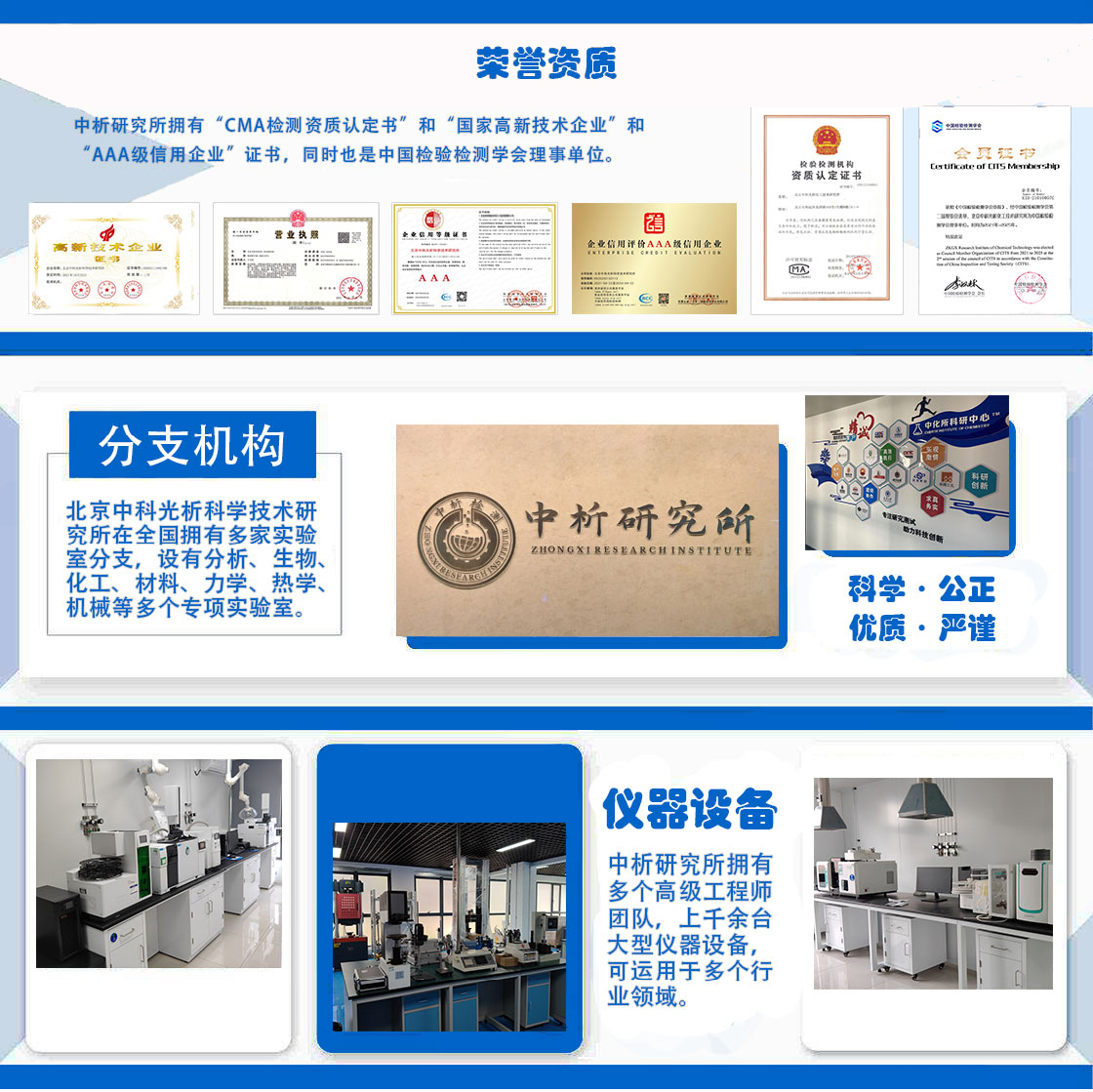
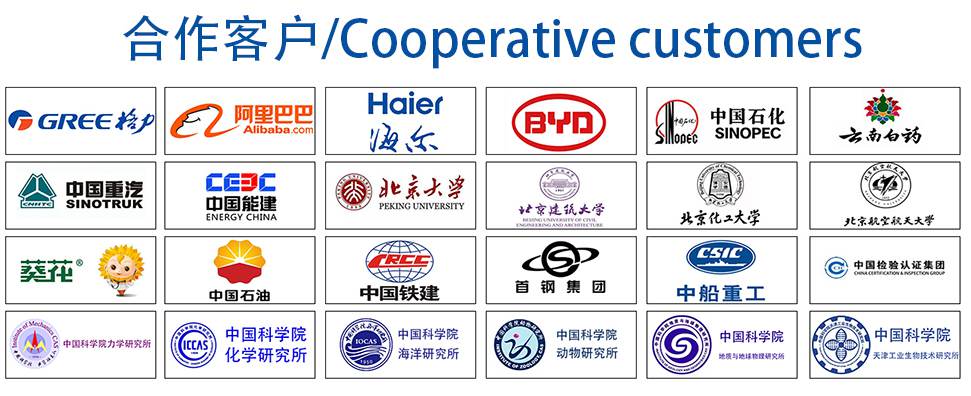