铝合金焊接检测的重要性与检测项目解析
铝合金因其轻量化、高强度、耐腐蚀等特性,广泛应用于航空航天、轨道交通、汽车制造及建筑领域。焊接作为铝合金结构件的主要连接方式,其质量直接影响产品的安全性和使用寿命。然而,铝合金的导热性强、氧化倾向高、热膨胀系数大等特点,容易导致焊接过程中产生气孔、裂纹、未熔合等缺陷。因此,铝合金焊接的质量检测是确保工程可靠性的核心环节。通过科学规范的检测手段,能够精准识别焊接缺陷,优化工艺参数,最终提升产品的综合性能。
铝合金焊接检测的主要项目
1. 外观检查
通过目视或低倍放大镜检查焊缝表面质量,主要观察焊缝成形是否连续均匀,是否存在咬边、焊瘤、表面裂纹等缺陷。根据ISO 10042标准,焊缝表面需无可见污染物及明显凹凸不平,余高应符合设计要求。
2. 无损检测(NDT)
- X射线检测(RT):适用于检测内部气孔、夹渣等体积型缺陷,对厚板焊接效果显著;
- 超声波检测(UT):可识别焊缝内部裂纹和未熔合,尤其擅长检测面状缺陷;
- 渗透检测(PT):用于发现表面开放性裂纹,需配合荧光或着色剂使用;
- 涡流检测(ET):适用于薄壁管材或导电性材料的近表面缺陷检测。
3. 力学性能测试
通过拉伸试验、弯曲试验和硬度测试评估焊接接头强度:
- 拉伸试验需满足AWS D1.2标准要求,抗拉强度不低于母材的90%;
- 弯曲试验检测接头的塑性变形能力,试样弯曲180°后不得出现裂纹;
- 维氏硬度测试用于分析热影响区软化现象。
4. 化学成分分析
使用光谱分析仪检测焊缝金属的合金元素含量,防止因焊材选用不当或稀释作用导致成分偏差。重点监控Mg、Si等主要合金元素的波动范围,确保符合GB/T 3190或AMS规范要求。
5. 金相检验
通过显微镜观察焊缝显微组织,评估晶粒度、第二相分布及热影响区宽度。典型缺陷如焊接裂纹、气孔的金相形貌有助于追溯工艺问题,例如过快的冷却速度可能引发热裂纹。
6. 气密性检测
针对压力容器或真空设备,采用氦质谱检漏、水压试验或气压试验验证焊缝的密封性。根据ASME BPVC标准,泄漏率需低于10^-5 Pa·m³/s量级。
7. 焊接工艺评定(WPS/PQR)
通过工艺验证试验确认焊接参数(电流、电压、焊速等)的合理性,确保重复生产的稳定性。需按照NB/T 47014标准进行全项目测试,并形成完整的工艺评定报告。
检测流程的优化建议
建议采用多阶段联合检测策略:焊前进行焊材认证和坡口清洁度检查,焊中实施层间温度监控,焊后按照“外观→无损→破坏性试验”的优先级开展检测。对于航空航天等高要求场景,可引入工业CT实现三维缺陷重构,结合AI算法提升检测效率。
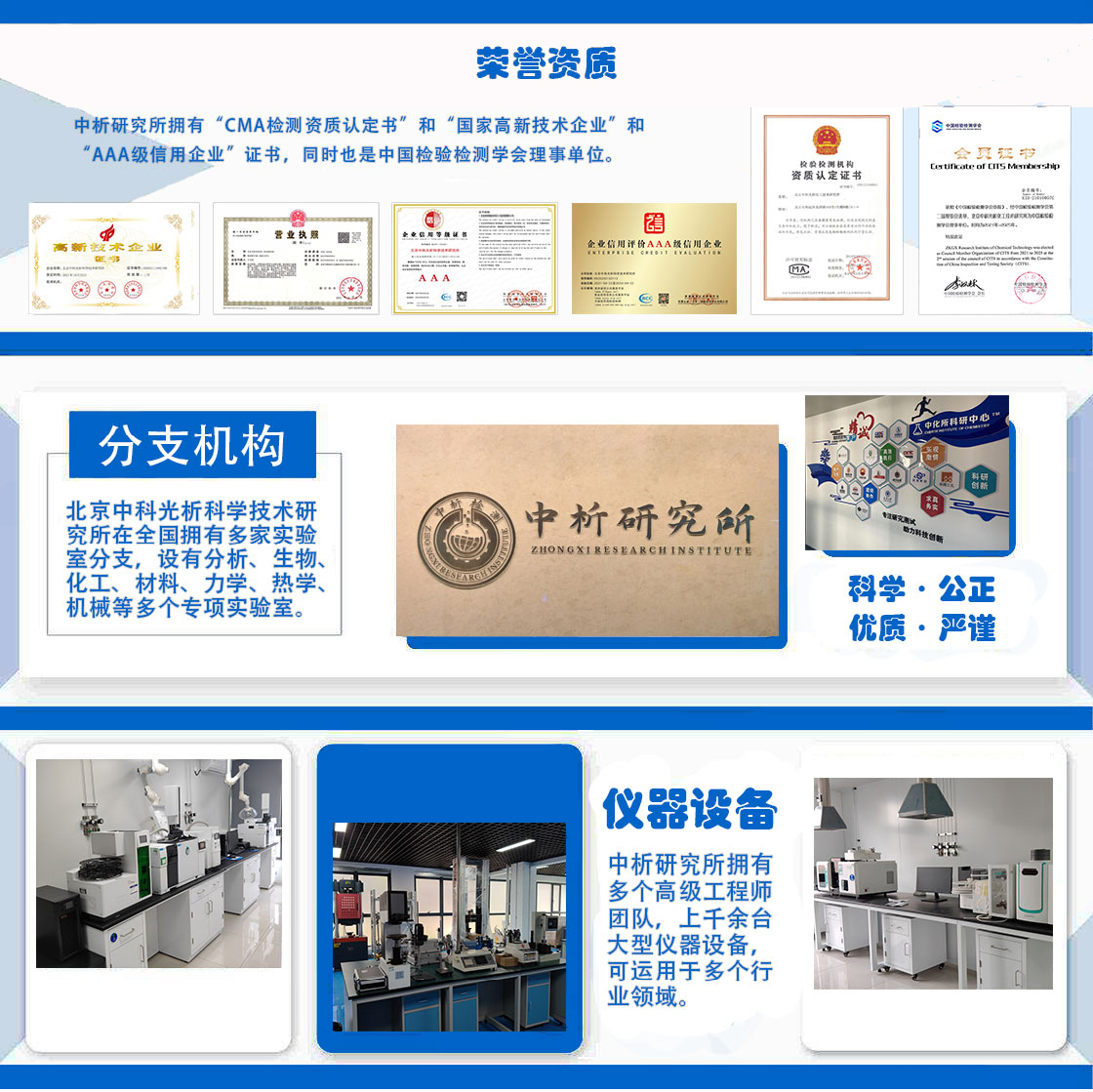
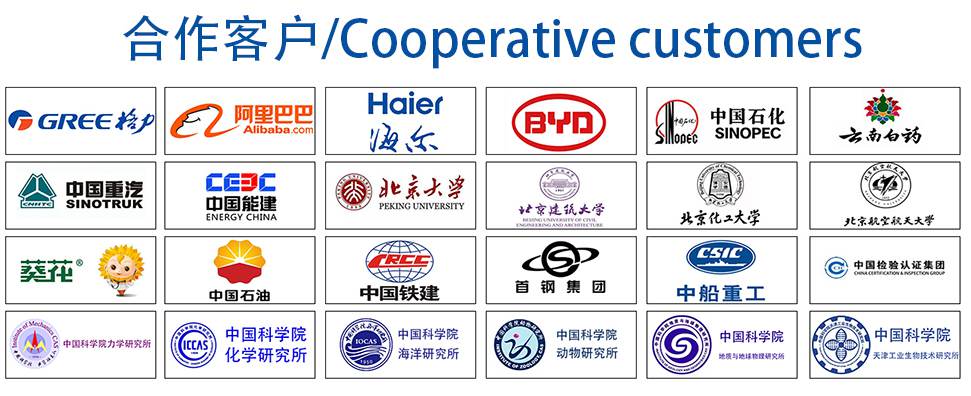