锅炉和压力容器用钢板检测的重要性
锅炉和压力容器作为工业生产和能源领域的核心设备,其安全性直接关系到人员生命、环境安全及生产连续性。钢板作为制造这类设备的主要材料,需在高温、高压、腐蚀等极端工况下长期稳定运行,因此其质量检测至关重要。通过对锅炉和压力容器用钢板进行系统化、标准化的检测,可以有效避免材料缺陷导致的结构失效、泄漏甚至爆炸等事故,同时确保设备符合国家标准(如GB 713-2014)及国际规范(如ASME SA-515/SA-516)。
主要检测项目及技术要点
1. 化学成分分析
钢板的化学成分直接影响其力学性能和耐腐蚀性。检测时需通过光谱分析仪、碳硫分析仪等设备,精确测定碳(C)、锰(Mn)、硅(Si)、硫(S)、磷(P)等元素含量,确保符合材料牌号要求。例如,硫、磷含量过高会导致材料脆性增加,降低抗冲击能力。
2. 力学性能测试
包括拉伸试验、冲击试验和弯曲试验:
- 拉伸试验:测定抗拉强度、屈服强度和延伸率,验证钢板在载荷下的变形能力;
- 冲击试验:采用夏比V型缺口试样,评估低温环境下的韧性;
- 弯曲试验:检测钢板在塑性变形时的表面裂纹敏感性。
3. 无损检测(NDT)
通过超声波检测(UT)、磁粉检测(MT)和渗透检测(PT)等技术:
- 超声波检测:发现内部夹杂、分层等缺陷;
- 磁粉/渗透检测:识别表面及近表面裂纹、气孔等缺陷,灵敏度需达到标准要求。
4. 尺寸与外观检查
测量钢板厚度、宽度、平直度等几何参数,确保加工精度;同时检查表面氧化皮、划痕、结疤等表观缺陷,避免应力集中区域的形成。
5. 高温性能与耐腐蚀性测试
模拟实际工况进行高温拉伸试验,评估材料在长期高温下的强度衰减情况;通过盐雾试验、晶间腐蚀试验等,验证钢板在特定介质环境中的耐蚀能力。
6. 金相组织分析
利用金相显微镜观察钢板微观结构(如铁素体、珠光体比例),分析晶粒度级别,判断热处理工艺是否达标,避免因组织异常导致性能下降。
结语
锅炉和压力容器用钢板的检测需贯穿原材料采购、生产加工及成品验收全流程,结合第三方认证与过程质量控制,才能从根本上保障设备的安全性和使用寿命。随着智能检测技术的发展,如自动超声波成像(AUT)和数字化金相分析的应用,检测效率和精度将进一步提升。
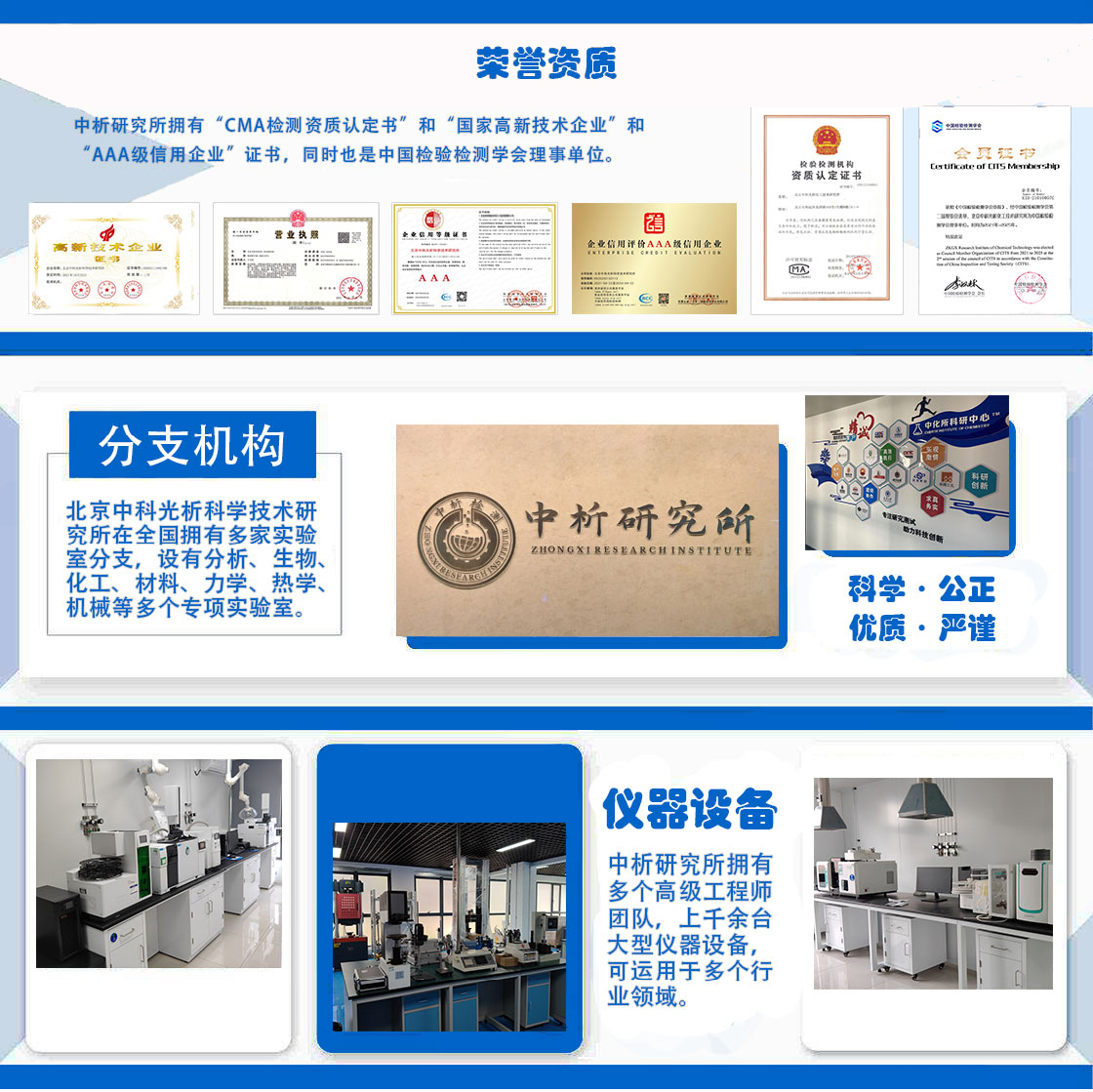
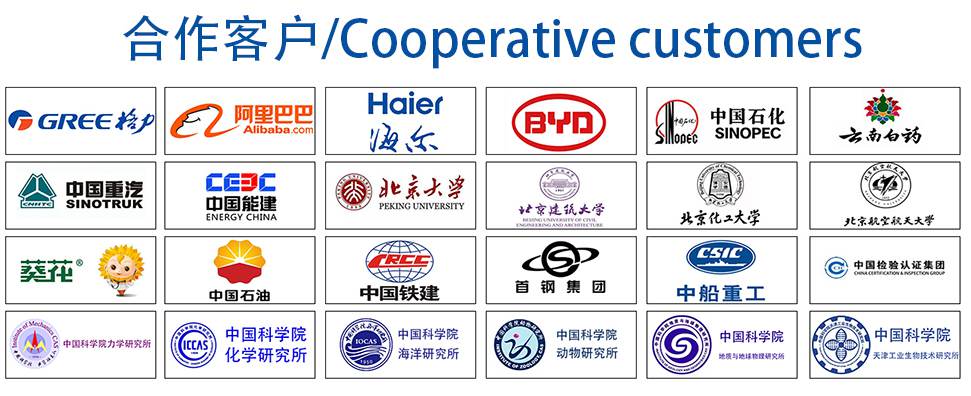