轮胎压路机检测的重要性与必要性
轮胎压路机作为道路施工中的核心压实设备,其性能稳定性直接影响工程质量和施工安全。随着使用时间的增加,设备的机械磨损、轮胎老化、液压系统故障等问题会逐渐显现,可能导致压实效果下降甚至安全事故。因此,定期开展轮胎压路机检测是保障设备高效运行、延长使用寿命的关键环节。通过系统性检测,不仅能发现潜在隐患,还能优化设备维护策略,减少非计划停机时间,显著提升施工效率并降低运营成本。
轮胎压路机主要检测项目
1. 外观与结构完整性检测
包括机体框架、配重块、轮胎支架等部件的目视检查,重点排查结构变形、裂纹、锈蚀等问题。需使用测量工具对关键部位间隙进行校准,如轮胎间距偏差应控制在±5mm以内,确保压实均匀性。
2. 轮胎系统专项检测
作为核心工作单元,需检查轮胎气压(标准值0.8-1.2MPa)、胎面磨损程度(沟槽深度≥3mm)、轮胎对中度(误差≤2%)。同时通过载荷测试验证各轮胎接地压力均匀性,避免出现单胎过载现象。
3. 液压系统性能测试
采用压力表检测液压泵输出压力(通常为16-20MPa),检查油缸升降速度和平稳性。同步监测液压油温(工作温度≤80℃)及油液污染度(NAS等级不超过8级),发现异常需立即更换滤芯或液压油。
4. 制动与转向系统验证
通过坡道驻车试验(坡度≥15%)验证驻车制动性能,行车制动距离测试要求20km/h时速下≤5m。转向系统需检查方向盘自由行程(≤15°)和转向油缸同步精度,确保操控灵敏度和安全性。
5. 振动压实系统分析
使用振动测试仪检测激振频率(常规范围25-40Hz)和振幅(1.5-2.0mm),验证偏心块配重是否符合设计要求。同时监测轴承温升(工作温度≤70℃)及异常噪音,防止振动系统失稳导致设备损坏。
6. 电气与安全装置检测
检查照明系统、仪表盘、紧急停机按钮等功能完整性,测试电路绝缘电阻(≥1MΩ)。安全装置重点验证驾驶室ROPS/FOPS防护结构强度,以及声光报警装置灵敏度,确保符合GB25684标准要求。
检测周期与结果应用
建议每500工作小时或季度进行常规检测,累计运行2000小时后需开展全面性能评估。检测数据应建立电子档案,通过趋势分析预测关键部件寿命,制定预防性维护计划。对于检测不合格项,需依据缺陷等级采取停机维修、部件更换或系统改造等纠正措施,经复检合格后方可重新投入施工。
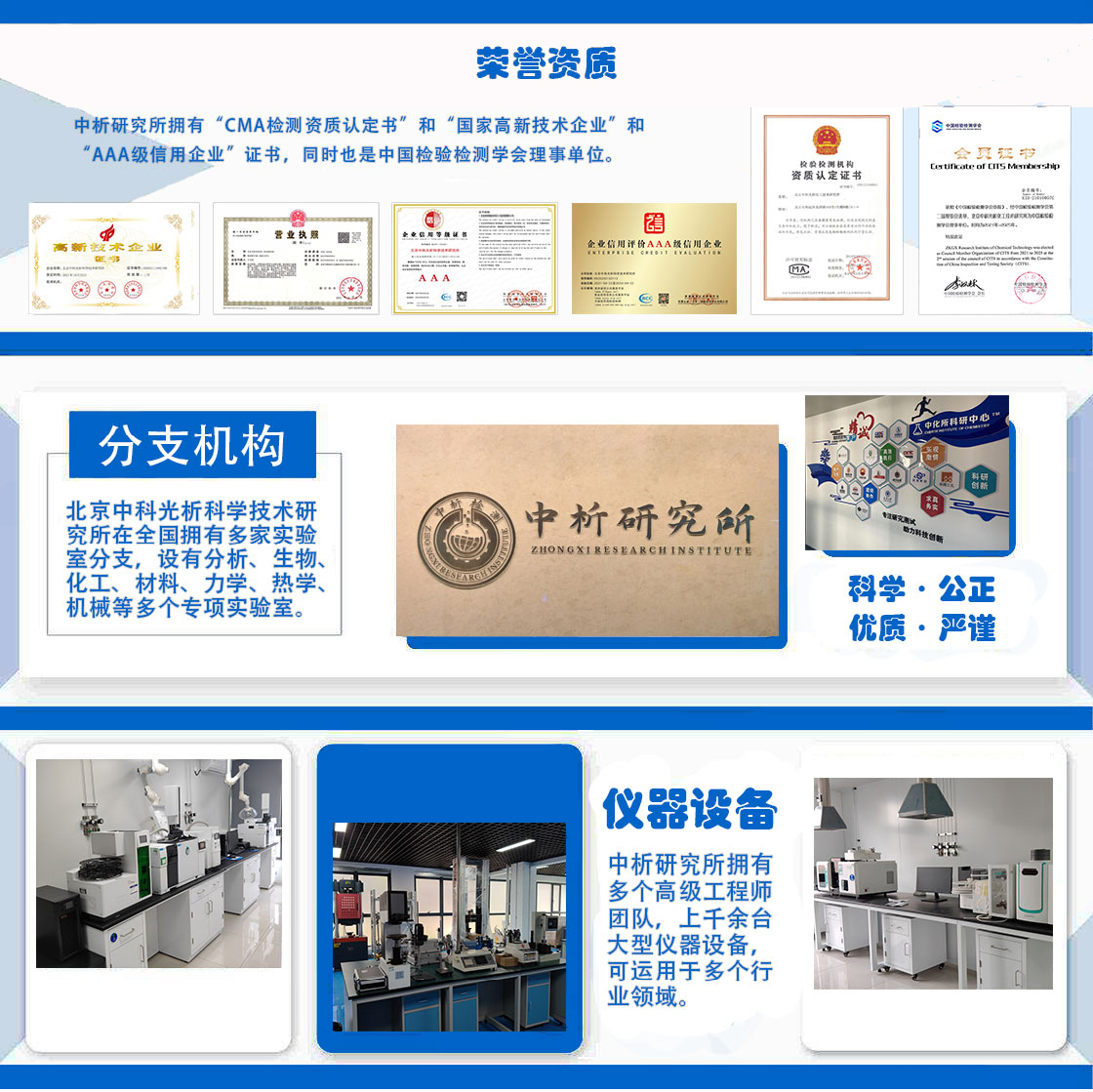
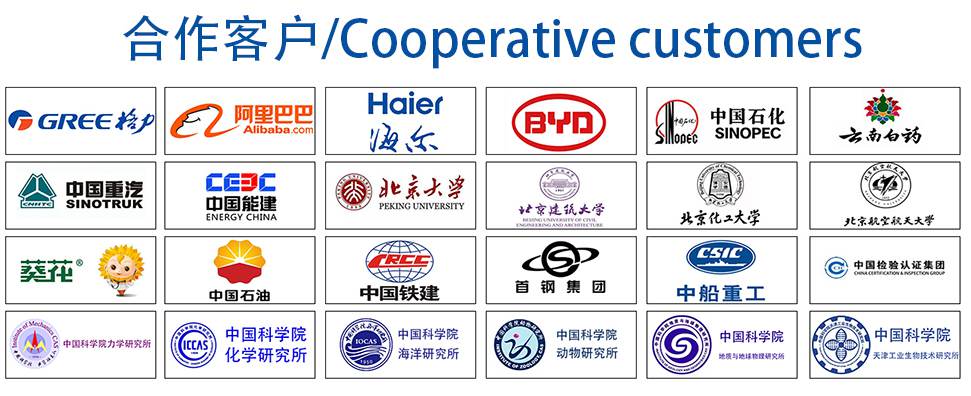