试验机检测概述
试验机检测是工业生产和科研领域中不可或缺的重要环节,主要用于评估材料、零部件或整机的力学性能、耐久性及可靠性。通过模拟实际工况中的载荷、温度、振动等条件,试验机能够精准检测产品的抗拉强度、压缩性能、疲劳寿命等关键指标,广泛应用于机械制造、建筑工程、航空航天、汽车制造等行业。随着技术进步和行业标准升级,试验机检测的精度和覆盖范围持续提升,成为保障产品质量、优化设计、降低安全风险的核心手段。
试验机检测的核心项目
1. 静态性能测试
静态性能测试是试验机检测的基础项目,主要包含拉伸试验、压缩试验和弯曲试验。通过施加恒定或渐变载荷,记录试样的变形量、应力-应变曲线及断裂点,分析材料的弹性模量、屈服强度、抗拉强度等参数。例如,在金属材料检测中,拉伸试验可明确其延展性和承载能力。
2. 动态性能测试
动态性能测试模拟周期性或冲击载荷对试样的影响,包括疲劳试验、冲击试验和振动试验。疲劳试验通过循环加载预测材料或结构的寿命,冲击试验则评估其在瞬时载荷下的抗破坏能力,此类测试对汽车零部件、桥梁构件等长期受动态载荷的产品尤为重要。
3. 环境适应性测试
针对高温、低温、湿度、盐雾等复杂环境条件,试验机需结合环境箱进行综合检测。例如,在航空航天领域,材料需在-60℃至150℃范围内验证性能稳定性;电子元件则需通过湿热试验评估耐腐蚀性。
4. 安全保护功能验证
试验机的安全保护系统检测包括过载保护、紧急停机、位移限位等功能验证。通过模拟异常工况(如载荷超限或传感器故障),确保设备能及时响应并切断动力,避免试样损坏或人员伤害。
5. 精度校准与计量认证
试验机的力值、位移、速度等测量系统需定期进行计量校准,以确保数据准确性。检测机构依据ISO 7500、JJG 139等标准,采用标准测力仪和位移传感器对设备进行误差分析,确保其满足国家或行业计量要求。
试验机检测的意义与挑战
通过系统化的试验机检测,企业能够提前发现产品缺陷、优化设计方案并缩短研发周期。然而,随着新材料(如复合材料、3D打印部件)的涌现,试验机需适应更高频率、更复杂的测试需求,这对设备智能化、数据分析能力提出了更高要求。未来,集成AI算法的试验机系统或将成为行业突破的关键方向。
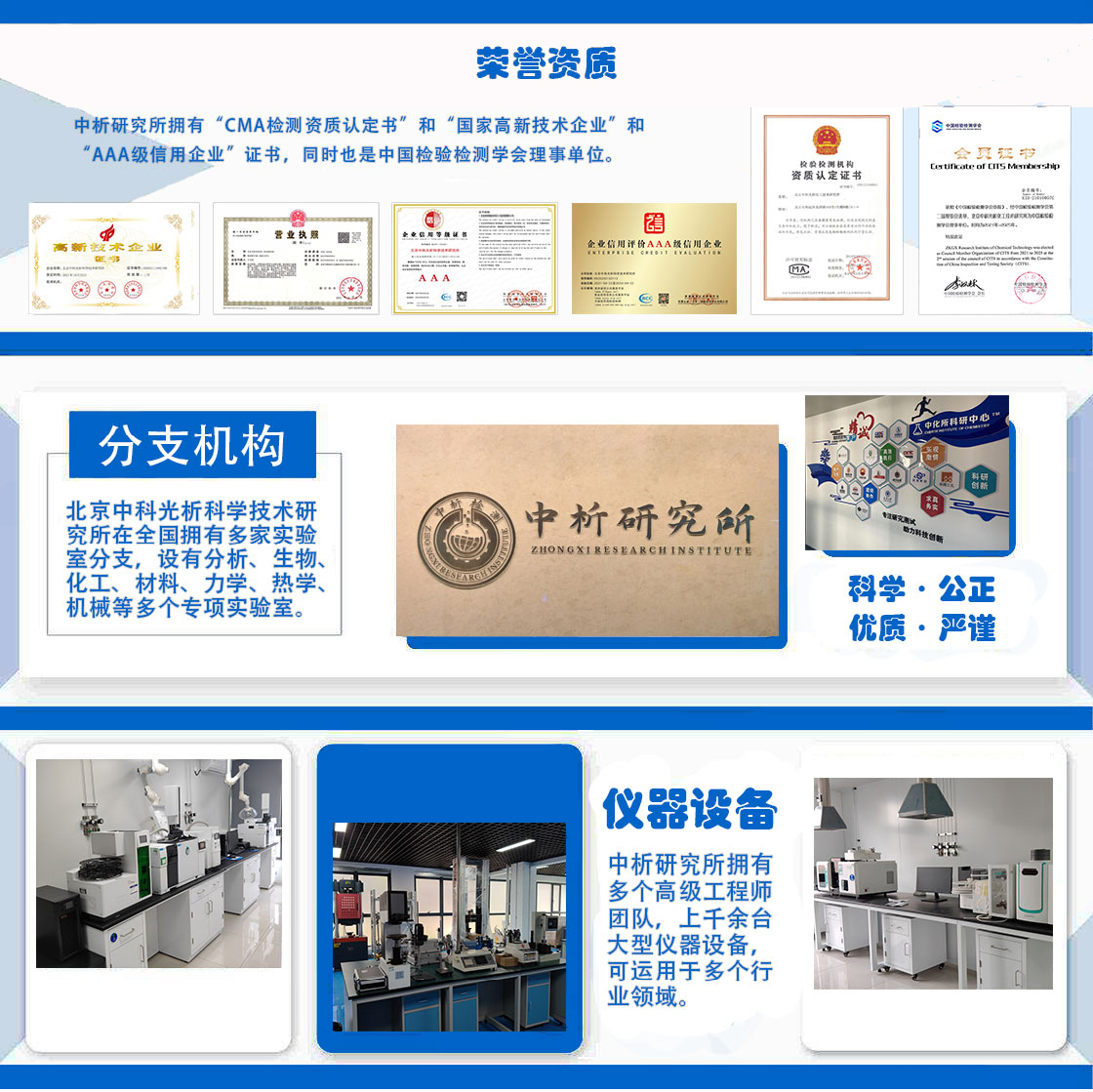
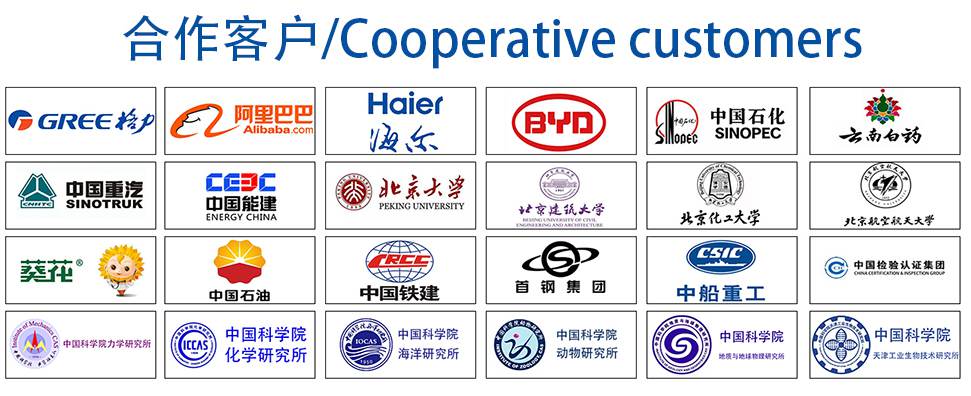