内部接线和连接测试检测的重要性
内部接线和连接测试是电气设备、电子产品和系统集成领域中的基础性质量保障环节,其核心目标是确保设备内部线路连接的正确性、安全性与可靠性。在现代工业制造中,随着设备复杂度提升和微型化趋势加剧,任何微小的接线错误或连接不良都可能导致设备性能下降、功能失效,甚至引发短路、过热、火灾等安全隐患。因此,通过系统化的检测手段对内部接线的绝缘性能、导通状态、机械强度及耐久性进行全面验证,成为保障产品出厂质量、延长使用寿命和降低售后风险的必要措施。
核心检测项目分类
在内部接线和连接测试中,需围绕以下几大关键项目展开:
1. 外观与物理结构检查:通过目视或光学设备检查导线颜色、线径是否符合设计要求,端子压接是否牢固,焊点是否存在虚焊、漏焊或氧化现象,确保无裸露导体或绝缘层破损。
2. 导通性测试:使用万用表或专用导通测试仪验证线路通断状态,确认信号传输路径的完整性,排除断路、错接或交叉短路问题。
3. 绝缘电阻测试:施加直流高压(通常500V-1000V)测量导线间及导线对地的绝缘电阻值,判断是否符合IEC 60664等标准要求,预防漏电风险。
4. 耐压强度测试:模拟极端电压条件(如AC 1500V/60s)检测绝缘材料的耐击穿能力,确保设备在突发过压情况下仍能安全运行。
5. 连接器插拔力与耐久性测试:通过机械拉力计和插拔寿命试验机评估接插件在反复使用后的接触稳定性,防止因插拔磨损导致接触电阻升高。
常见问题与隐患识别
在实际检测中,高频发现的问题包括:线缆弯曲半径过小导致屏蔽层断裂、多股线芯分叉造成局部短路风险、高温环境下绝缘材料变形引发的导体接触,以及振动环境中螺丝端子松动引起的间歇性断路。这些问题若未被及时检出,可能引发设备间歇性故障、电磁干扰超标或电气火灾等严重后果。
检测实施方法与标准遵循
现代检测流程通常结合自动化测试设备(ATE)与人工复检,例如使用可编程电源配合数据采集卡实现多通道并行测试。标准体系方面需严格参照GB 4943.1(信息技术设备安全)、IEC 60950(通信设备安全)或车辆电子领域的ISO 16750等规范,同时根据应用场景叠加UL、CE等认证要求。对于高可靠性领域(如航空航天),还需引入X射线检测、红外热成像等非破坏性检测技术。
总结与建议
内部接线和连接测试贯穿于产品研发、生产及维护全周期,企业应建立多维度的检测方案:在设计阶段通过DFMEA分析潜在风险点,生产阶段采用SPC统计过程控制,并在售后阶段通过定期维护检测预防老化故障。只有将标准化检测流程与技术创新相结合,才能有效提升产品市场竞争力并降低全生命周期质量成本。
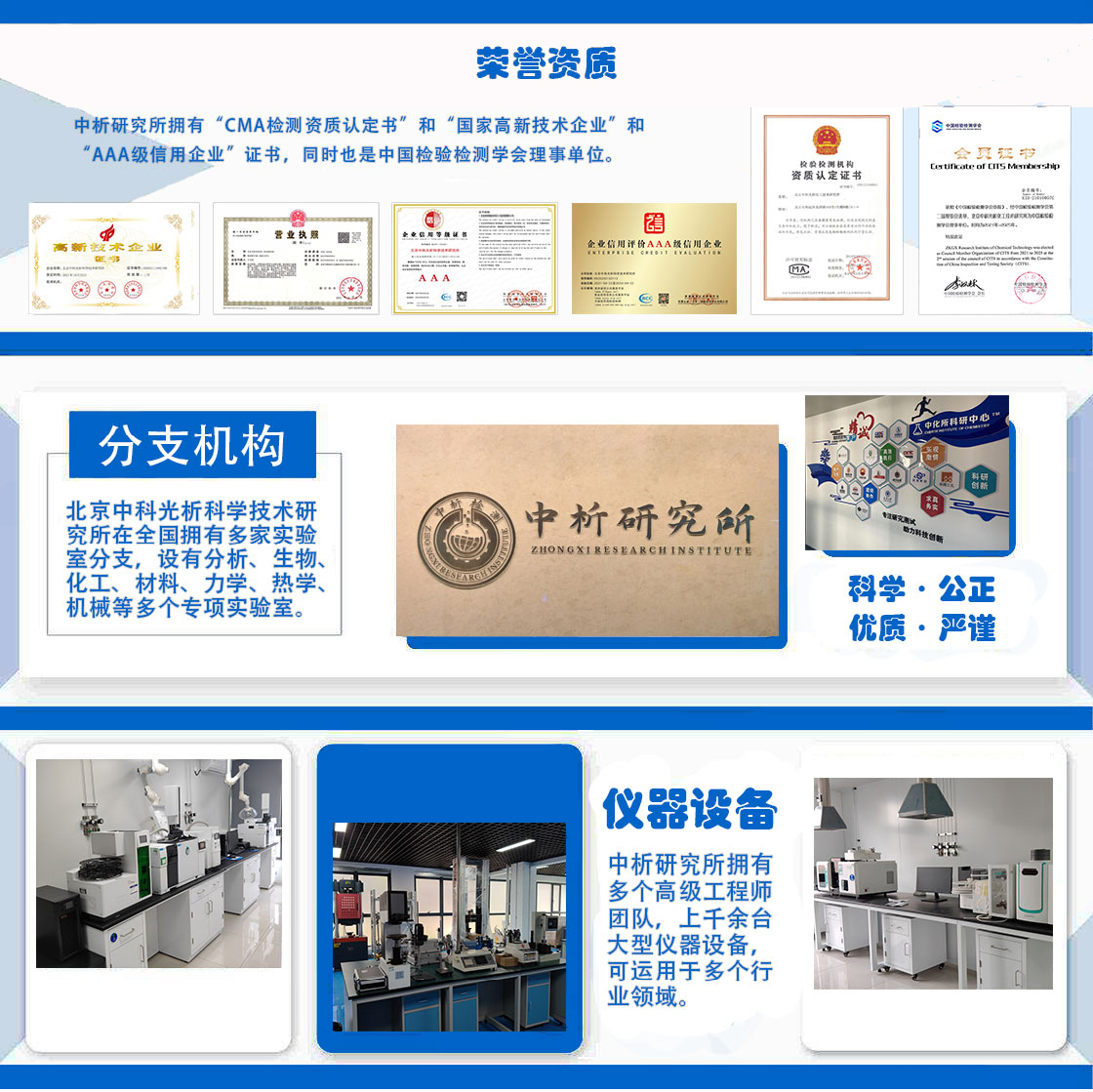
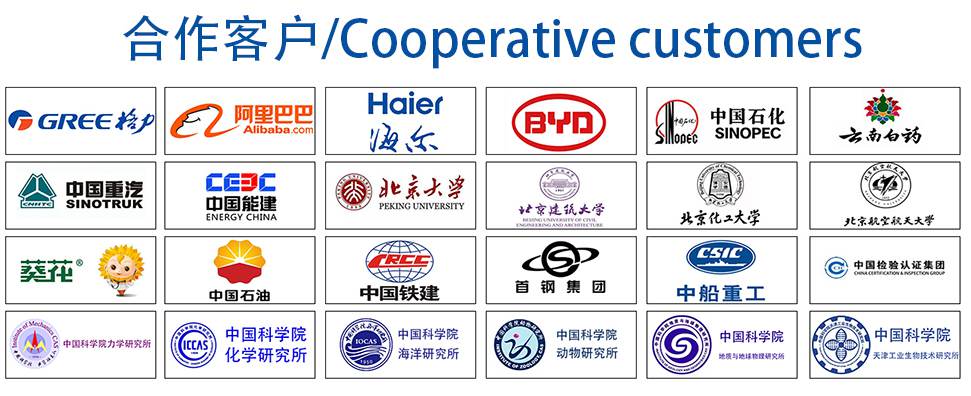