电力机车检测的重要性
电力机车作为现代轨道交通的核心动力设备,其运行安全性与可靠性直接关系到铁路运输效率和乘客生命安全。随着电力机车技术向智能化、高效化方向快速发展,检测项目已成为保障机车性能的关键环节。通过系统化、标准化的检测流程,能够及时发现潜在故障、优化设备寿命,并满足日益严格的环保与能耗要求。无论是日常维护还是大修周期,检测工作都需要覆盖动力系统、电气装置、机械结构等多个维度,以确保机车在复杂工况下的稳定运行。
核心检测项目分类
1. 动力系统检测
动力系统是电力机车的"心脏",检测重点包括牵引电机性能测试、变流器效率分析及高压线路绝缘强度验证。通过振动频谱分析、温升试验和动态负载测试,评估电机轴承状态与散热能力。同时需使用兆欧表检测高压电缆绝缘电阻,确保其在25kV高压环境下的安全性。
2. 制动系统功能性检测
采用气压传感器与制动距离测量装置,验证电空联合制动系统的响应时间和制动力分配精度。重点检测制动闸片磨损量、空气管路泄漏率以及防滑控制系统的动态调节能力,确保紧急制动时减速梯度符合GB/T 3317标准要求。
3. 车载电气设备检测
涵盖主变压器油色谱分析、IGBT模块开关特性测试及辅助电源谐波检测。使用红外热成像仪扫描电气柜连接点温度分布,结合电能质量分析仪评估电磁兼容性。特别关注高压隔离开关接触电阻值,要求不超过设计标准的15%。
4. 车体与转向架结构检测
采用三维激光扫描技术检测车体变形量,运用磁粉探伤检查转向架构架裂纹。通过落锤试验验证车钩缓冲装置吸能性能,并测量轮对踏面磨耗深度及轮径差,确保其符合UIC 510-2规范限值。
5. 智能控制系统验证
对TCMS(列车控制管理系统)进行黑盒测试与故障注入试验,验证网络通信的实时性与冗余切换可靠性。使用HIL(硬件在环)仿真平台模拟极端工况,检测牵引/制动指令的协同控制精度,要求响应延时不超过50ms。
6. 环境适应性检测
在高温、高湿、盐雾等环境舱内开展72小时持续运行试验,检测绝缘材料老化速率与金属部件腐蚀情况。同时进行-40℃低温启动测试,验证蓄电池组容量保持率需达到额定值的85%以上。
齐全检测技术的应用
现代电力机车检测已引入PHM(故障预测与健康管理)系统,通过安装500+个传感器实时采集数据。结合数字孪生技术构建虚拟样机,实现关键部件的剩余寿命预测。车载检测设备与地面专家系统形成"车地一体"诊断网络,使故障定位准确率提升至98.6%。
检测标准与发展趋势
目前我国执行TB/T 3118-2018等系列检测标准,同时逐步与国际铁路联盟(UIC)规范接轨。未来检测技术将向智能化、无人化方向发展,基于5G的远程在线检测和AI驱动的故障模式识别技术正在测试验证阶段,预计可将检测效率提升40%以上。
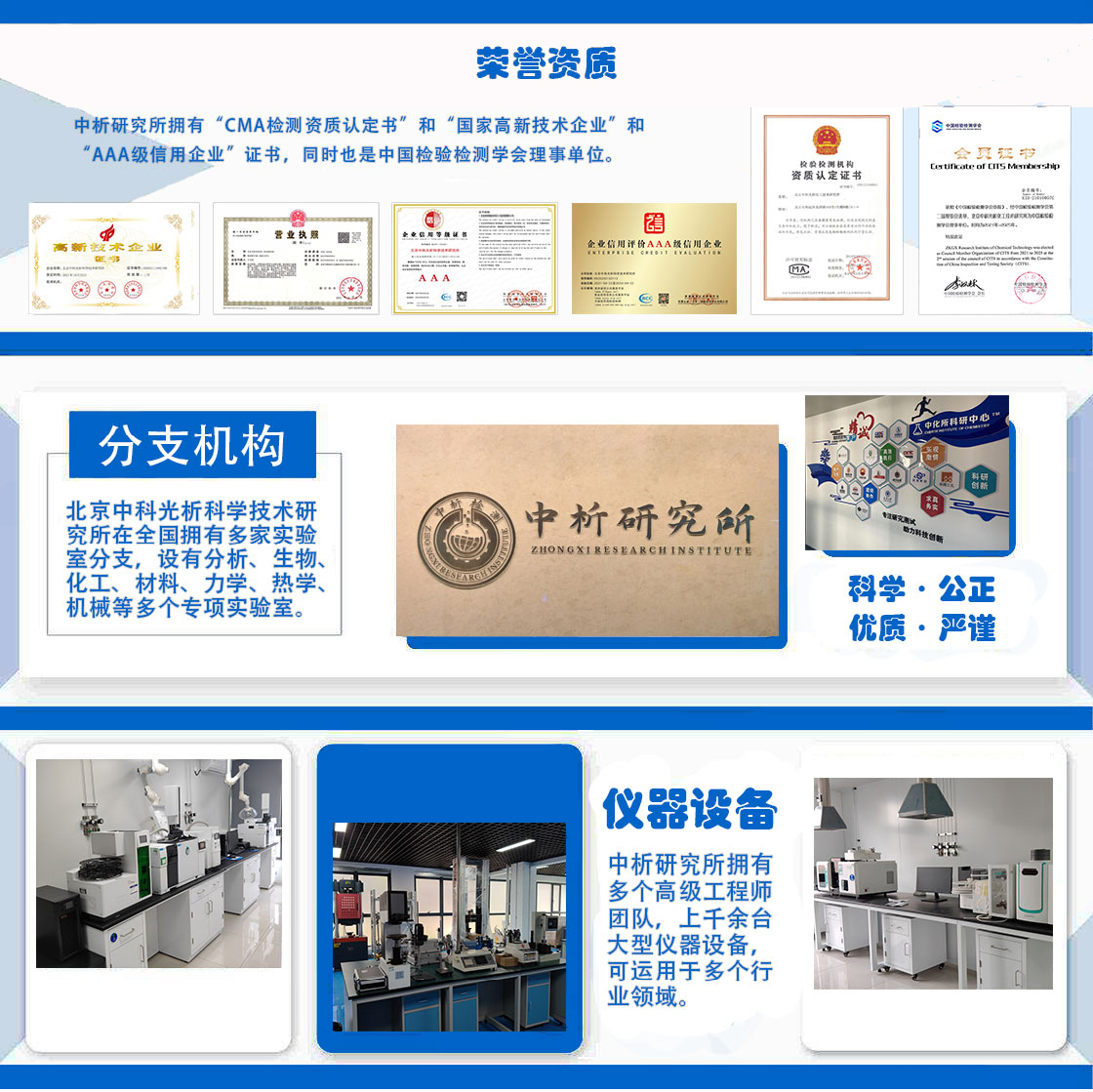
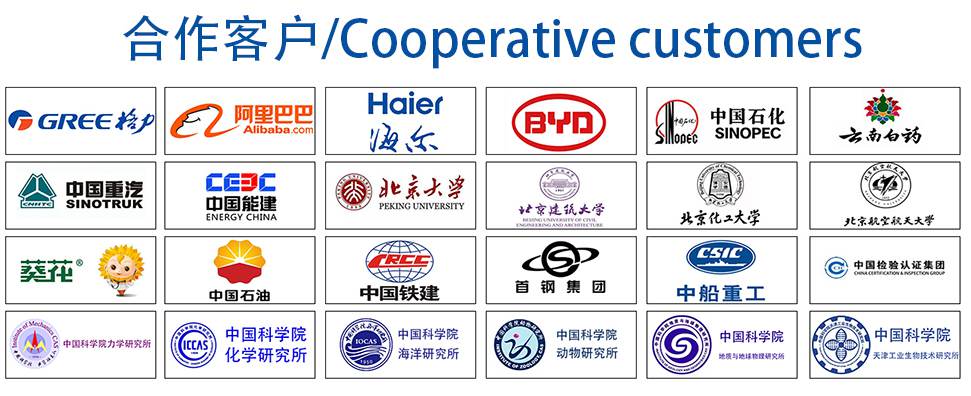