机车、动车空气管路用橡胶软管检测的意义与标准
在铁路运输系统中,机车与动车的空气制动管路承担着传递制动压力、保障行车安全的核心功能。作为管路系统中的关键部件,橡胶软管因其柔韧性、耐压性和密封性被广泛应用于连接不同设备。然而,橡胶材料在长期使用中易受温度变化、油液侵蚀、机械振动等因素影响,可能产生老化、龟裂或变形等问题,进而引发泄漏甚至制动失效等安全隐患。因此,严格执行橡胶软管的定期检测与质量评估,是确保轨道交通运营安全的重要环节。根据《铁路机车车辆空气制动橡胶软管技术条件》(TB/T 3138)等标准规范,检测项目需覆盖材料性能、结构完整性及环境适应性等多维度指标。
核心检测项目及技术要求
1. 材料性能检测
橡胶软管的胶料需通过拉伸强度、断裂伸长率、硬度等基础力学测试,确保材料符合耐压需求。同时需进行热空气老化试验(70℃×72h)、耐油性能试验(IRM903油浸泡23℃×24h)和臭氧老化试验(50pphm×40℃×72h),验证其抗老化能力。测试后性能衰减率不得超过标准限值,例如拉伸强度变化率应≤±20%。
2. 密封性与耐压测试
通过静态压力试验(1.5倍工作压力保压3min)和脉冲压力试验(模拟实际工况循环加载),检测软管接头与管体的密封可靠性。试验过程中不得出现泄漏、鼓包或永久性变形,且压力衰减幅度需低于5%。针对高速动车组用软管,还需增加振动疲劳测试,模拟运行中的高频振动环境。
3. 低温弯曲性能评估
将软管在-40℃低温环境下冷冻24小时后,以管径10倍的弯曲半径进行180°弯折,观察表面是否产生裂纹或分层。此项目验证软管在极寒地区的适用性,避免因低温脆化导致管路破裂。
4. 爆破压力测试
逐步加压至软管爆破,实测爆破压力需≥4倍额定工作压力。通过该测试可验证管体结构设计的冗余度,确保在极端工况下的安全余量。
5. 外观与尺寸检验
采用高精度测量工具检查软管内径、壁厚及总长度的公差范围(通常要求±1.5%以内)。表面须无气泡、杂质、划痕等缺陷,编织层或缠绕层分布均匀无松散。
检测流程与质量控制要点
检测需遵循“批次抽样-实验室测试-现场验证”相结合的原则。对于新供货批次,应按GB/T 2828.1进行抽样;在用软管则结合运行里程制定抽检周期。重点监控接头扣压工艺质量,防止因装配不良导致的早期失效。检测数据需通过数字化平台建档,实现全生命周期追溯管理。
结语
机车与动车空气管路橡胶软管的检测不仅是技术规范的执行过程,更是保障铁路运输安全的重要防线。通过建立涵盖材料、结构、环境适应性的多维度检测体系,结合智能化的数据管理手段,可有效预防管路系统故障,为轨道交通的高效运营提供坚实支撑。
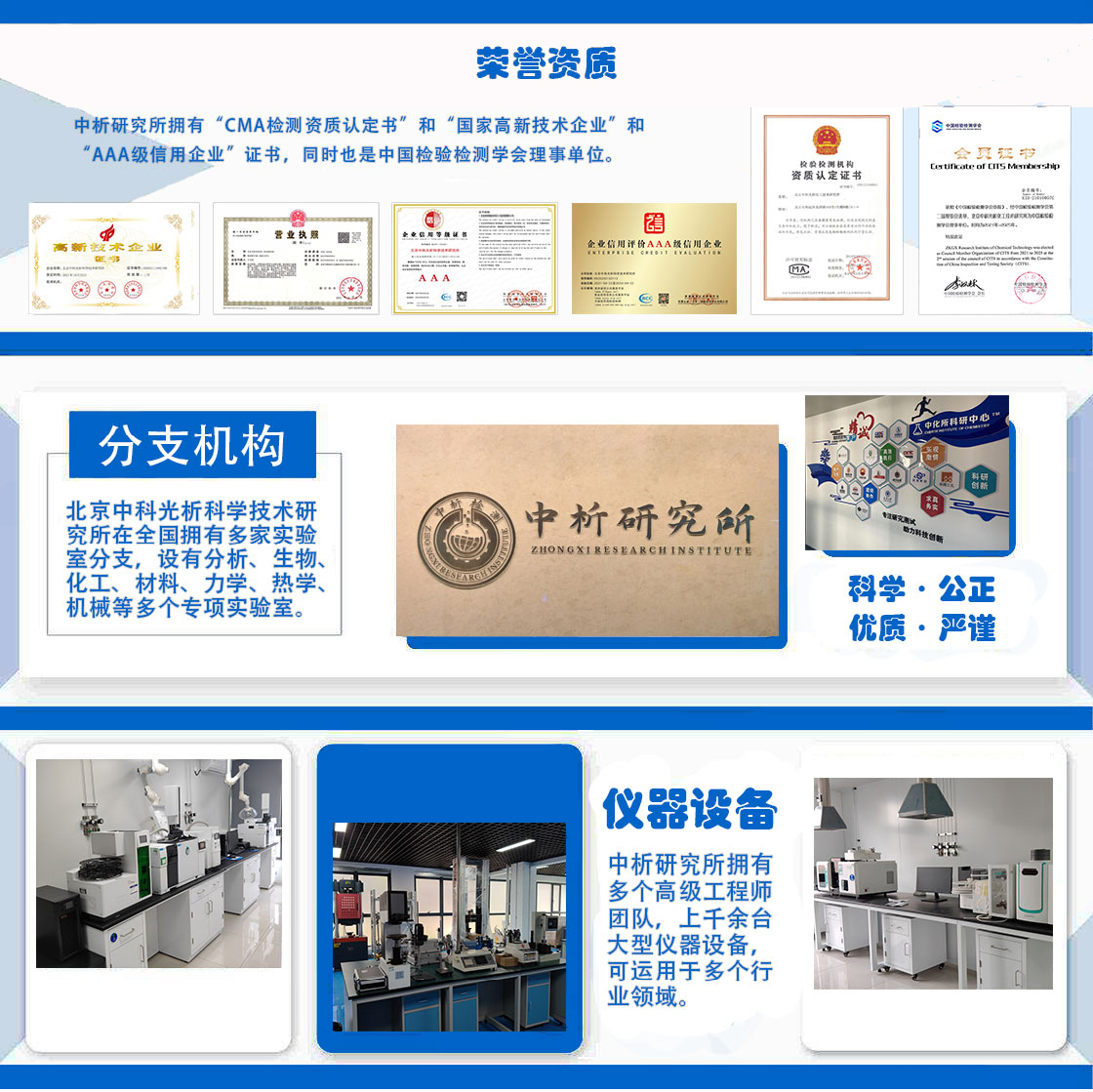
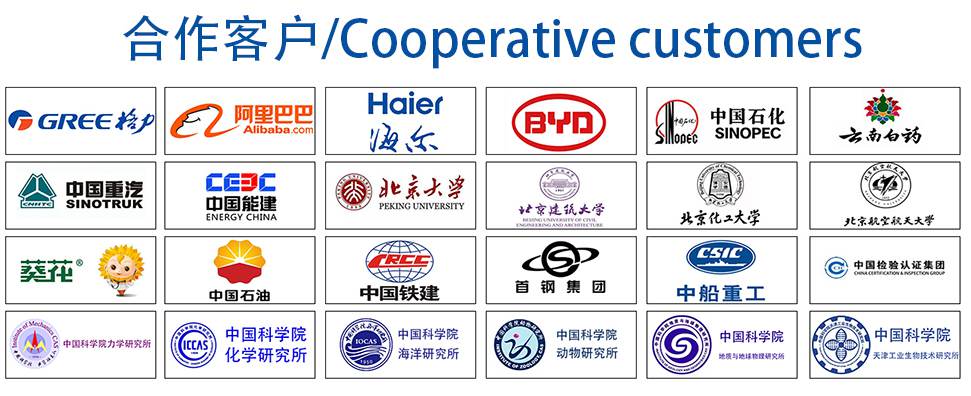