浸泡水腐蚀参数检测的意义与应用场景
浸泡水腐蚀参数检测是评估材料在液态环境中耐腐蚀性能的核心技术手段,广泛应用于船舶制造、海洋工程、石油化工、输水管道等领域。通过模拟材料长期浸泡于水环境(包括淡水、海水或特定溶液)的条件,系统分析其腐蚀速率、表面形貌变化及化学稳定性,为材料选型、防腐工艺优化和设备寿命预测提供科学依据。随着对基础设施耐久性要求的提升,该检测已成为ISO、ASTM等国际标准及GB/T国家标准的强制性验证项目。
主要检测参数体系
1. 腐蚀速率:通过失重法或电化学法计算单位时间内材料厚度损失,国际通用单位为mm/a(毫米每年)。
2. 质量变化率:精准测量浸泡前后样品重量差值,适用于评估均匀腐蚀程度。
3. 表面形貌分析:采用SEM(扫描电镜)观测点蚀、裂纹等局部腐蚀特征,结合EDS能谱分析腐蚀产物成分。
4. 溶液参数变化:监测pH值、电导率、溶解氧等溶液指标变化,判定材料腐蚀的化学动力学过程。
5. 电化学参数:通过极化曲线测试获取腐蚀电位、腐蚀电流密度,利用EIS(电化学阻抗谱)分析界面反应机制。
标准化检测流程与方法
依据ASTM G31标准,典型检测流程包括:试样制备→溶液配制→恒温浸泡→周期性取样→表面清洗(按ASTM G1去除腐蚀产物)→数据采集。常用方法组合包括:
• 浸泡试验箱法:模拟真实环境进行长期暴露试验(通常28-90天)
• 电化学工作站:快速获取Tafel曲线和Nyquist图谱
• 加速腐蚀试验:通过温度、压力、搅拌等参数加速腐蚀进程
• XRD/XPS联合分析:精确鉴定腐蚀产物晶体结构及元素价态
关键质量控制指标
国际通行的验收标准要求:
• 碳钢在3.5% NaCl溶液中年腐蚀率≤0.1mm
• 不锈钢点蚀电位需高于+200mV(vs.SCE)
• 涂层体系需通过2000小时盐雾试验无起泡
• 铝合金的晶间腐蚀深度应<50μm
检测技术创新方向
当前行业正推进:①微型传感器原位监测技术 ②基于机器学习的腐蚀预测模型 ③多因素耦合试验装置(温度+压力+流速) ④符合ISO 20340标准的循环老化测试。这些技术突破使检测周期缩短40%,数据精度提升至微米级,特别适用于深海管线、核电站冷却系统等严苛环境下的材料评估。
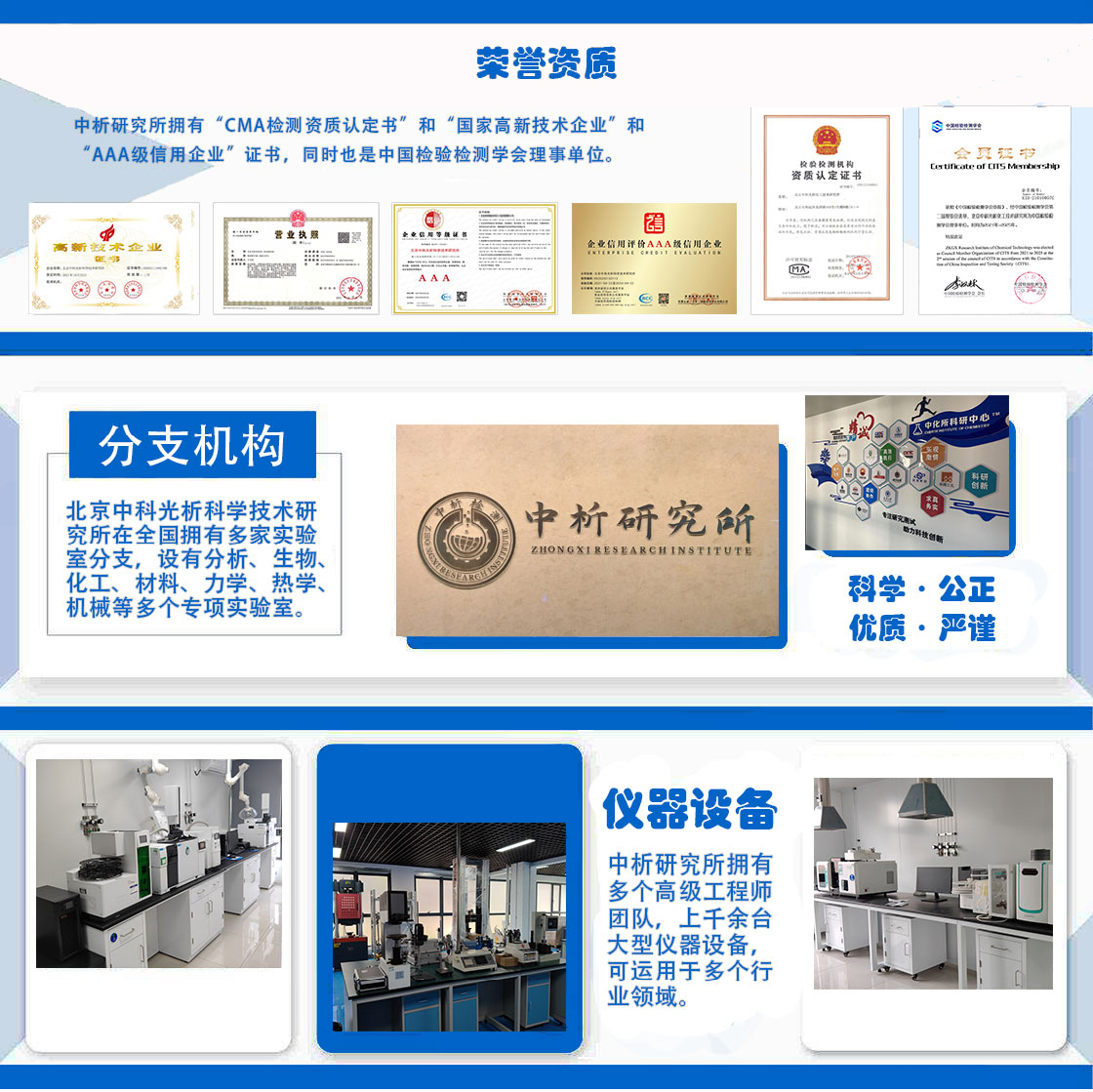
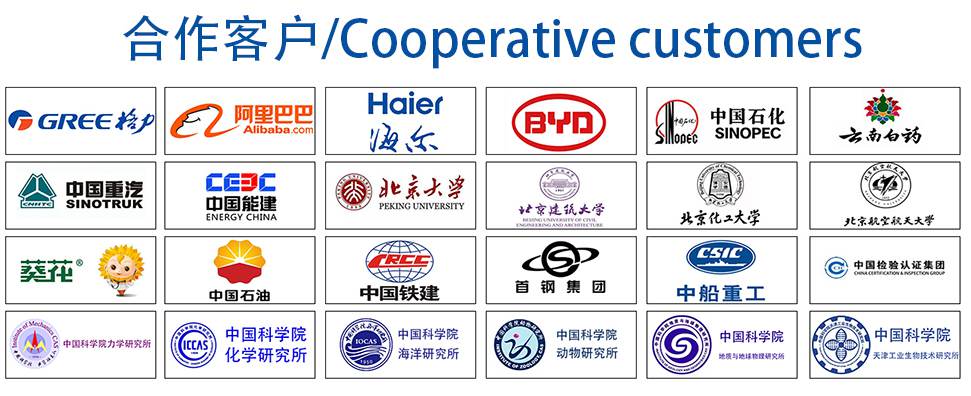