机床检测的核心项目与技术解析
在精密机械加工领域,机床作为核心生产设备,其性能精度直接决定了产品质量和生产效率。机床检测是通过系统化测试手段验证设备状态的核心工序,包含几何精度、动态性能、电气系统等六大关键检测维度。
一、几何精度检测
作为机床检测的基础项目,主要采用激光干涉仪、球杆仪等设备测量:主轴径向跳动(≤0.005mm)、工作台平面度(0级精度要求≤0.01mm/m)、导轨直线度(允许误差0.015/1000mm)等参数。特别需注意温度补偿,20℃标准环境下测量值需换算补偿0.008mm/℃的膨胀系数。
二、动态性能检测
包含振动频谱分析(FFT频宽0-1000Hz)、主轴温升测试(连续运转4小时温升≤25℃)、噪声检测(A计权声压级≤75dB)等项目。使用加速度传感器和红外热像仪采集数据时,需在XYZ三轴方向分别进行空载/负载对比测试。
三、数控系统检测
重点验证伺服驱动性能:位置环响应时间≤2ms、速度波动率<±0.1%、反向间隙补偿(重复定位精度达到±0.002mm)。通过示波器监测编码器反馈信号时,需特别关注电子齿轮比设置与理论值的偏差。
四、切削能力验证
采用标准试件法进行综合测试:包含圆度误差(≤0.005mm)、表面粗糙度(Ra≤0.8μm)、轮廓精度(三维扫描偏差<0.02mm)等指标。45#钢试件建议选用φ50×100mm规格,切削参数参照机床额定功率的80%设定。
五、安全性能检测
涵盖急停响应时间(≤0.5s)、防护罩联锁功能、漏电保护(绝缘电阻≥1MΩ)等项目。使用PLC信号分析仪检测安全回路时,需模拟断刀、过载等16种故障模式验证保护机制。
六、能耗效率评估
新型检测项目包含空载功率(≤额定功率15%)、能效指数(EEI≥85%)、液压系统泄漏量(<5ml/min)等指标。采用功率分析仪连续监测72小时,结合MTBF(平均无故障时间)计算设备综合效率OEE。
通过上述检测体系的实施,可将机床精度保持周期延长30%,减少50%的非计划停机。建议企业建立每500小时/次的周期性检测制度,结合ISO 230-2:2014标准建立数字化检测档案,为智能制造转型提供设备保障基础。
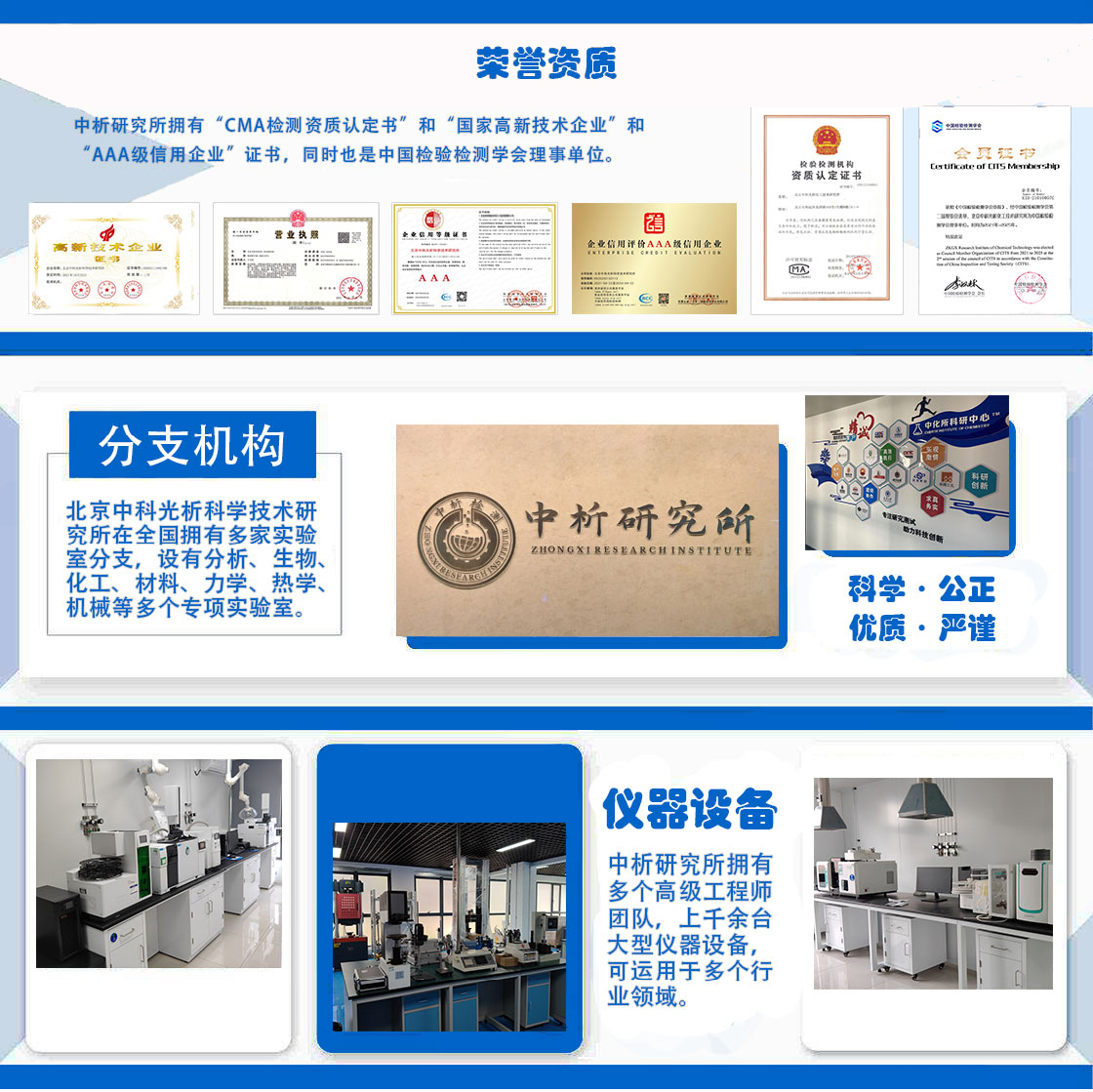
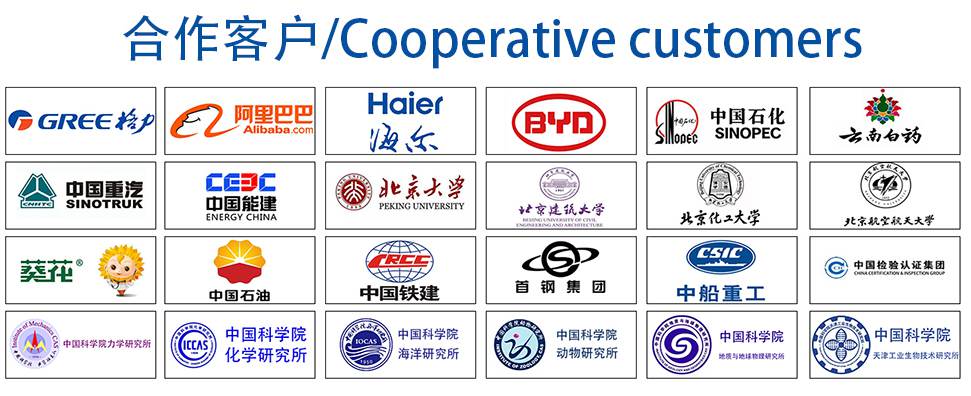