储罐检测的重要性与核心内容
储罐作为石油、化工、能源等行业中储存液体或气体的关键设备,其安全性与可靠性直接关系到生产安全和环境保护。由于储罐长期暴露在复杂环境中,易受腐蚀、疲劳、沉降等因素影响,定期检测成为预防泄漏、爆炸、环境污染等事故的核心手段。通过系统化的储罐检测,可以及时发现潜在缺陷,评估剩余寿命,并为维修决策提供科学依据。根据行业规范(如API 653、NBIC等),储罐检测需涵盖结构完整性、材料性能、附属设施功能等多个维度,以确保其在整个生命周期内的稳定运行。
储罐检测的核心项目
1. 外观与结构检查
通过目视或辅助工具(如无人机、高清摄像头)对储罐外壁、焊缝、支撑结构进行全面检查,识别腐蚀、变形、裂纹等表面缺陷。重点关注罐顶、罐底边缘板等易损区域,并记录保温层、防腐涂层的破损情况。
2. 壁厚与腐蚀检测
使用超声波测厚仪(UT)或射线检测(RT)技术测量罐体及管道的剩余壁厚,评估均匀腐蚀或局部减薄程度。结合腐蚀速率计算,预测储罐的剩余使用寿命,并为后续维护计划提供数据支持。
3. 焊缝无损检测
对储罐主焊缝、接管焊缝等关键连接部位进行渗透检测(PT)、磁粉检测(MT)或相控阵超声检测(PAUT),检测未熔合、气孔、夹渣等隐蔽缺陷,确保焊缝的力学性能满足设计要求。
4. 基础沉降与几何变形评估
采用激光扫描或全站仪测量储罐基础的沉降量,分析罐体垂直度与圆度偏差,防止因地基不均匀沉降导致的应力集中或密封失效。
5. 附属设施功能测试
检查呼吸阀、紧急泄放装置、液位计、防雷接地系统等安全附件的有效性,验证紧急切断阀的响应速度以及消防设施的联动功能,确保在异常工况下能快速启动保护机制。
6. 内部涂层与衬里检测
对于有内防腐层或衬里的储罐,通过内窥镜或电火花检测仪评估涂层完整性,检测剥离、鼓包或针孔缺陷,避免介质直接接触罐体导致加速腐蚀。
7. 材料性能分析
通过金相分析、硬度测试、化学成分检测等手段,评估储罐材料是否发生劣化(如氢脆、应力腐蚀开裂),尤其适用于高温、高压或腐蚀性介质环境下的老旧储罐。
8. 泄漏与密封性检测
利用氦质谱检漏、压力衰减测试或红外热成像技术,检测罐体、法兰、阀门等部位的微量泄漏,并结合真空箱试验验证罐底焊缝的密封性能。
检测周期与风险管理
根据储罐的介质特性、设计寿命和运行环境,检测周期通常为3-10年。高风险储罐(如存储有毒或易燃物质)需缩短检测间隔,并结合在线监测系统(如声发射、腐蚀探针)实现实时预警。检测数据应纳入完整性管理平台,通过风险矩阵评估缺陷的危害等级,制定分级管控措施。
结语
储罐检测是一项多学科交叉的综合性技术工作,需结合现场经验与齐全检测手段,形成“预防为主、检维修结合”的管理模式。通过科学规划检测项目,企业不仅能避免重大安全事故,还可降低运维成本,延长储罐服役周期,为可持续发展提供保障。
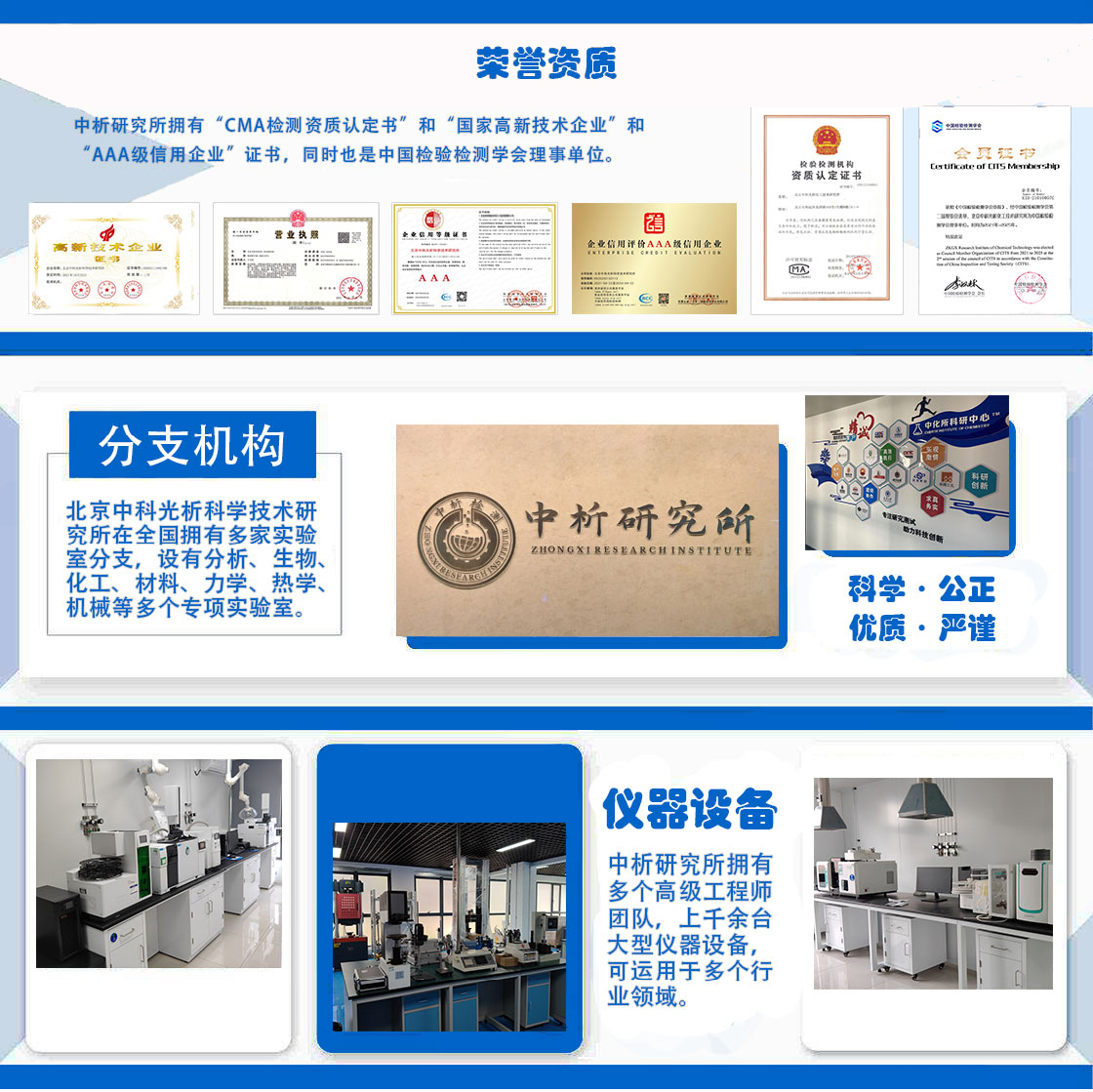
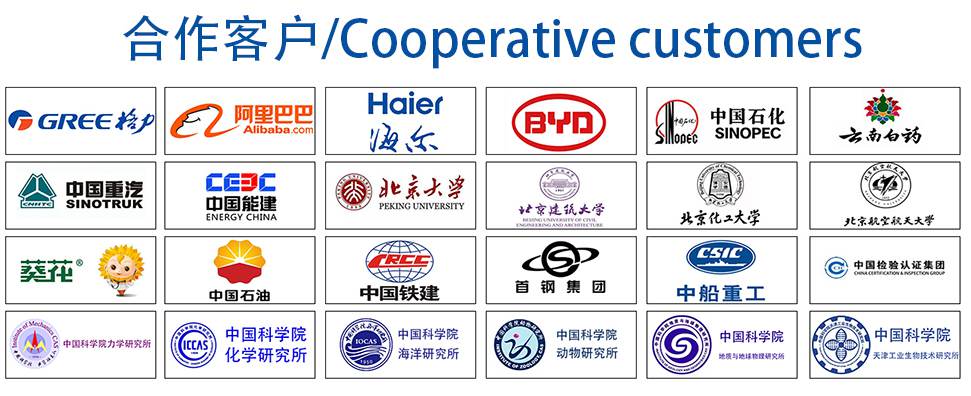