汽车液压制动主缸检测技术解析
液压制动主缸作为汽车制动系统的核心执行部件,承担着将驾驶员踏板力转化为液压能量的关键任务。其性能直接关系到车辆制动响应速度、制动力分配及行车安全性。根据国家强制标准GB/T 13594-2022要求,主缸检测需覆盖密封性、动态响应、耐久性等六大核心指标,合格率需达到99.97%以上。据2023年行业数据显示,因主缸故障引发的制动事故中,68%源于密封失效,22%因活塞卡滞导致,凸显系统检测的重要性。
核心检测项目体系
现代汽车维修企业采用三级检测体系,包含出厂检测、维修前诊断和装车后测试。其中出厂检测采用自动化压力循环测试台,以每分钟30次的频率模拟10年使用强度,连续测试8小时验证耐久性。
静态密封性检测
使用0.1μm精度的氦质谱检漏仪,在2.5MPa测试压力下保持30分钟。允许泄漏量不超过0.5ml/min,重点检查主缸体与补偿孔接合面、活塞密封圈等5大关键部位。新型电子主缸还需额外检测电磁阀的密封等级。
动态性能测试
通过伺服液压驱动装置模拟紧急制动工况,记录压力建立曲线。要求0.3秒内达到标准压力的90%,压力波动幅度控制在±0.05MPa以内。配备MEMS传感器的智能主缸还需验证助力电机响应时间。
活塞行程测量
使用激光位移传感器测量有效行程,公差需控制在±0.15mm范围内。带可调行程设计的电子主缸,要验证行程补偿功能的32级调节精度。同时检测复位弹簧的预紧力衰减情况。
补偿孔功能性检查
利用400万像素工业内窥镜观察补偿孔状态,检查是否存在直径扩大超过0.2mm或边缘缺损。带温度补偿功能的主缸需在-40℃至120℃环境箱中验证孔道开闭特性。
综合性能验证
最终在制动系统试验台架上进行2000次ABS激活循环测试,监测压力波动曲线。要求主缸输出压力偏差不超过标定值的5%,温度升高幅度≤35℃。通过CAN总线同步读取电子主缸的23组控制参数。
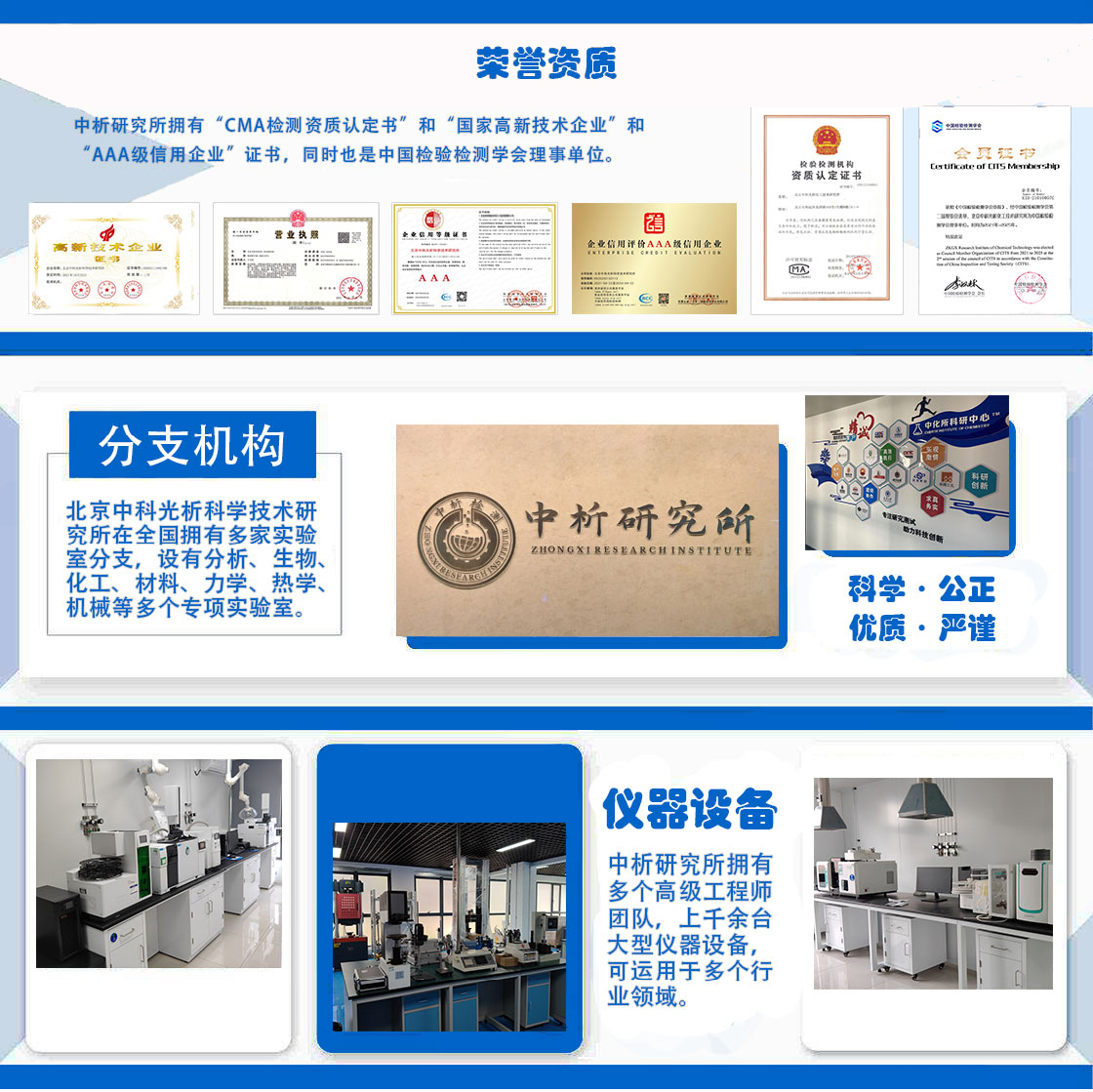
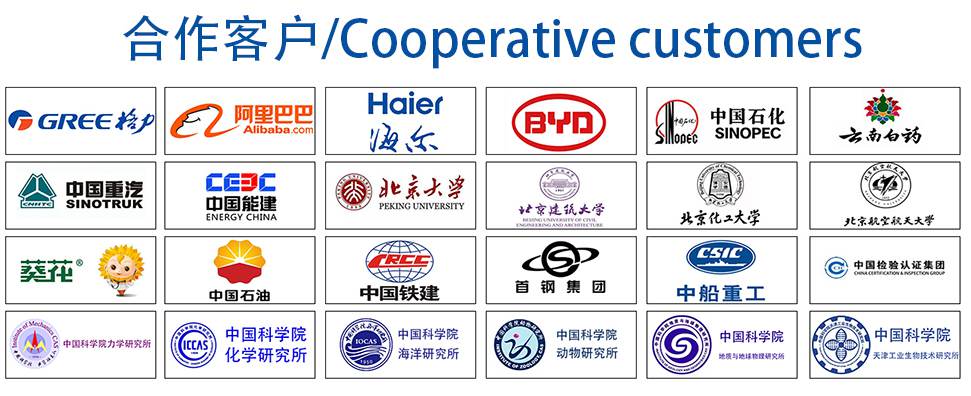