动车组轴箱轴承检测的重要性与挑战
作为高速铁路列车的核心承载部件,动车组轴箱轴承直接关系到列车运行安全与稳定性。每套轴箱轴承需承受高达数吨的动载荷,在持续高速运转中经历复杂的热-力耦合作用。据统计,轴承故障占转向架系统故障的37%以上,其中疲劳剥落、润滑失效和装配误差是主要失效模式。随着列车运行时速突破350km/h,传统检测手段已难以满足精准诊断需求,需要通过系统性检测项目构建多维度的健康评估体系。
核心检测项目体系
1. 外观与几何精度检测
采用工业内窥镜对轴承滚道、保持架进行可视化检测,识别表面划痕、点蚀等缺陷。使用三坐标测量机(CMM)检测轴承内径、外径、圆度等几何参数,精度需控制在±2μm范围内。特别关注轴承座配合面的表面粗糙度(Ra≤0.8μm)和同心度偏差(≤0.05mm)。
2. 振动与噪声分析
通过安装加速度传感器采集轴承振动频谱,运用包络解调技术分离特征频率。建立时域指标(RMS值、峰值因数)与频域指标(谐波成分、边带能量)的复合评价模型。依据EN12082标准,异常振动值超过基线30%即触发预警。
3. 温度场监测
采用红外热像仪实现非接触式温度场测绘,重点监控轴承外圈温升梯度。正常工况下温升应≤40℃,相邻测点温差不超过8℃。开发基于LSTM神经网络的温度预测模型,实现过热故障的早期识别。
4. 润滑状态评估
运用铁谱分析技术检测润滑油中的磨粒浓度与形态特征,当Fe元素含量>150ppm或出现>50μm的层状磨粒时判定异常。同步开展油脂锥入度测试(标准值220-250mm/10)和氧化安定性分析,确保润滑性能符合TB/T3317规范。
5. 材料性能测试
采用超声波探伤仪对轴承钢进行内部缺陷检测,可发现≥0.5mm的夹杂物。通过显微硬度计(HV≥700)和残余应力测试仪(表面压应力≥300MPa)验证热处理质量。开展滚动接触疲劳试验,模拟100万公里等效载荷下的材料耐久性。
智能检测技术突破
新型轴箱轴承检测体系融合了PHM(故障预测与健康管理)技术,部署多物理场传感器网络实现实时监测。基于数字孪生技术构建轴承三维动力学模型,通过虚拟标定提升故障诊断准确率。实践表明,该体系可将轴承故障漏检率降低至0.3%以下,平均维保周期延长40%。
随着量子传感、太赫兹检测等新技术的工程化应用,未来将实现纳米级缺陷识别和剩余寿命精准预测,为高铁装备可靠性提升提供坚实保障。
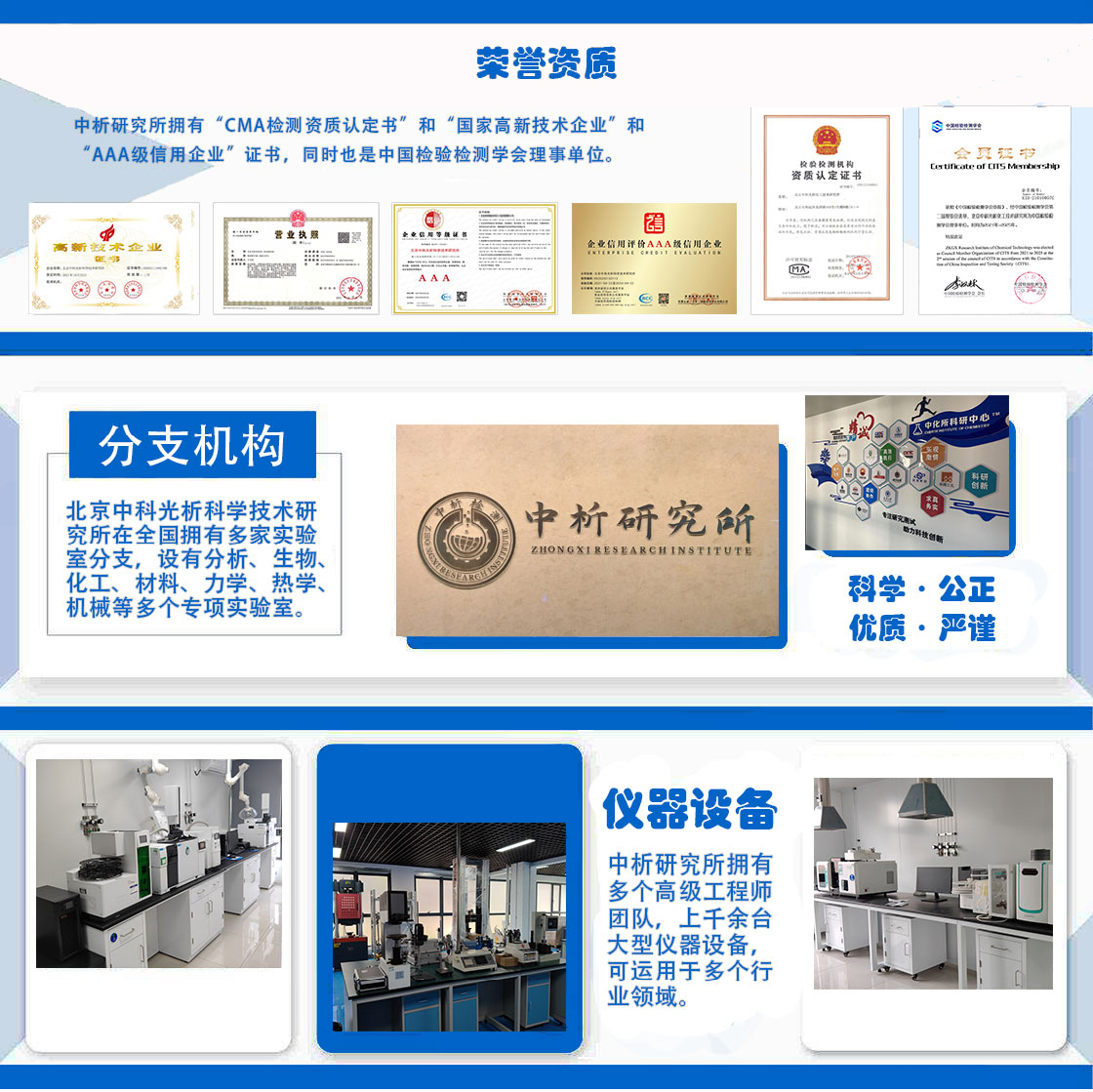
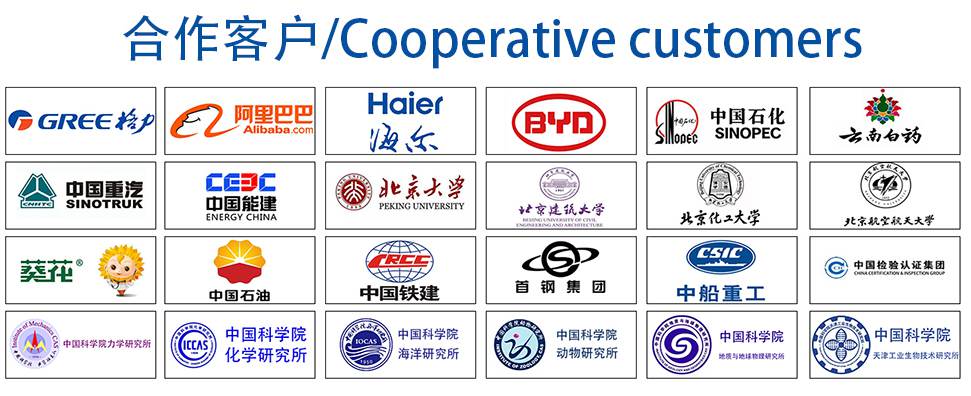